Pages:
1
2 |
Engager
Hazard to Others
 
Posts: 295
Registered: 8-1-2006
Location: Moscow, Russia
Member Is Offline
Mood: Lagrangian
|
|
Calcium cyanamide and aminoguanidine from urea and calcium oxide
Note: Preparation of aminoguanidine bicarbonate form calcium cyanamide produced by method described in this
post can be found in one of the posts below.
Preparation of calcium cyanamide from urea and calcium oxide
Properties. Pure calcium cyanamide is a colorless crystalline solid, soluble in water (2.5g in 100
ml of water at 25C) and insoluble in alcohol. It is volatile at high temperatures, sublimes at 1090C (at atmospheric pressure), and can be melted
under excessive pressure of nitrogen at 1340C. Dissolved in cold water, it is hydrolyzed forming a soluble acidic salt and calcium hydroxide (eq.1),
while hot water decomposes calcium cyanamide with formation of urea and calcium hydroxide (eq.2), and action of water steam at 110-115C causes release
of ammonia and formation of calcium carbonate (eq.3). At temperatures above 400C calcium cyanamide is readily oxidized by air (eq. 4).
2CaCN2 + 2H2O(cold) → Ca(CN2H)2 + Ca(OH)2
CaCN2 + 3H2O(hot) → Ca(OH)2 + CO(NH2)2
CaCN2 + 3H2O(steam) → CaCO3 + 2NH3
2CaCN2 + 3O2 → CaCO3 + 2N2
Pure calcium cyanamide contains 34.98% of nitrogen. The industrial product has greyish black color due to
contamination by carbon (9-13%), contains 55-65% of pure cyanamide and 18-24% of nitrogen. Additional contaminants (~5%) contain mainly silicic acid,
oxides of iron, magnesium and aluminum. In addition industrial calcium cyanamide contains 14-20% of calcium oxide and 2-5% of unreacted calcium
carbide.
Calcium cyanamide slowly reacts with moisture in the air forming urea, cyanamide, dicyandiamide and ammonia. Calcium
cyanamide is used in agriculture as a nitrogen fertilizer. In chemical industry calcium cyanamide was used to produce cyanides, guanidine and a large
variety of organic compounds.
Calcium cyanamide is toxic and acts mainly as a skin and lung irritant. Toxicity is relatively low but can be raised
greatly then combined with alcohol. Action of cyanamide dust followed by alcohol drinks cause severe poisoning accompanied by agonising suffocation.
This specific toxic effect is reason why cyanamide solutions are proposed for use in anti alcoholism drugs.
Preparation. Calcium cyanamide is produced on an industrial scale by fixation of atmospheric
nitrogen by calcium carbide at temperatures above 1000C in electric furnaces:
CaC2 + N2 → CaCN2 + C
Other methods of preparation include: action of ammonia on cyanogen chloride, melting of urea with metallic sodium,
high temperature reaction of hydrocyanic acid with calcium oxide and thermal decomposition of calcium cyanate. It is clear that only last one is
possible in home scale since calcium cyanurate can be readily produced by melting urea with calcium oxide or hydroxide, but this method require some
work to gain access to high temperature.
The process consists of two main stages – in the first stage is formation of calcium cyanate by melting urea with
calcium oxide. Thermal decomposition of urea is not a simple process and can produce wide variety of products, depending from reaction conditions and
timing, but in presence of alkali it goes almost exclusively to cyanate direction. Mechanism of cyanate formation can be expressed by the following
reactions:
1. 3CO(NH2)2 → 3HOCN + NH3
2. CaO + 2HOCN → Ca(OCN)2 + H2O
3. HOCN + H2O → CO2 + NH3
As one can see, theory requires 3 moles of urea for 1 mole of calcium oxide, since one molecule of cyanic acid is
decomposed by water liberated in neutralization of calcium oxide. Reaction takes place at temperatures above urea melting point (120 - 350C) and
causes formation lots of ammonia gas, accompanied by intensive foaming of the melted mixture. When the process is nearing completion the reaction
mixture re-solidifies due to formation of calcium cyanate which have higher melting point (decompose without melting at higher temperatures). In order
to produce calcium cyanamide, calcium cyanate produced is cooled, grounded in mortar and calcined at high temperature in absence of air oxygen.
