Pages:
1
2 |
Hennig Brand
International Hazard
   
Posts: 1284
Registered: 7-6-2009
Member Is Offline
Mood: No Mood
|
|
Oh at least one more; someone with a great deal of experience and skill in the art of frugality could likely squeeze in several more shots. 
"A risk-free world is a very dull world, one from which we are apt to learn little of consequence." -Geerat Vermeij
|
|
Hennig Brand
International Hazard
   
Posts: 1284
Registered: 7-6-2009
Member Is Offline
Mood: No Mood
|
|
Tetrolite Friction Sensitivity Testing
A crude friction test was performed on ETN, melt/cast ETN, co-precipitated Tetrolite and melt/cast Tetrolite. A set of bathroom scales was used to
measure downward force applied. A marble pestle, from a pestle and mortar set was used. A piece of carbon steel with surface rust was used, which was
extremely abrasive. Downward force was kept between 40-45lbs as the pestle was drug over the sample (ca. <5mg sample weight). The pestle was rubbed
across each sample six times or until ignition. The only sample that was initiated by this treatment was the melt/cast ETN, which produced a loud
snap.
1. Powder ETN....................................No ignition
2. Melt/cast ETN..................................Ignition
3. Co-precipitated Tetrolite (granular)....No Ignition
4. Melt/cast Tetrolite............................No Ignition
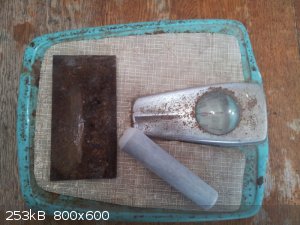
Note:
I suppose the rust could be seen as a contaminant and could have altered the sensitivity of the sample it mixed with. It was of course a crude test
and if anything the rust would have likely increased sensitivity not decreased it.
[Edited on 8-12-2014 by Hennig Brand]
"A risk-free world is a very dull world, one from which we are apt to learn little of consequence." -Geerat Vermeij
|
|
Laboratory of Liptakov
International Hazard
   
Posts: 1405
Registered: 2-9-2014
Location: Technion Haifa
Member Is Offline
Mood: old jew
|
|
[Edited on 8-12-2014 by Laboratory of Liptakov]
|
|
Laboratory of Liptakov
International Hazard
   
Posts: 1405
Registered: 2-9-2014
Location: Technion Haifa
Member Is Offline
Mood: old jew
|
|
Holes
This is a pretty good method. Test friction. And the results are good. Sensitivity is low.
I also have results ........ Also, saving material....LL
|
|
Hennig Brand
International Hazard
   
Posts: 1284
Registered: 7-6-2009
Member Is Offline
Mood: No Mood
|
|
Nice collection! I would have quite a pile too, at this point, if I went around and gathered everything up.
I was thinking of performing an impact sensitivity test on molten Tetrolite. I could easily heat a small anvil up with a propane torch to above the
melting point of Tetrolite. I have a small 11lb anvil that would likely work well.
TNT Acidity
It was brought into question a while ago whether or not the acidity of TNT would be a stability problem for mixtures of it and ETN. I still don't have
a definitive answer, but I understand better now what I am dealing with. ETN is much less storage stable than PETN and this instability gets worse in
the presence of acidity. Gladly, it turns out that TNT has extremely low acidity. Also, TNT and ETN are non hygroscopic and have very low solubility
in water. The attached jpg image below was made from the first few paragraphs of page 300 from Urbanski Volume 1.
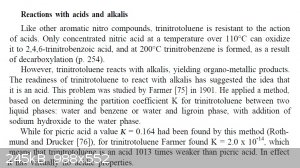
[Edited on 8-12-2014 by Hennig Brand]
"A risk-free world is a very dull world, one from which we are apt to learn little of consequence." -Geerat Vermeij
|
|
PHILOU Zrealone
International Hazard
   
Posts: 2893
Registered: 20-5-2002
Location: Brussel
Member Is Offline
Mood: Bis-diazo-dinitro-hydroquinonic
|
|
Acidity of TNT only express in strong alcaline media (NaOH for example)...the resulting compound is coloured red and this is a proof of an
aci-nitronic/nitronate form. The resulting form is also more sensitive to shock (impact sensitivity).
The rest of the aromatic ring has been left aside because it doesn't enter the reaction
CH3-C=C-NO2 <==--> CH2=C-C=N(O)-OH
CH2=C-C=N(O)-OH =NaOH=> CH2=C-C=N(O)-ONa + H2O
So there is no acidity concern to fear about TNT in admixture with ETN...as long as both ingredients are wel acid-free washed
and recristallized.
[Edited on 10-12-2014 by PHILOU Zrealone]
PH Z (PHILOU Zrealone)
"Physic is all what never works; Chemistry is all what stinks and explodes!"-"Life that deadly disease, sexually transmitted."(W.Allen)
|
|
Hennig Brand
International Hazard
   
