Pages:
1
..
6
7
8
9
10
..
13 |
al93535
Harmless
Posts: 13
Registered: 22-5-2004
Member Is Offline
Mood: good
|
|
I'm looking for some information on melt casting TNT with PETN to make pentolite. What I would like are pointers on which available books I can find
this information. Or if anyone here knows the correct safe procedure.
Thank you!
|
|
magneet
Harmless
Posts: 19
Registered: 30-12-2007
Location: on a forum somewhere
Member Is Offline
Mood: lurking mostly
|
|
Here's something:
http://www.google.com/patents?id=sGVgAAAAEBAJ&printsec=abstract&zoom=4#v=onepage&q&f=false
Ive made it a time ago, be sure of a good ignition.
Hi,
|
|
al93535
Harmless
Posts: 13
Registered: 22-5-2004
Member Is Offline
Mood: good
|
|
While that exact link wasnt what i was looking for, you reminded me about searching patents!!! Thank you! Doing lots of reading! I'll post what i
find for others.
Ok, here is what I plan to do:
Prepared petn which will be sized to -60+100 mesh, will be added to distilled water in a ratio of 400:1500 petn:water at 36 degrees F. Then TNT will
be dissolved in acetone Nd brought up to 90 degrees F, ratio 400:600.
While the petn is vigorously being stirred the TNT/acetone will be added slowly. Thus causing the TNT to coat the petn when it comes out of solution.
Filter and dry.
Melt the clongolmorate Granules in a beaker in a hot water bath at 85-90 degrees C. Pour cast into suitable mould with a funnel providing extra for
the 10% shrinkage during cooling.
How's that sound
[Edited on 13-7-2012 by al93535]
|
|
Hennig Brand
International Hazard
   
Posts: 1284
Registered: 7-6-2009
Member Is Offline
Mood: No Mood
|
|
Last year I experimented with nitrating toluene. I used ammonium nitrate and draincleaner sulfuric acid. The sulfuric acid titrated as about 91%
concentrated. I used a three stage method, using ammonium nitrate, given by Bonome earlier in this thread. I was pretty sure that the acid wasn't
strong enough for the final stage, going from DNT to TNT, but I gave it a try anyway. Bonome indicated that he was using sulfuric acid of 94%
concentration, and IIRC I didn't make adjustments in my experiment for the lower concentrated 91% acid used.
I have recently been experimenting with melting point determinations in order to determine the purity of Picric Acid samples. I thought I would give
it a try with the sample of TNT saved from last year.
The thermal mass in the picture is an aluminum block weighing 304g. There is a 1cm deep recess in the top of the block for the thermocouple probe, as
well as a 1cm deep recess for the sample to be tested. A glass slide could be placed over the sample recess, to obtain a small increase in melting
point accuracy. A propane torch is used to focus a small flame into the notch at the base of the aluminum block. A small block of dry cedar was placed
below the aluminum block, to insulate the block and prevent heat loss. It is reasonable easy to accurately control the temperature of the sample with
this setup. The big thing seems to be having a suitably large thermal mass.
The melting point obtained was 64C. According to the table taken from "TNT Trinitrotoluenes And Mono And Dinitrotoluenes Their Manufacture And
Properties" by G. Carlton Smith, this melting point corresponds to either ~13% TNT or ~ 76% TNT. Given the color of the sample I think that it is
probably the later, 76% TNT. The text is available for download from the forum library. I have included a jpg of the table from the text and a couple
of pictures of the melting point apparatus used.
The TNT is definitely far from pure. However it can be nitrated further or be used to make a very nice cheddite explosive.
BTW, regarding pentolite, apparently TNT samples with quite a lot of DNT in them can still make very respectable pentolite (I have references if I can
find them). The other advantage is that a little DNT greatly reduces the melting point, facilitating pentolite manufacture.
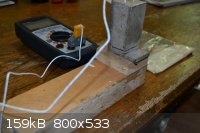
[Edited on 19-7-2012 by Hennig Brand]
"A risk-free world is a very dull world, one from which we are apt to learn little of consequence." -Geerat Vermeij
|
|
Hennig Brand
International Hazard
   
