Boffis
International Hazard
   
Posts: 1867
Registered: 1-5-2011
Member Is Offline
Mood: No Mood
|
|
Commercial Calcium Cyanamide experiments
In an earlier series of threads in SM Engager described the preparation of calcium cyanamide and the fairly elaborate fabrication of the furnace to
prepare it. He went on to describe the preparation of aminoguanidine bicarbonate, 5-aminotetrazole and derivatives there-of from it. However, in
recent years industrial grade calcium cyanamide has started to appear in gardening supply shops in several European countries under the trade name
“Perlka cyanamide”. It take the form of hard black shot 2-4mm in diameter that claim to be approximately 55% calcium cyanamide and comes in small
buckets or sacks up to 25kg for as little as 1.50 € a kg. Given this improving availability it seems worth investigating what can be made from it.
The following experiments were very preliminary attempts to determine its practical utility.
The small spherical shot is hard, though brittle, and grinding it to a powder is difficult without a small ball mill. In order to avoid this problem
experiments to decompose it directly where undertaken.
It was found that 80% acetic acid rapidly decomposes the material with the evolution of significant heat. The black porridge that results was
extracted with water to give an aqueous solution of calcium acetate and free cyanamide. If the filtered solution is treated with strong sodium
carbonate solution until all of the calcium has precipitated then filtered quickly the cyanamide should remain in solution. If further sodium
carbonate is added to raise the pH to 8-9 and then the solution boiled dicyandiamide crystallises on cooling but the yield was rather low. The usual
method of preparing free cyanamide is to decompose the industrial calcium cyanamide with acetic acid and then extract the moist crumbly mass with
ether, however, being short of ether at present isopropanol was used. This solvent extracts a considerable amount of calcium acetate too and if only a
little solvent is used the whole mass gels, this complicated the conversion of cyanamide to dicyandiamide or the recovery of the free cyanamide. The
conversion of cyanamide to the much less soluble dicyandiamide is catalysed both by acids and alkalis but the addition of sodium carbonate or
sulphuric acid causes a precipitate of the appropriate Ca salt. The carbonate is preferred because the calcium carbonate is more completely
precipitated and the alkaline conditions maximise the conversion to dicyandiamide. Acids convert cyanamide to dicyandiamide too but there is
significant conversion to urea, melamine and other difficult to separate triazine derivatives. Hydrochloric acid may work too and the calcium chloride
would remain in solution simplifying the work up; this has not yet been tried but acid hydrolysis to urea etc. would still be a problem.
The industrial process (see attached file by Sankaranarayanan) uses dilute sulphuric acid for this process and neutralise and precipitate the
remaining calcium and acid with sodium carbonate solution then recover the dicyandiamide with a little melamine etc. by cooling the filtrate. The
calcium cyanamide shot seems to break up and decompose reasonably well in dilute sulphuric acid and through prolonged boiling with water. Future
experiments will look at the decomposition simply by boil with water while adding carbon dioxide. 100g of commercial calcium cyanamide should give
about 26 to 28g of cyanamide or dicyandiamide, the latter is less soluble but still dissolves to the extent of about 40g/l at room temperature so with
100g of calcium cyanamide and 700-800ml of water the products should remain in solution and can be recovered by filtration and evaporation.
The most successful experiment to date in this field was the direct conversion of the black calcium cyanamide into aminoguanidine bicarbonate. The
process was basically that described by Engager with slight modifications but it is clear that in order to improve the yield further significant
modifications will be required. The main issue is the slow rate of the Perlka shot type cyanamide without first grinding it; this results in a low pH
for most of the reaction time rising above 7 only towards the end and only a little sulphuric acid was required to lower the pH to 6.5 prior to
precipitation of the aminoguanidine as bicarbonate. Two possible routes to overcoming this problem exist; firstly and most obviously is to ball-mill
the calcium cyanamide to increase its reactivity or secondly to add the hydrazine sulphate (which is actually hydrazinium hydrogen sulphate) is small
quantities only when the pH rises to 9 or above. A third, less practical, possibility may be to decompose the calcium cyanamide shot with acetic acid
and then react this with dihydrazinium sulphate which is much more soluble and much less acid; any pH adjustment then being carried out with either
sulphuric acid or sodium carbonate as appropriate.
Experimental:
1) Aminoguanidine bicarbonate
55g of hydrazine sulphate were dispersed into 200ml of water and 55g calcium cyanamide shot were added. The mixture was stirred and warmed to 40°. It
was found to be rather acidic with an initial pH of 4 so a further 25g of finely ground calcium cyanamide (ground in a pestle and mortar, hard work!!)
was added and this rapidly raised the pH to 7 over a few minutes. On heating the pH of the solution reached 10 but require only a little 8M sulphuric
acid to adjust the pH to 9. After 30 minutes the pH was adjusted 7 requiring about 7.5ml of 8M sulphuric acid. The slurry was kept at 80°C for 1 hour
and then cooled to about 50°C and the pH adjusted to 6.5 with a little sulphuric acid and filtered. Filtration was difficult even with a large
Buchner funnel and the first 70-80 ml of filtrate contained suspended carbon and had to be returned to the Buchner funnel and flushed through with a
little wash water (about 50ml).
The final filtrate was a clear pale amethyst colour. This was treated with sodium bicarbonate until no further precipitate formed, 45g were required
suggesting that the solution was a little too acidic a fact borne out by the effervescence that occur initially. The slightly off-white precipitate
was filtered using a 7cm Buchner funnel but not washed on the filter as the precipitate was very fine and filtered slowly. The cake was transferred to
a 250ml beaker and dispersed into 150ml of water and filter on a 9cm Buchner funnel, washed with methanol and sucked as dry as possible and turned out
on to a 12cm watch glass to dry. It took more than 2 days at 30°C to reach a constant weight even with periodic breaking up of the pieces (note 1).