Posts: 1284
Registered: 7-6-2009
Member Is Offline
Mood: No Mood
|
|
Thanks for the great description.
There really are a lot of things that can be done with TNT that can't be done with picric acid. For instance, because it has virtually no acidic
properties, a relatively low melting point and great compatibility with most other explosives, among other desirable qualities, TNT can form many
useful mixtures with other explosives. Picric acid has its place too though; it is much easier to make and many other useful explosives can be made
from it. Picric acid seems a bit easier to use as a base charge as well. Both of these cousins have a lot going for them.
[Edited on 11-12-2014 by Hennig Brand]
"A risk-free world is a very dull world, one from which we are apt to learn little of consequence." -Geerat Vermeij
|
|
Hennig Brand
International Hazard
   
Posts: 1284
Registered: 7-6-2009
Member Is Offline
Mood: No Mood
|
|
Cast 50/50 Tetrolite Base Charge Explosive Testing in 7.6mm id Aluminum Casing
I found some more witness plates, so this is the last time I will show this over exploited old one.
A while ago now I tested some cast 50/50 Tetrolite. A stainless steel pot with ca. 60-70C water was used to melt the 50/50 tetrolite. The aluminum cap
casing was taped to the side of the pot so that it would also be above the melt point, which prevented premature solidification and also provided a
larger thermal mass allowing for slower cooling of the casting. The tetrolite was melted in a small polypropylene plastic container partially
submerged in the hot water.
Three cast 50/50 tetrolite explosive tests have been performed all with similar results. The first test involved 1g cast tetrolite with 0.2g of lead
azide pressed on top. The second test involved 1g of cast tetrolite and 0.3g of LA pressed on top. The third test involved 0.75g of cast tetrolite,
0.25g of granular tetrolite pressed on top and 0.3g of LA pressed on top of that. A little basic lead picric was used as flash igniter in all tests.
None of the tests showed the plate penetration that the pressed granular material displayed. The cast material did however make by far the biggest
dents in the witness plate that I have seen so far. I assume at this point that cast 50/50 tetrolite has a lower detonation velocity at the 7.6mm
charge diameter than does pressed tetrolite. I will need to test the cast tetrolite at a larger diameter to see if that shows an improvement (I
suspect it will).
Attached are a few pictures from one of the tests. The hole/dent and scab on the right, in the witness plate top and bottom views, are from this test.
Last time using this witness plate I promise. 
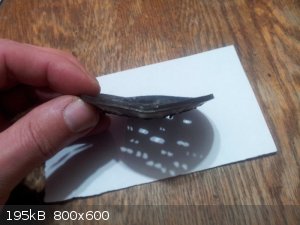
[Edited on 20-12-2014 by Hennig Brand]
"A risk-free world is a very dull world, one from which we are apt to learn little of consequence." -Geerat Vermeij
|
|
Hennig Brand
International Hazard
   