Posts: 1284
Registered: 7-6-2009
Member Is Offline
Mood: No Mood
|
|
I did do a sulfite wash. I also remember that I had to rinse an awful lot in order to get all of the red out afterwards.
My brother was renovating a rental unit a few years ago and he came across this large bottle of chemical on the basement floor beside some paint cans,
etc. He knew I was into experimenting so he gave it to me instead of throwing it out. IIRC, the previous tenant was into photography. I think there is
still around 4 lbs or so of sodium sulfite left in the bottle.
"A risk-free world is a very dull world, one from which we are apt to learn little of consequence." -Geerat Vermeij
|
|
al93535
Harmless
Posts: 13
Registered: 22-5-2004
Member Is Offline
Mood: good
|
|
Thank you hennig!! I needed that melting point table! I could not find the forum library, however I was able to find the book a great help! thanks!!
[Edited on 23-7-2012 by al93535]
[Edited on 23-7-2012 by al93535]
|
|
Hennig Brand
International Hazard
   
Posts: 1284
Registered: 7-6-2009
Member Is Offline
Mood: No Mood
|
|
No problem. For the forum library use the following link.
http://www.sciencemadness.org
Look at the address bar at the top of your screen. Deleting everything in the URL after the domain name, and hitting enter, will bring you to a page
with links to the forum, the library and other resources.
[Edited on 24-7-2012 by Hennig Brand]
"A risk-free world is a very dull world, one from which we are apt to learn little of consequence." -Geerat Vermeij
|
|
Trotsky
Hazard to Others
 
Posts: 166
Registered: 6-2-2013
Location: US
Member Is Offline
Mood: No Mood
|
|
Sorry to revive an old thread, but better than starting a new one. I was wondering if someone could tell me the following:
1) what is the real risk of a runaway with TNT? Is it similar to NC or more like ETN (which I've had runaway reactions the two times I've
(attempted) to make it. I know the second and third nitrations require heating too more than 100C. Is the risk only in the first nitration?
2) I've seen people talk about using nitrate salts in making TNT. Is that really effective? I would think it would need to be more pure, at least
for the third nitration. With huge excess does it work? I've seen people suggest using 3x the stochiometric ratio to ensure complete nitration to go
straight to DNT.
How does DNT compare to TNT as an explosive? I'm sure I made some during experiments nitrating gasoline and kerosene, but that was a globby waxy
mess* and not useful for drawing conclusions from.
*(which made for a very energetic fuel when burned, but awesome rocket fuel when mixed with KNO3- it burned like an energetic in open air but there
wasn't enough NO3 groups on whatever it was to really burn well in confinement it seems).
|
|
Ral123
National Hazard
  
Posts: 735
Registered: 31-12-2011
Member Is Offline
Mood: No Mood
|
|
I tried to make MNT with 60% nitric. It required fast stirring. Anyway I ended up with a runaway, a fire and short circuit in the room. Btw a friend
made and detonated successfully cast TNT with 5% Al with only some AP. He used AN/H2SO4. I mixed mine with 40% ETN end couldn't set if off with
azide-ETN-ETN/EGDN :/
|
|
Hennig Brand
International Hazard
   
Posts: 1284
Registered: 7-6-2009
Member Is Offline
Mood: No Mood
|
|
Just above in this thread: http://www.sciencemadness.org/talk/viewthread.php?tid=29&... I was unsure if what I had made was 13% TNT or 76% TNT. After nitrating some of
the same material further I can say that it was actually about 13% TNT. There were some very interesting colors during the nitration and washing
stages. About 95% yellow nitric acid and 95% sulfuric acid was used for the final nitration.
About 14 grams of the 13% TNT - 87% DNT mixture was used for the nitration. About 10mL of ca. 95% yellow nitric acid and 18mL of ca. 95% sulfuric acid
was used to form the mixed acid. The nitrotoluene mixture was dissolved in the sulfuric acid with warming followed by nitric acid addition at 50-60C
and then the temperature was brought up, and held, between 100C and 115C for 2 hours.
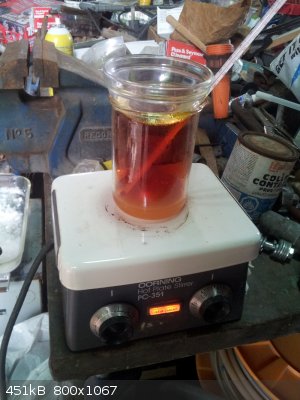
This light green colored syrup was what I got after letting the nitration mixture cool and then transferring the nitrated toluene into a beaker with
water.
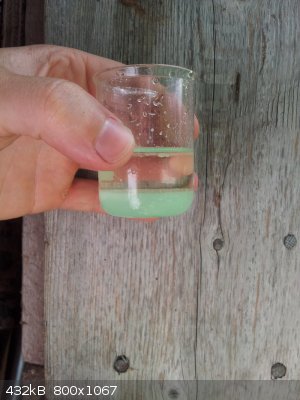
[Edited on 30-6-2014 by Hennig Brand]
"A risk-free world is a very dull world, one from which we are apt to learn little of consequence." -Geerat Vermeij
|
|
Hennig Brand
International Hazard
   