The second stage (calcination of calcium cyanate) proceeds at temperatures about 700-900C, producing calcium
cyanamide and carbon dioxide (Eq.1 below). It should be noted that that air oxygen oxidizes produced cyanamide to carbonate (Eq.2 below), and process
should be carried out with very limited air contact or under protective gas atmosphere:
1. Ca(OCN)2 → CaNCN + CO2
2. 2CaCN2 + 3O2 → CaCO3 + 2N2
This reaction proceeds relatively slowly, and it takes about an hour to be substantially complete. Process also
require use of high temperature for extended amount of time and in relatively large volume and ideally can be preformed in laboratory electric
furnace. Since such equipment is not readily accessible for amateur chemist, below i will show you how you can build your own from commonly obtainable
components.
How to build simple 900C oven from OTC materials.
In general the oven consists of ceramic fireproof muffle tube, covered by nichrome wire heating element, covered by
radial fireclay layer which ensures that main heat flow is directed to opposite direction – into the muffle. To prevent heat losses to environment
and allow heating to high temperature the whole construction is protected by heat shielding. Temperature in the muffle is measured by means of
thermocouple. Heat wire is powered by AC power supply which allows voltage regulation – this will allow temperature regulation inside the muffle by
regulating heat flow from heat element.
1. The muffle is fireproof ceramic tube, stable at high temperature, high electric resistance and
able to withstand heat shock. Perfect materials include ZrO2/MgO/Al2O3 based ceramics. Tubes suitable for ovens can be obtained from many sources, for
example from high voltage safety fuses and other high voltage electric components. Tube i used for my oven is zirconium oxide based fireproof ceramic
tube with following dimensions: 90 mm long, 60 mm outer diameter, wall thickness 4 mm.
2. Nichrome heating element was made from 80:20 nickel-chromium alloy, with high electric
resistance, with low temperature-resistance dependence. Nichrome is best for the job because of high electric resistance, high working temperature
(about 1000C) and is stable to air oxidation at such temperatures. I used wire of 0.5 mm diameter, which was wound on the ceramic muffle with narrow
equally spaced turns. To make turns equally spaced the wire is wound in pairs with filament having approximately the same diameter, turns are made
contiguous to each other, and after all wire is coiled filament is carefully removed leaving coil with ideally spaced turns. Coil wire is fixed in
place by two nichrome wire rings spaced near the top and bottom edges of the tube. Don’t forget to provide the coil with some free nichrome wire at
the edges, to exit from the heating element and make contacts with the power supply output line. A photo of my coil is shown below, it has 81 Ohm of
electric resistance.

3.The next thing to do is to determine working voltage and appropriate power supply – those can
be calculated from required power of the heating element. If power is too high wire will simply burn out due to wire melting, if power is too low it
won’t reach high temperature – so optimum values have to be determined. First we need to select appropriate output power for our heat element; for
a small oven like ours 500 watts is a way to go. Now we can determine voltage required to reach desired level of power, by using Joule–Lenz and
Ohm’s laws:
As shown by the calculation above to reach desired power we need to use regulated AC power supply, capable of 200 V
output voltage and current of ~2.5A. To make sure our wire doesn't burn out at such current and determine maximum recommended wire temperature we must
check out current value against maximum allowed current:
As we can see from the table above, for our wire (0.5 mm diameter) maximum allowed current is about 3.5A with
recommended working temperature about ~1000C. Then combined with efficient heat shielding such heating a element would allow us to reach temperature
around 900C. Now we can derive the voltage limit for our heating element and maximum possible power. To do this we must substitute maximum allowed
current to Ohm’s formula to get voltage at Imax and then use the derived voltage to calculate power:
Resuming conclusions above we can now summarize parameters of our heating element: 500W voltage is ~200 V with
current of 2.5A, maximum allowed voltage is 283.5V with current 3.5A and ~1 KW power, recommended working temperature is <= 1000C.