The dry product was powder to give 22.74 g of pure white product (about 40% of theory based on hydrazine sulphate; rather poor by Engager's
standards).
Note 1, bicarbonates are notoriously heat sensitive and tend to break down to carbonate, carbon dioxide and water at low temperatures so I dare not
attempt to dry it at a higher temperature.
Attachment: Dicyandiamide and Guanylurea sulphate from Calcium cyanamide J unknown Sankaranarayanan & Sen 1943.pdf (349kB) This file has been downloaded 634 times
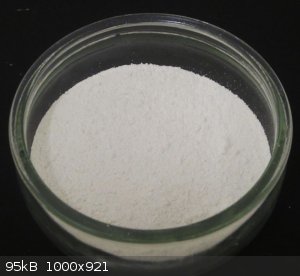
Aminoguanidine bicarbonate final product
|
|
dimroth
Harmless
Posts: 2
Registered: 8-7-2014
Location: Croatia
Member Is Offline
Mood: No Mood
|
|
I conducted similar experiments in order to obtain aminoguanidine bicarbonate (AG) as an precursor for synthesis of different 1,2,4-triazoles. I
stumbled across a few drawbacks of this commercial-CaCN2-route which ended in decision to explore other similar syntheses that can be used
to convert commercial CaCN2 into useful compounds. The second compound was already mentioned dicyandiamide (dicy) which I obtained more
simply and in greater yields than AG. Nevertheless, it's still a good route to AG since fertilizer is cheap and hydrazine sulphate is easily made in
large quantities.
Experimental AG
Commercial CaCN2 fertilizer "Cvetal Agrostrun" (slovenian producer) was bought. Somewhat more expensive, around 4,5€ for 1 kg. Same
characteristics, hard black shots with a slight ammonia smell. Description says 19,8% of nitrogen which comes to calculation that there is 56,6% of
CaCN2 (other components being mostly Ca(OH)2 and carbon). In the first experiment shots were ground using pestle and mortar
(hard work indeed!) and in the second, ball mill was used to obtain a fine powder. First problem - even ball mill grinding takes time and the material
sticks to the grinding medium and walls of cylinder. I haven't yet cleaned the cylinder but it seems it'll be quite a job to return it to previous
shape. Therefore I recommend to use one cylinder and medium specifically for grinding CaCN2.
Procedure was followed from [1] which it seems is the same as Boffis used.
20 g (0,1537 moles) of hydrazine sulphate and 22 g (0,1554 moles) of ground CaCN2 fertilizer were dry mixed. The mixture was slowly added
into 72 ml of water with stirring. pH was raised to around 9 by 6M NaOH and the slurry was heated to 40°C and stirred at this temperature for 30 min.
pH was adjusted to 7 with 50% sulfuric acid and the slurry was then heated to 80°C and held at that temp. for 1 hour. Thereafter it was cooled then
filtered. It was washed few times with water. Amethyst colored filtrate was returned to stirrer and NaHCO3 was added. At first
CO2 releases since solution is obviously somewhat acidic but then a cloudiness appears from precipitated AG. Solution changes color from
amethyst to slightly yellow. AG was vacc. filtered (takes time - very fine precipitate) and washed with water several times. AG was dried in the oven,
for what I now see was a mistake. A dark red coloration appeared on the edges of the crucible.
Stoichiometric quantities of NaHCO3 were used during addition but since solution was acidic I decided to add a little more.
NaHCO3 is also sparingly soluble in water as AG so any surplus gets in the AG precipitate in which it is then hard to wash it off. I
concluded that my AG is definitely not pure but contains a considerable amount of NaHCO3. I analysed my product gravimetricaly and by
titration but now by knowing AG decomposes very easily during drying, results does not matter.
Experimental AG (2)
Scale was 3-fold from previous exp., 60 g hydrazine sulfate and 66 g of fertilizer. NaOH was not used. AG precipitate was mistakenly dried again in
the oven. Result 25 g of off-white powder which accounts for 40% yield (based on hydrazine sulfate).
There are quite a few things that could be done to hopefully achieve better results:
1) as [1] suggests, AG could be precipitated with bubbling CO2. This results not necessarily in better yield but purer product. Or at least
adding stoichiometrical quantities of NaHCO3 and then bubbling CO2.
2) non-oven drying, maybe just holding it for enough time in exicator? I haven't washed my precipitate with solvent but it seems it could be a good
thing to do.
3) getting rid of iron contaminants present in commercial fertilizer which may influence yield? In [1] iron is rid off to get purer and whiter AG.
Scaffhausen [2] uses similar procedure and even mentions usage of commercial CaCN2 which is ground to 200 mesh but uses hydrazine hydrate
instead of hydrazine sulfate.
Reference
1. Simons, P. US Patent 3673253, Process for the production of aminoguanidine bicarbonate, 1972.
2. Schaffhausen, J. G. US Patent 4906778, Process for the production of aminoguanidine bicarbonate, 1990.
|
|
Boffis
International Hazard
   
Posts: 1867
Registered: 1-5-2011
Member Is Offline
Mood: No Mood
|
|
I recently had time to investigate the aminoguanidine bicarbonate prepared above. Working on the basis that the most likely impurity is sodium
bicarbonate decomposed roughly 0.1g in a small pre-weighed crucible until all of the guanidine has been removed and the sodium is left as the simple
carbonate. This revealed that the sodium bicarbonate concnetration must have been over 35% or just over 64% aminoguanidine bicarbonate. The residue
contained a little brown material (iron oxide?) and some insoluble/sparingly soluble material, possibly calcium sulphate, too. This was
disappointingly poor and reduces the "real" yield to only about 25%. Could do better!
|
|
|