Posts: 1284
Registered: 7-6-2009
Member Is Offline
Mood: No Mood
|
|
The product did eventually solidify after it was washed with water, and cooled more, and changed in color to a white color with a tiny hint of yellow.
The product was then melted and washed under hot water with magnetic stirring. After 20-30 minutes of washing in 90-100C water the product came out
with a pinkish color. A hot (90-100C) sulfite wash was next performed using about a 5% sodium sulfite solution. A lot of rinsing was needed after the
sulfite wash to remove the red impurities. The final product was a brown color and had a melting point which would indicate that it was about 85% TNT.
According to several sources, including Wiki, lower grade (grade B) TNT is brown colored because of the presence of impurities and has a significantly
lower melting point than more pure grade A TNT..
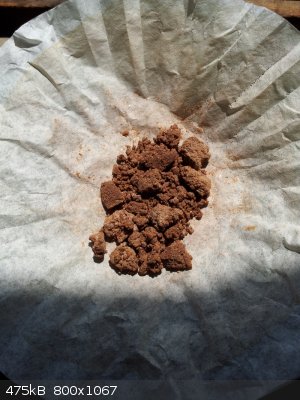
I somewhat arbitrarily chose the quantities of acids to use for the nitration. If I had used the quantities from the journal article posted by Axt
earlier in this thread I may have had better results or at least a higher degree of nitration. http://www.sciencemadness.org/talk/viewthread.php?tid=29&...
The toluene I was nitrating has been through a lot though; many hours exposed to nitration mixtures at elevated temperature, with substandard
nitration mixtures in many cases, which would likely contribute to higher amounts of impurities being formed. The purity of the hardware store toluene
is also an unknown.
[Edited on 30-6-2014 by Hennig Brand]
"A risk-free world is a very dull world, one from which we are apt to learn little of consequence." -Geerat Vermeij
|
|
nitro-genes
International Hazard
   
Posts: 1048
Registered: 5-4-2005
Member Is Offline
|
|
Familiar photos, reminds of the 3 phase synthesis of TNT I did once, also noticed that the DNT produced during the 2nd nitration had a ssemingly
higher melting point than the product obtained after further nitration to TNT using destilled 95% WFNA + 98% SA. Some eutectic is most likely formed
with DNT or maybe the nitric acid itself. Didn't had sulfite at that time, took me 20 washings or so with demineralized water to raise the melting
point to close that of TNT. The product I obtained back then was slightly yellowish not the brown colour in your last picture, any idea what the
impurities are? Seen the nearly identical synthesis used it appears the sulfite treatment to remove isomers may actually be (partly) responsible for
the brown colour?
[Edited on 30-6-2014 by nitro-genes]
|
|
Hennig Brand
International Hazard
   