Posts: 1284
Registered: 7-6-2009
Member Is Offline
Mood: No Mood
|
|
Tetrolite Impact Testing
I built an impact testing machine in the last few days. I spent a bit of time in the past watching a large electromagnet being used to move scrap
metal around at a scrap yard and noticed that when the electromagnet was de-energized the steel fell basically instantaneously and straight down. I
though it would make a great quick release mechanism for a fall hammer. The fall hammer quick release could be controlled from as far away as desired
by running a thin copper pair with a switch at the end. An electromagnet was made from an old 16V, 1A, "wall wart" type DC power supply transformer.
The core was cut off at one end with a hack saw and the 16V secondary winding was removed. The top of the hammer head was too small and rounded so a
steel plate was welded onto one end for the magnet to attached to. It was found that 5V DC, across the 120V primary winding, was more than enough to
hold up the 2.85kg hammer, but 9V DC was used instead which could hold the weight of at least several times the weight of the hammer. A wooden slide
was made, for height adjustment, which could be fixed in place by tightening a wing nut. A plumb line was made from a bit of nylon cord and a steel
nut was used as the plumb bob which allowed me to determine exactly where the fall hammer would land and position the anvil and punch assembly
accordingly. Simply because of availability, 13/16 inch soft steel round stock was used to make the anvil and punch (roller bearing would have been
preferable and possibly in smaller diameter). A wooden holder was made for the anvil and punch with two large vent holes for explosive gases and flash
to escape from. The bottom end of the 13/16 inch anvil sits on the large blacksmith's anvil below.
This test was a quick and dirty test in a number of ways. It was in large part an excuse to test the apparatus. The ETN used for the ETN test was of
unknown purity and not freshly made; it was removed from a section of detcord which was made over 3 years ago and was a very fine powder. From earlier
testing of the machine, I knew about were the starting height should be for this sample of ETN. The sensitivity of the ETN tested seemed
uncharacteristically low. The test will be repeated when a freshly made, recrystallized, sample of ETN is available. Also, as has been discussed
before, wrapping the sample in aluminum foil does effect the results, at least to a small extent, as it is soft and will absorb some of the force of
the blow. The height was increased by 2 inches after each no go test.
Results (2.85kg Fall Hammer and 13/16 Inch Punch and Anvil):
ETN Powder
22 inches - no go
24 inches - loud bang
Tetrolite 50/50 Co-precipitated/Granular
24 inches - no go
26 inches - loud bang
Tetrolite 50/50 Cast
26 inches - no bang but smell
28 inches - no bang but smell
30 inches - small snap, a lot of smoke and smell
Here are a few pictures of the apparatus:
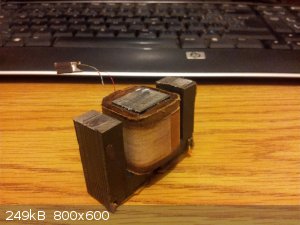
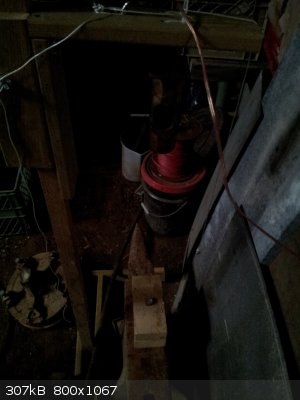
[Edited on 20-12-2014 by Hennig Brand]
"A risk-free world is a very dull world, one from which we are apt to learn little of consequence." -Geerat Vermeij
|
|
Bert
Super Administrator
       
Posts: 2821
Registered: 12-3-2004
Member Is Offline
Mood: " I think we are all going to die. I think that love is an illusion. We are flawed, my darling".
|
|
I continue to be impressed with your testing program.
I spoke about drop tests some time back with a manufacturer of industrial testing & quality control equipment. They did indeed use an
electromagnetic drop mechanism. The rig also automatically reset, logged heights of tests, all the tech did was set a new anvil plate & sample in
place-
It was HIDEOUSLY expensive, came with a nice software suite though.
Rapopart’s Rules for critical commentary:
1. Attempt to re-express your target’s position so clearly, vividly and fairly that your target says: “Thanks, I wish I’d thought of putting it
that way.”
2. List any points of agreement (especially if they are not matters of general or widespread agreement).
3. Mention anything you have learned from your target.
4. Only then are you permitted to say so much as a word of rebuttal or criticism.
Anatol Rapoport was a Russian-born American mathematical psychologist (1911-2007).
|
|
Hennig Brand
International Hazard
   
Posts: 1284
Registered: 7-6-2009
Member Is Offline
Mood: No Mood
|
|
Thanks, good to know I was on the right track with the electromagnet as well. Much better electromagnets can be made or bought. I watched a professor
pick up a ca. 120lb girl off the floor, who was holding a handle or sitting in a harness attached to a steel plate, using a small round electromagnet
(ca. 2-3 inches in diameter) powered by one, 1.5V, D sized battery in a first year electrical engineering class. The magnet he used was rated for up
to 500lbs, IIRC, and was obtained mail order from a scientific supply company. I think they went for about $100 the last time I checked. The professor
told me the same D battery had been used for about 5 years to do the class demonstrations. Those designs are much more highly optimized than the one I
made from an old transformer, but the one I made does the trick (at least for this application). Making a highly optimized and powerful electromagnet
has been on my to do list for a while.
[Edited on 20-12-2014 by Hennig Brand]
"A risk-free world is a very dull world, one from which we are apt to learn little of consequence." -Geerat Vermeij
|
|
Laboratory of Liptakov
International Hazard
   