4. Now that our heating element is ready we must complement it with heat shielding and make the
oven body. First we need to cover the nichrome wire with 0.5-1 cm layer of fireclay (I’ve used ~0.75mm thickness). Take some fire clay and add the
least water needed to reach plasticity and cover wire with a clay layer, then the wire is covered and the clay layer is smoothed by rolling on a
smooth surface. The whole device is placed into a kitchen oven to dry for 2 hours at ~250C. When initial drying is finished one can attach contacts of
nichrome wire to power supply and heat it slowly rising voltage to nominal and allow element to sit at this voltage for a while (0.5-1 hour) to
complete drying of the clay layer. Top and bottom caps of muffle can be made in the same manner, but can be worked out without such careful drying,
sitting for 2 hours at 250C kitchen oven is enough. The oven body can be made from an iron can. Carefully remove can cover, remove can contents and
drill two holes in can side walls, those will be required for nichrome wire contacts (my can was 10 cm in diameter and 12 cm height). Fill the bottom
of the can with a layer of magnesium oxide, and place heating element and its clay bottom in the can center, leading wire contacts through the drilled
side holes. Cover holes with contacts with clay to prevent wire short circuit over the oven body and fill the whole space between the heating element
and walls of can with powdered magnesium oxide. To complete the oven you must cover muffle with the clay cover you made earlier and cover whole thing
with iron cover of the can (this second cover will help in prevention of convective heat transfer caused by active air circulation), both covers are
made coaxial and provided with a drilled hole in the center which will be used for thermocouple temperature control.
5. Your oven is now almost ready to use. Just place it into a saucepan of wider diameter filled
with a wide layer of magnesium oxide to minimize heat transfer from oven can (I’ve used saucepan with ~15 cm diameter), place thermocouple to the
top cover of can and attach your oven to the corresponding power supply. I’ve used a laboratory auto transformer (0-220V AC, with maximum secondary
coil current of 4A). Now your heating device is fully operational. The device I’ve described is can reach a temperature of 900C in less then 1.5
hours. A photo of the working heating device is shown below:
Preparation of calcium cyanamide
Preparation of calcium cyanamide was performed according to US patent 5753199. Prepare a mixture of 56.4g (1 mol) of
pure finely ground calcium oxide (Note №1) and 180g (3 mol) of pure fine urea. Mixture is placed to saucepan and heated on a hotplate. As soon
as the urea melts the reaction starts, a lot of ammonia is evolved and mixture begin to foam (Note №2). After foaming subsides, mixture begins
to solidify and became unstirable. Then reaction mixture is completely solidified, heat source is turned off and still hot product is grounded to fine
powder. This yields about 134g of crude calcium cyanate (Note №3). Calcium cyanate is then placed to ceramic crucible, witch is covered by
closely fit clay lid, placed to electric furnace (also provided with closely fit cover) and is heated up to 750-800C for one hour (Note №4).
After this period furnace is turned off and is allowed to cool down, without opening furnace cover. Then temperature in furnace is downed to 150-200C,
furnace cover and crucible is removed and placed to cool on the air. Opened crucible is filled with spongy pinkish-white calcium cyanamide, with small
(about ¼ of crucible) bottom layer of product with grey color (Note №5). Total yield is 69.3g of high quality calcium cyanamide (86% from
theory), containing almost theoretical amount of nitrogen (~33-34%).
Notes:
1. It is essential to use pure calcium oxide, to prevent presence of alkali metal salts in reaction
mixture. Those at first will form corresponding cyanates, witch are unstable at high temperature of second – calcinations stage and will decompose
to form cyanide and oxygen. Even if relatively small amounts of sodium or potassium are present, final product can became much more dangerous since on
action of acids it will realize extremely dangerous and toxic hydrogen cyanide, in quantities easily detectable by smell from such reacting mixture,
or even from solid product itself.