Posts: 1284
Registered: 7-6-2009
Member Is Offline
Mood: No Mood
|
|
The following was basically taken right from COPAE, though the words may have gotten changed around a bit.
From COPAE, sodium sulfite reacts with and allows easy removal of Beta-TNT (2,3,4-trinitrotoluene) and Gamma-TNT (2,4,5-trinitrotoluene) to form red
colored materials which are readily soluble in water. The sulfite leaves the Alpha-TNT (2,4,6 -trinitrotoluene) and any TNB, TNX and
2,4-dinitrotoluene unaffected. Concentrated sulfuric acid apparently removes dinitrotoluene most readily of the solvents listed in COPAE as the ones
most commonly used, which include alcohol, solvent naphtha (mixed xylenes), carbon tetrachloride, and concentrated sulfuric acid. The organic solvents
remove Beta and Gamma TNT better, but all of these solvents also remove some of the Alpha TNT as well as the impurities. The material dissolved by the
sulfuric acid can be recovered by dilution with water. The organic solvents are recovered by distillation, dark brown liquids are left as residue
known as TNT oil and are used in the manufacture of non-freezing dynamite. According to COPAE the best process of purification is to agitate the crude
TNT with a warm solution of sodium sulfite.
TNT seems like a lot of extra trouble for a material that is only an improvement over picric acid as a main charge if filling artillery shells or
something similar was the objective. I think Pentolite boosters would be nice though and apparently very easy to make. Warm liquid TNT apparently
dissolves PETN quite readily and TNT with a fair bit of DNT in it still makes decent Pentolite.
There is a lot I don't know about TNT. It seems like there are quite a few strange things that can form for various reasons when making TNT and that
last nitro group can be a real pain to add unless you have the right strength and quantity of acids as well as having the temperature and reaction
time dialed in properly. I don't think making TNT is all that complicated, but it is not really well suited to the hobbyist the way that picric acid
is for a variety of reasons. It is much harder to effect the trinitration with TNT and with the materials (acid strength) normally available to the
home chemist it is not nearly as economical to do so either. Picric acid can be done in a one pot synthesis, in high yield and purity and without the
strongest acids. Many other useful materials can be made from picric acid. Picric acid is slightly more powerful than TNT as well. TNT is still
interesting to learn about and one of the nicest aspects of experimenting with it is that there is so much good reading material available because it
was such a widely used explosive.
[Edited on 1-7-2014 by Hennig Brand]
"A risk-free world is a very dull world, one from which we are apt to learn little of consequence." -Geerat Vermeij
|
|
PHILOU Zrealone
International Hazard
   
Posts: 2893
Registered: 20-5-2002
Location: Brussel
Member Is Offline
Mood: Bis-diazo-dinitro-hydroquinonic
|
|
Possible other contaminants: DNBA, TNBA, TNB!
DNT and TNT may also oxydise in boiling HNO3 with NxOy to dinitro and trinitrobenzoic acid...the later can decarboxylate to trinitrobenzene...
About the nitrated benzoic acid, a simple warm wash with concentrated NaHCO3 or Na2CO3 (or NaOH diluted) will make the soluble benzoate salt pass into
water; Acidification will crash it out. Concentrated NaOH should be avoided since it is able to deprotonate TNT and form a red colorfull soluble
nitronate salt what renders the TNT more sensitive!
CH3-C=C-NO2 + OH(-) --> CH2=C-C=N(O)-O(-) + H2O
(the aromatic ring was left aside)
Separation of TNT and TNB might be more tricky!
PH Z (PHILOU Zrealone)
"Physic is all what never works; Chemistry is all what stinks and explodes!"-"Life that deadly disease, sexually transmitted."(W.Allen)
|
|
Hennig Brand
International Hazard
   
Posts: 1284
Registered: 7-6-2009
Member Is Offline
Mood: No Mood
|
|
Thanks for the pointers. I gave the warm NaHCO3 solution wash a try and there was considerable bubbling, but the TNT is still brown. I have been
reading about TNT recrystallization from nitric acid in "Military Explosives" and "Explosives" by Meyer. Meyer suggests using 62% HNO3 and according
to both sources this recrystallization technique is very effective, but wasn't used much for other reasons for which there is some explanation in
"Military Explosives". Of course the sodium sulfite wash is supposed to be very effective too, but not as much as recrystallization from HNO3. It
looks like I oxidized the hell out of it during nitration. Oh well, it's all a learning process.
"A risk-free world is a very dull world, one from which we are apt to learn little of consequence." -Geerat Vermeij
|
|
Hennig Brand
International Hazard
   