Posts: 1405
Registered: 2-9-2014
Location: Technion Haifa
Member Is Offline
Mood: old jew
|
|
hammer
I have this idea. Why use a plumb line? Motion in the picture. Replaceable paper tube. Small window for precise adjustment and control before the
test. The paper tube is a plug-in. Not too much force. Not too freely. In short, just right. I suggest pipe inner diameter of about 15 mm. If it
blows, the paper will be destroyed. But if not, it can be used again. On the right in the picture is a simple version without solenoid. Plastic pipe
with a diameter of about 50 mm or 2 inches.... ....LL
|
|
Hennig Brand
International Hazard
   
Posts: 1284
Registered: 7-6-2009
Member Is Offline
Mood: No Mood
|
|
The plumb line is only used to position the anvil under the hammer then it is put up out of the way during the test. So in your design the anvil,
punch and hammer all fall onto the main anvil below? All of the commercial designs that I have seen have a track or guide of some sort on either side
of the hammer, which has advantages. For starters, it guides the hammer to the target and the hammer doesn't need to be picked up off the ground
either. The free fall design has some advantages too, however, it is simpler and cheaper to build, one can be sure that there is no resistance to
motion other than wind resistance during the fall as well. I think your plastic tube idea could probably work, not sure about the release mechanism
though. I wanted a true falling hammer and I wanted it simple and I suspected that if I got into shoots and tracks and things that I could easily get
into problems with friction unless I went complicated or expensive (tracks). The solution to not having to aim the hammer every time is to build a
better stand for the apparatus. The stand could have been made with two vertical members, like in Markx's design and most commercial models, which
were carefully made as close to perfectly vertical as possible and well fixed in that position. With this setup, no matter what height the hammer was
put at it would always hit more or less the same place every time (gravity is a wonderful thing; very reliable). Even one vertical member could be
used but it would need to be made to more exacting standards than I made mine. This is only a prototype model. 
Laser Plumb Line
Ok, I just thought of a nice solution to the hassle of the plumb line. The plumb line I am using now must have its length adjusted nearly every time
the hammer height is adjusted and being so long it can be a bit unwieldy to work with and a bit of a bother to make steady. I have been thinking of
how to use a laser level or laser pointer in some way that would be more convenient but still be as reliable. I kept discarding ideas because most of
them seemed less reliable and less accurate compared to a plumb line. A laser plumb line though incorporates the good points of both the laser and the
plumb line and loses most of the negative attributes of the regular plumb line. It can be made much shorter and never needs to be adjusted for height,
since the laser beam can travel the distance and mark the landing spot. Since the plumb line is shorter, it is easier to steady and also easier to put
up out of the way during tests. I found the attached picture of one online.
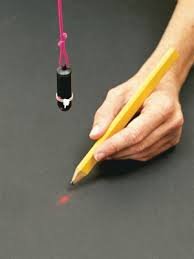
[Edited on 21-12-2014 by Hennig Brand]
"A risk-free world is a very dull world, one from which we are apt to learn little of consequence." -Geerat Vermeij
|
|
Laboratory of Liptakov
International Hazard
   
Posts: 1405
Registered: 2-9-2014
Location: Technion Haifa
Member Is Offline
Mood: old jew
|
|
nice work
OK results are important and these are at the top. Tetrolite granules cast and are less sensitive than ETN. That's the main thing. All three samples
have low sensitivity. That's good, nice work .... ...LL
|
|
Hennig Brand
International Hazard
   
Posts: 1284
Registered: 7-6-2009
Member Is Offline
Mood: No Mood
|
|
Thanks, I expect that the sample of ETN powder I tested was less pure and more insensitive than it should be however. You are right though, tetrolite
both granular co-precipitated and cast is definitely at least a little less sensitive to impact than ETN which is an important thing to know.
"A risk-free world is a very dull world, one from which we are apt to learn little of consequence." -Geerat Vermeij
|
|
markx
National Hazard
  