2. Foaming of reaction mixture is very intensive and can easily overflow reactor wessel. This must
be taken to account then choosing volume of reactor. Foam can be sufficiently settled down by intensive mixing. Note that moistured source materials
will not result in even more intensive foaming but will also reduce overall yield due to increased moisture decomposition of cyanic acid.
3. This quantity is larger then theoretical (134g vs 124g theory), this is result of the fact that
solidification and drop of reaction rate occur earlier that source products are completely reacted. It was found that continue of heating after
solidification doesn’t lead to sufficient change of mass and complete transformation. Analysis of reaction product shown clear strong signal for
cyanate, but some small amount of unreacted source products also present. This however is not critical for further calcinations step, since strong
heat will cause them to react further, forming final reaction product.
4. Then this crude cyanate is heated up to about 300-400C, impurities of unreacted urea and calcium
oxide will react/decompose, forming more ammonia. This additional amount of ammonia evolved is quite small but is easily detectable by smell, so it is
advised to perform calcinations in place with good ventilation. Remember to use closely fit lids for both crucible and furnace to prevent oxidation by
air, if such lids are used circulation of waste reaction gases is avoided, allowing them to act as protective atmosphere for main product.
5. Analysis of both colored layers shown that their constituents are exactly the same – both show
strong and clear signal for cyanamide with ammoniacal silver nitrate and both contain only tiny traces of cyanate shown by reaction with cobalt salt
solution. It appears that grey coloration of bottom layer is caused by charring of some organic impurities present in starting cyanate, and is not
related to exact calcination temperature or speed of heating.
Photos:
1. Left photo shows reaction mixture on beginning of foaming, middle one is resulting crude calcium cyanate, latest photo shows product reaction on
cyanate using cobalt salts.
2. Left photo shows furnace operating on calcinations stage, next one shows two layers in final product removed from the crucible, third one shows
final product from mixed layers and last one shows product reaction on cyanamide with ammonacal silver nitrate – yellow coloration is result of
precipitating silver cyanamide.
Attachment: Cyanamide from urea and CaO.pdf (172kB) This file has been downloaded 2261 times
[Edited on 20-8-2010 by Engager]
|
|
rrroket
Harmless
Posts: 3
Registered: 4-8-2010
Member Is Offline
Mood: No Mood
|
|
syntheses CaCN2
Hello Engager
Excellent work!
Several years ago i also tried this synthesis, but worked with calcium hydroxide.
Calcium cyanamide successfully used for the synthesis of AGB. / 50% theoretical yield/. Successfully received and dicyandiamide.
An attempt to synthesis using calcium carbonate gave a product that does not AGPs with hydrazine hydrate!
What were your results in this direction?
/Note - an electronic text is a translation.
Possible ambiguities./
|
|
Taoiseach
Hazard to Others
 
Posts: 241
Registered: 16-3-2008
Member Is Offline
Mood: No Mood
|
|
Very nice work!
How did you measure purity/nitrogen content of the product?
|
|
Engager
Hazard to Others
 
Posts: 295
Registered: 8-1-2006
Location: Moscow, Russia
Member Is Offline
Mood: Lagrangian
|
|
I've done only qualitative tests using ammonical silver nitrate solutions to confirm identity of product. I have not measured nitrogen content myself,
but since i followed procedure from one of patent examples with known quality of product produced, i assume that nitrogen content in my product is
similar to product in patent examples.
|
|
Inorganic
Harmless
Posts: 21
Registered: 1-7-2008
Member Is Offline
Mood: No Mood
|
|
Outstanding work! Maybe i will try to do CaCN2, but i have a problems with my 4,1kW furnace...
|
|
Sedit
International Hazard
   
Posts: 1939
Registered: 23-11-2008
Member Is Offline
Mood: Manic Expressive
|
|
You have passion for chemistry that is matched by vey few Very nice work
Engager always a pleasure to read your work,
Knowledge is useless to useless people...