Posts: 1284
Registered: 7-6-2009
Member Is Offline
Mood: No Mood
|
|
Quote: Originally posted by nitro-genes  | The product I obtained back then was slightly yellowish not the brown colour in your last picture, any idea what the impurities are? Seen the nearly
identical synthesis used it appears the sulfite treatment to remove isomers may actually be (partly) responsible for the brown colour?
|
I would tend to agree with you, especially after reading the following patent.
Attachment: US1975598 Purification of TNT.pdf (420kB) This file has been downloaded 704 times
"A risk-free world is a very dull world, one from which we are apt to learn little of consequence." -Geerat Vermeij
|
|
greenlight
National Hazard
  
Posts: 753
Registered: 3-11-2014
Member Is Offline
Mood: Energetic
|
|
Does anyone at all trust Jared Ledgard's 3-step Trinitrotoluene synthesis in his book a Preparatory Manual of explosives in regards to danger of
runaway or bad yields.
I tried it with 62% nitric acid because it is all i had at the time and scaled it down a lot. I used:
111.5ml 98% Sulphuric acid
92.5ml 62% Ntric acid
62.5ml toluene
And then for the dinitro step:
107.25ml 98% Sulphuric acid
70ml 62% Nitric acid plus mononitrotoluene from first step
And for the final trinitro step:
133.12ml 98% Sulphuric acid
30ml 62% Nitric acid plus dinitritoluene from last step
I obtained 75g of what i assume is pure TNT after crashing into ice-water, but is this a good yield?
|
|
NeonPulse
Hazard to Others
 
Posts: 417
Registered: 29-6-2013
Location: The other end of the internet.
Member Is Offline
Mood: Isolated from Reality! For Real this time....
|
|
I think you need strong nitric for the last step. Testing the MP of your product will giv a good indication as to what you have. I myself am looking
for a more challenging nitration and am looking at attempting the 3 step process and will be using sulfuric and nitrate salt for the mono and di
nitrations and distilled nitric for the final step but before I do ski was wondering about the smell. People have reported that the smell is pretty
strong and recommend doing this outside, which I will, but how bad does it smell? Is it really strong? If anyone who has performed these nitrations
could help that would be greatly appreciated. NP.
|
|
greenlight
National Hazard
  
Posts: 753
Registered: 3-11-2014
Member Is Offline
Mood: Energetic
|
|
When i did the 3-step nitration the smell was quite strong especially on the last steps where the temperature was very high (100degrees+). I did it
in a medium size shed and it definately did fill up the whole space inside with a sweet strong smell that i noticed when i removed my mask. It
actually smells quite nice, its just an unusual smell
It wasn't too bad outside if you are worried about neighbours smelling it but it seemed to stick to everything inside for a while afterwards.
Neonpulse, will u be using red fuming nitric or vacuum distilled white nitric and what salt, potassium nitrate?
[Edited on 8-11-2014 by greenlight]
|
|
Hennig Brand
International Hazard
   
Posts: 1284
Registered: 7-6-2009
Member Is Offline
Mood: No Mood
|
|
I found that the strongest smell in the reaction was from the mono-nitrotoluene product from the first step of the three step process (a lot of people
describe it as an almond smell). I personally have a pretty serious unpleasant physical reaction to mono-nitrotoluene, however, many people seem to
describe it as just a really strong unpleasant smell. Also, depending on the materials and process used the product of the second step can still smell
strongly of mono-nitrotoluene. The temperature gradually increases all the way up to 110-120C or so by the end of the final stage of nitration which
will of course result in greater acid vapor production (acid loss), since vapor pressure is directly proportional to temperature, which is very bad
for one’s health (if inhaled) and weakens the nitration mixture. During the final stage of nitration maintaining the strength of the mixed acid is
necessary to obtain TNT of high purity directly from nitration. The reaction flask should be fitted with a reflux condenser, especially during the
final stage of nitration.
I haven't gotten around to it, but I do plan on synthesising some TNT in the next little while. I have made equipment that will allow me to easily
make SO3 and I plan to use it to produce an anhydrous mixture of nitric and sulfuric acids for the final stage of the nitration. Like NeonPulse, I
plan on using sulfuric acid and a nitrate salt for the first two stages of the nitration, or I may combine the first two stages somehow in order to
help limit my exposure to the unpleasant mono-nitrotoluene (even if it means being more wasteful of materials). Below is a link to the posts I made
about SO3 production around the time I was working on it earlier in the summer.
http://www.sciencemadness.org/talk/viewthread.php?tid=5495&a...
"A risk-free world is a very dull world, one from which we are apt to learn little of consequence." -Geerat Vermeij
|
|
Hennig Brand
International Hazard
   