Posts: 646
Registered: 7-8-2003
Location: Northern kingdom
Member Is Offline
Mood: Very Jolly
|
|
Excellent work, Hennig!
The ETN sensitivity really seems very low, a characteristic result for a fresh recristallised and purified sample would lie on the order of 30-40cm
drop height which translates into about 10-15 inch. At least it does so on my particular drop test machine. Then again the results of drop test may
vary quite significantly between different machines depending on construction, materials, placement and substrates. Hence it is hard to compare the
values from different testers, but comparing the relative differences of samples tested on one and the same apparatus should give a better
perspective.
Perhaps you could also incorporate a mechanical failsafe for the electromagnet in case the power circuit should fail or become damaged for some
reason. Electromagnets are strong, but the only thing keeping the hammer from falling is the electrical current...one bad solder joint or damaged
switch and a premature drop is the result. There is no real danger of a serious injury if the sample weigths are kept normal, but the effect of
thescare that the noise from a 3kg hammer hitting an anvil accompanied by the possible detonation of the sample can give you is quite enough for me to
incorporate some preemptive measures into the system.
Also building a basket around the anvil to catch the falling hammer after if has hit the target is really convenient....and prevents the thing from
landing on your toes after every test 
Perhaps something like the one I did here:
http://www.sciencemadness.org/talk/viewthread.php?tid=32296&...
Exact science is a figment of imagination.......
|
|
Hennig Brand
International Hazard
   
Posts: 1284
Registered: 7-6-2009
Member Is Offline
Mood: No Mood
|
|
Thank you. Yeah, that ETN is very likely much too insensitive. The ETN used to make the tetrolite was from a much more recently made batch. I built
the apparatus in a bit of a hurry as well, so I should go back and carefully check that the anvil and punch surfaces are really flat and smooth and
actually flush with each other. The aluminum foil probably shouldn't be used either, but I would need to test to see how much of a difference going
without it would make. A basket to catch the fall hammer would be convenient for sure. I have a procedure which I think is fairly safe though. The
sample is placed on the anvil and lined up under the hammer release. The hammer is put in place last and then a bit of downward force is placed on the
hammer by hand to be sure that it is really secure. The position of the anvil is verified with the plumb line before the line is moved out of the way
for the test. Currently about 15 feet of speaker wire (copper pair) is used which allows me to be well away from the apparatus, and behind cover if
desired, when the current flow is removed from the magnet.
Battery Backup Failsafe
Some of the old backup lighting systems, security system and things had a very simple battery backup system, so I was told by a technician years ago,
that used a single diode. I have used the following concept several times in the past. If the AC power, or power supply, fails for whatever reason
current will immediately start flowing through the diode from the battery when the voltage on the cathode side of the diode drops below that of the
battery by about 0.6V (for a silicon diode). This is a very simple circuit compared to many modern battery backup systems, without some of the
advantages, but it is very reliable, simple and cheap. I made a little sketch with paint to illustrate the concept. Of course a mechanical failsafe
could also be used, with or without the battery backup.
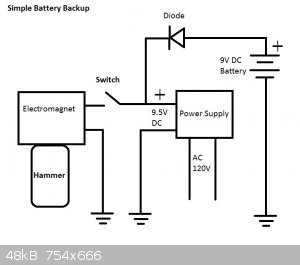
[Edited on 22-12-2014 by Hennig Brand]
"A risk-free world is a very dull world, one from which we are apt to learn little of consequence." -Geerat Vermeij
|
|
Hennig Brand
International Hazard
   
Posts: 1284
Registered: 7-6-2009
Member Is Offline
Mood: No Mood
|
|
It just occurred to me that what I need are adjustable feet for the fall hammer apparatus. The vertical member could maybe have been positioned closer
to perpendicular the base, during assembly, but the truth is almost no floor or ground is perfectly level anyway. A way to quickly make adjustments to
make the apparatus level would be a good addition. This would reduce the need to make adjustments of anvil position below the fall hammer whenever the
height was adjusted.
[Edited on 24-12-2014 by Hennig Brand]
"A risk-free world is a very dull world, one from which we are apt to learn little of consequence." -Geerat Vermeij
|
|
Hennig Brand
International Hazard
   
Posts: 1284
Registered: 7-6-2009
Member Is Offline
Mood: No Mood
|
|
Here is an alternative to an electromagnet for the drop hammer device. It is a permanent magnet inside a light casing for picking up iron, steel and
other magnetic objects. A spring is inside which holds the magnet against the thin non-magnetic bottom plate. When the handle, which is attached to
the magnet by a rod, is pulled the magnet comes away from the plate which releases any objects magnetically coupled. If a suitable commercial model
could not be found, to hold up the fall hammer used, one of these could be built or the magnet in a commercial model could be replaced with a more
power magnet. Before I built the electromagnet I was playing around with a car speaker magnet. These speaker magnets are often extremely strong and
have no problem holding up a hammer head of several kilograms. Some sort of lever or pulley arangment, above the permanent magnet assembly, could be
used to change the direction of force and possibly provide mechanical advantage allowing the hammer to be released from a safe distance by pulling a
thin cord.
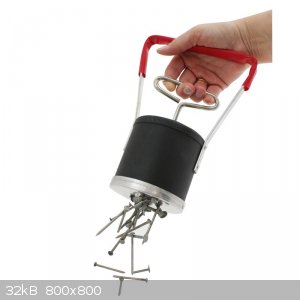
[Edited on 31-12-2014 by Hennig Brand]
"A risk-free world is a very dull world, one from which we are apt to learn little of consequence." -Geerat Vermeij
|
|
Hennig Brand
International Hazard
   