"I see a lot of patterns in our behavior as a nation that parallel a lot of other historical processes. The fall of Rome, the fall of Germany — the
fall of the ruling country, the people who think they can do whatever they want without anybody else's consent. I've seen this story
before."~Maynard James Keenan
|
|
chemoleo
Biochemicus Energeticus
   
Posts: 3005
Registered: 23-7-2003
Location: England Germany
Member Is Offline
Mood: crystalline
|
|
Very nice, Engager.
It's a shame you didn't use the forum scipics directory - give it a few years and your pictures will be gone!
Next step is the making of guanidine compounds?
Never Stop to Begin, and Never Begin to Stop...
Tolerance is good. But not with the intolerant! (Wilhelm Busch)
|
|
maxidastier
Hazard to Others
 
Posts: 118
Registered: 3-4-2010
Member Is Offline
Mood: No Mood
|
|
Next step is the making of guanidine compounds?
There is another thread existing about preparation of Guanidinitrate.
We discussed, that Calcium Cyanamide is banned in Russia, but in Germany is readily available in fertilizers cheap 
|
|
Engager
Hazard to Others
 
Posts: 295
Registered: 8-1-2006
Location: Moscow, Russia
Member Is Offline
Mood: Lagrangian
|
|
Remarks on preparation of calcium cyanamide
Note: Information obtained from experiments described below, was used to update main post in this topic,
witch is now updated by modified reaction procedure.
As mentioned earlier it was found that calcium cyanamide produced from precipitated CaCO3 and urea fertilizer was
not essentially pure for production of aminoguanidine. So taking to account rrrocket's statement, big effort has been made to produce pure calcium
cyanamide - this time from pure CaO and urea starting materials (both bought from chemical supplier and is no more impure fertilizer product).
Decision to use chemically pure CaO was made due the statement of rrrocket and due to it's purity from alkali metal salts (those will produce cyanide
on calcination stage).
First of all much more reference work has been made to gain information on detailed reaction mechanism and
conditions and lead to first major improvement. It was found in some references, that 1 mole cyanamide actually require 3 moles urea, not 2 as basic
theoretical view can predict, this is due to the following reactions:
1. 3CO(NH2)2 => 3HOCN + 3NH3
2. CaO + 2HOCN => Ca(OCN)2 + H2O
3. HOCN + H2O => CO2 + NH3
4. Ca(OCN)2 => CaNCN + CO2
So the synth i proposed (using 2 mole urea vs 1 mole of calcium oxygen compound) is no good due to lack of urea to
fully complete conversion to cyanate. Another improvement to process was realized then more experimentation with new ratio has been done - it was
found that then mixture is calcined in open crucible placed in closed electric furnace i've described - results in large of contamination by cyanamide
oxidation product - calcium carbonate. Resulting product is snowy - white powder, then pure calcium cyanamide prepared under protective atmosphere was
found to be pinkish. So great care should be taken to protect calcinating product in the reactor out of air contact, covering crucible with relatively
tight lid and placing in to furnace covered in same manner found to be satisfactory to produce quite pure calcium cyanamide.
Here are results from second line of cyanamide experiments i've preformed: 56g of pure calcium oxide were mixed with
180g of pure crystalline urea and mixture was melted as mentioned in procedure in top of topic. Resulting first stage product is weighted 135g vs 124g
theoretically predicted - this indicates that some ammount of unreacted urea and calcium oxide still present in solidified reactor mixture. Effort has
been made to force this stage to complete by grinding solidified mixture and applying more heat for extended time period, it was found that reaction
(and decrease of mixture mass) proceeds very slowly and it is not profitable to do this additional heating at first stage. Resulted product was
analyzed for presence of cyanate and it was found that mixture consists mainly from calcium cyanate while some 5-6% of unreacted urea + CaO still
present in the mixture. Photos of this reaction product as well as colored reaction it gives in cyanate test are shown below:

Calcination of resulting product out of air contact, as expected resulted in calcium cyanamide, however some
interesting results have been obtained. Removing product from crucible after cooling shown that product consists from 2 layers, lower layer (~1/4 of
crucible height) was filled with grey product, while upper layer (~3/4 crucible height) consisted from pinkish-white product. This was confusing at
first and i thought it may be from some crucible impurity, later experiments shown that such stuff happens with any batch in more or less ammount,
however ammount of grey product is always much smaller. After this to parts separated both vere analyzed for cyanamide pressence using ammoniacal
silver nitrate and in both cases clear and strong signal of cyanamide was observed, as formation of bright pale-yellow silver cyanamide precipitate.