Posts: 1284
Registered: 7-6-2009
Member Is Offline
Mood: No Mood
|
|
DNT Synthesis In One Step
I spent the last few days making some TNT and taking a lot of pictures along the way. The nitration was performed in two steps; toluene was nitrated
to DNT in one step and then DNT was nitrated to TNT in a second step. I will first report on the DNT portion of the experiment, since I have a lot of
pictures for each section. I had sixty or more pictures for the DNT step alone, which I pruned down to twenty five.
Some time was spent reading through COPAE and Urbanski and the nitration mixture used was based on numbers from an old Italian method described in
Urbanski Volume 1, pg 363.
From toluene to DNT
Nitration Mixture:
HNO3....28%
H2SO4...60%
H2O......12%
In order to make a nitration mixture approximating these numbers, ammonium nitrate and 91% sulfuric acid was used. The reaction between the nitrate
and sulfuric acid was assumed to be ideal and represented by the following chemical equation.
NH4NO3 + H2SO4 ---> HNO3 + NH4HSO4
A 10% excess of HNO3 was used (though I might increase it to 20% next time around)
For 1g of toluene:
1g / 92.14g/mol = 0.01085 mols toluene
T ---> DNT takes two moles of nitric acid (ideally), used 10% excess
2 * 0.01085 * 1.1 = 0.024 moles of HNO3
therefore need 0.024 moles NH4NO3 & 0.024 moles H2SO4 to form the HNO3
mass of NH4NO3 needed = 0.024 moles * (80.052 g/mol) = 1.92g
mass of H2SO4 needed = 0.024 moles * (98.079 g/mol) = 2.35g
mass of HNO3 produced 0.024 moles * (63.01 g/mol) = 1.51g
Using the percentages from Urbanski for the nitration mixture:
mass of H2SO4 needed for nitration mixture = 1.51g / 28 *60 = 3.24g
mass of H2O specified for nitration mixture = 1.51g / 28 * 12 = 0.65g
Experimental:
For 50g of toluene used:
96g NH4NO3 (recrystallized and oven dried fertilizer grade nitrate)
(117.5 + 162g) / 0.91 = 307.1 g, 91% H2SO4 (or ca. 169mL at 1.82 g/mL)
H2O added with H2SO4 (NH4NO3 was oven dried and assumed perfectly dry):
0.09 * 307.1 g = 27.64 g
The numbers (neglecting NH4HSO4):
75.5g HNO3
162g H2SO4
27.6 H2O
Total mass = 265.1g
Percent water = 27.6g / 265.1g * 100% = 10.4% (less than the 12% specified by the Italian numbers)
Procedure:
The NH4NO3 was dissolved in the sulfuric acid the night before the nitration was to be performed. The 50g of toluene was weighed out and added to a 1L
Erlenmeyer flask which was equipped with an improvised air cooled reflux condenser. Addition of the nitration acid took about 3 hours and was done
with a 25mL burette. The temperature started out at about 30C, but was raised all the way to 80C by the end of the 3 hours and then was held at 80C
for an additional 2 hours once all the nitration acid had been added. It is clear from the pictures that as the nitration progressed the color of the
mixture darkened to a maroon color and gradually lightened again to a light yellow color. Strong magnetic stirring was used throughout.
The mason jar in the first picture holds about 1/4 of the nitration acid made from NH4NO3 and 91% H2SO4. I forgot to take a picture of it at the
start. The second picture shows the 50g of toluene in the flask just before the nitration was started.
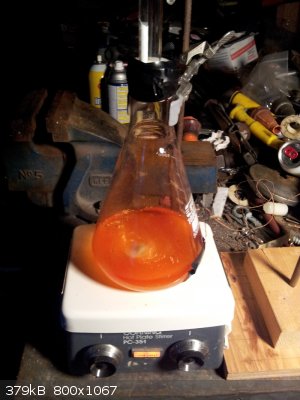
[Edited on 25-11-2014 by Hennig Brand]
[Edited on 7-12-2014 by Bert]
[Edited on 7-12-2014 by Bert]
"A risk-free world is a very dull world, one from which we are apt to learn little of consequence." -Geerat Vermeij
|
|
Hennig Brand
International Hazard
   