Posts: 1284
Registered: 7-6-2009
Member Is Offline
Mood: No Mood
|
|
Quote: Originally posted by Hennig Brand  |
Results (2.85kg Fall Hammer and 13/16 Inch Punch and Anvil):
ETN Powder
22 inches - no go
24 inches - loud bang
Tetrolite 50/50 Co-precipitated/Granular
24 inches - no go
26 inches - loud bang
Tetrolite 50/50 Cast
26 inches - no bang but smell
28 inches - no bang but smell
30 inches - small snap, a lot of smoke and smell
|
A freshly made and recrystallized from methanol sample of ETN was just tested three times and the average fall height which resulted in initiation was
15 inches using exactly the same testing method and apparatus as was used for the earlier testing. The temperature in the building where the testing
was done, this time and last, was below zero Celsius which could have at least partially resulted in lower values for sensitivity. Since the tetrolite
was made with ETN that was only a month or two old and was recrystallized and well stored, it is safe to say with a high degree of certainty that
tetrolite, either co-precipitated or cast, is significantly less sensitive to impact than straight crystalline ETN.
"A risk-free world is a very dull world, one from which we are apt to learn little of consequence." -Geerat Vermeij
|
|
Laboratory of Liptakov
International Hazard
   
Posts: 1405
Registered: 2-9-2014
Location: Technion Haifa
Member Is Offline
Mood: old jew
|
|
etn
This is an interesting change, but it's still pretty good sensitivity. Clean fresh ETN, hammer almost 3 kg, height 38 cm, it is still good ... ...LL
|
|
Dornier 335A
Hazard to Others
 
Posts: 231
Registered: 10-5-2013
Location: Northern Europe
Member Is Offline
Mood: No Mood
|
|
I got an idea about another melt-castable based on TNT. It could maybe be called "hexolite", but not from mannitol hexanitrate. The much more potent
and denser oxidizer hexanitroethane should give a slightly better bang. 63.4% HNE and 36.6% TNT is oxygen balanced and should be possible to cast
safely, at least with some care. A similar but non-cast mixture with HNE and tetryl was tested in an old thread found here
The downside would be that the mixture can prove to be quite sensitive. Pure HNE is like PETN, but a mixture with a fuel will likely be more
sensitive; that's at least the case with TNM-based mixtures.
Calculated performance at 1.77 g/cc:
DCJ: 9000 m/s
PCJ: 363 kbar
Energy content: 7.21 MJ/kg (about 30% higher than HMX)
|
|
markx
National Hazard
  
Posts: 646
Registered: 7-8-2003
Location: Northern kingdom
Member Is Offline
Mood: Very Jolly
|
|
Perhaps coprecipitation from a common solvent or solvent system could also yield interesting results with some combination of energetics....and likely
be a safer practice compared to melt casting. I do not particularily like the idea of melting together highly potent substances...
Exact science is a figment of imagination.......
|
|
Hennig Brand
International Hazard
   
Posts: 1284
Registered: 7-6-2009
Member Is Offline
Mood: No Mood
|
|
Hard to ignore the great ease with which very well incorporated mixtures can be cast at high density and with great uniformity however. The advantages
for shaped charge applications, for instance, are tremendous. Pentolite is a very common melt/cast mixture that is used both militarily and
commercially and all reports I have seen would indicate that it is fairly safe to work with. Tetrolite (ETN-TNT) can be melted below 50C using hot
water much below the boiling point. As long as open flames, or other intense localized heat sources, aren't used the melt/cast process should be
fairly safe in my opinion. I have several samples of tetrolite which have been sitting around for a month or so, both co-precipitated and melt/cast,
and so far there appears to be no signs of decomposition. The melt/cast samples have been re-melted and cast several times too. I do proceed with
caution though when working with such things.
"A risk-free world is a very dull world, one from which we are apt to learn little of consequence." -Geerat Vermeij
|
|
Pages:
1
2 |