Posts: 1284
Registered: 7-6-2009
Member Is Offline
Mood: No Mood
|
|
Continuation of Nitration and Color Change
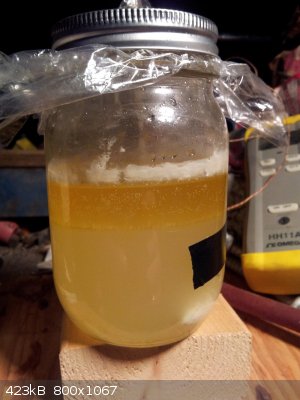
[Edited on 25-11-2014 by Hennig Brand]
"A risk-free world is a very dull world, one from which we are apt to learn little of consequence." -Geerat Vermeij
|
|
Hennig Brand
International Hazard
   
Posts: 1284
Registered: 7-6-2009
Member Is Offline
Mood: No Mood
|
|
Post Reaction Work-up
After the three hour addition time, and two hour heating at 80C, the stirring was continued but the mixture was allowed to cool. The stirring was
stopped once the temperature had dropped to about 60C and the DNT was allowed to rise to the surface and collect. Solidification did not happen until
about 50C. Once the reaction mixture had cooled to 20-30C the DNT cake was broken up with a large, stainless steel, flat head screw driver and scooped
out with a spoon. Diluting the spent acid mixture precipitated another small amount.
The collected, and water washed, DNT was put back in the flask with about 250mL of clean water and heated to above the melting point of the DNT.
Vigorous stirring was applied for 15-20 minutes to help dissolve water soluble impurities. The flask was then allowed to cool to room temperature, at
which point the water was drained off and the DNT cake was washed a couple of times with small quantities of cold water. The cake was then broken up
with a bamboo skewer and dumped from the flask. The chunks of cake were then allowed to dry and then weighed.
Yield of Crude DNT
Theoretical Yield:
50g / (92.14g/mol) * 182.134g/mol = 98.84g
Actual Yield = 100.2g (not counting an estimated 1g not retrieved as fines from wash water)
Percent Yield : 100.2g / 98.84g * 100% = 101%
The product is not pure DNT, but contains some MNT and TNT, as well as at least a small amount of other impurities. A very small amount of water would
also be included in the weight. Nevertheless, the yield is very good.
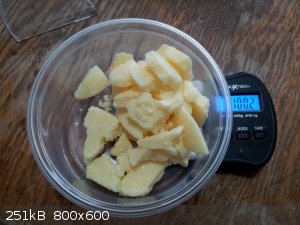
[Edited on 25-11-2014 by Hennig Brand]
"A risk-free world is a very dull world, one from which we are apt to learn little of consequence." -Geerat Vermeij
|
|
Rosco Bodine
Banned
Posts: 6370
Registered: 29-9-2004
Member Is Offline
Mood: analytical
|
|
There is a file attached to this linked post that may be useful
http://www.sciencemadness.org/talk/viewthread.php?tid=29&...
DNT and aluminum powder at about 5% and 1% IIRC make one of the best sensitizer systems ever found for NH4NO3
|
|
Hennig Brand
International Hazard
   
Posts: 1284
Registered: 7-6-2009
Member Is Offline
Mood: No Mood
|
|
Thanks for posting the great article. I have been looking it over off and on for more than a week. 
That ammonium nitrate sensitizer sounds really interesting. Do you have any reading material on it?
"A risk-free world is a very dull world, one from which we are apt to learn little of consequence." -Geerat Vermeij
|
|
Pages:
1
..
6
7
8
9
10
..
13 |