In addition both samples vere tested for cyanate presence, and in both cases only traces of them were discovered. In total from 135g of starting
material from first step (calcium cyanate) 68.9g of calcium cyanamide was produced, this corresponds to 87% theoretical based on starting urea and
calcium oxide. Photos of 2 layers, final product and product test for cyanamide are shown below:
[Edited on 20-8-2010 by Engager]
|
|
Rosco Bodine
Banned
Posts: 6370
Registered: 29-9-2004
Member Is Offline
Mood: analytical
|
|
Attached is a page from Thorpe which mentions an obscure but interesting reaction I haven't seen before. Fusion of Sodium Cyanate with Sodium
Hydroxide produces Disodium Cyanamide. No reaction conditions are stated so the equation below is presently my speculation how that
reaction mentioned by Thorpe may proceed. The required temperature for the reaction would be interesting to know.
3 NaOCN + 3 NaOH ------> Na2CN2 + 2 Na2CO3 + NH3
The implication for this reaction if it is true and valid is that
it may be possible to produce Disodium Cyanamide directly
from the heating of Sodium Hydroxide and Urea together,
in the same manner as would be done to produce Sodium Cyanate, but providing an additional amount of Sodium Hydroxide as would further react with the
Sodium Cyanate and convert it to Sodium Cyanamide.
The conversion of urea to Potassium Cyanate is quantitative by this method. The same reaction appears to be less efficient for Sodium Cyanate as
described in similar patents.
However, those similar patents describe reaction of urea with Sodium Carbonate, rather than reaction of urea with Sodium Hydroxide. Attached are some
related patents of possible interest.
Here it may be possible also to utilize the cyanuric acid salt of the base for a desired cyanamide product as an alternative. If the conversion
temperatures are not excessive, it may be better in terms of the subsequent hydrazine sulfate reactions to avoid the voluminous insoluble sulfate
byproduct precipitate which may complicate filtering and isolation of the cyanamide derivative, to work from a different cyanamide than the calcium
salt.
Alternatively, it may be easier to precipitate the calcium as a phosphate or borate, in advance of the hydrazine sulfate reaction with the soluble
cyanamide.
Attachment: Cyanamide page from Thorpe_dictionary_of_applied_chemistry.pdf (240kB) This file has been downloaded 2040 times
Attachment: US3935300 Potassium Cyanate via KOH and Urea.pdf (301kB) This file has been downloaded 2456 times
Attachment: US3167387 Cyanates via DMSO solvated Urea and Carbonate .pdf (404kB) This file has been downloaded 2398 times
[Edited on 19-8-2010 by Rosco Bodine]
|
|
rrroket
Harmless
Posts: 3
Registered: 4-8-2010
Member Is Offline
Mood: No Mood
|
|
For better insulation from the air on the lid of the oven pour quartz sand.
I also watched the formation of gray items in 1/4 of the reaction mixture!
I thought that this is due to the fact that I use very long furnace reactor / diameter 45 mm, length 300 mm/
So someone is cause charring organic residues and can not be separated.
It appears this is not the reason.
Also 30 minutes after reaching a temperature of 700-750 degrees leaking gas products are capable of burning with a blue flame.
At the end of the separation of these reaction products are terminated.
/Note-text is machine translation.
Possible inaccuracies/
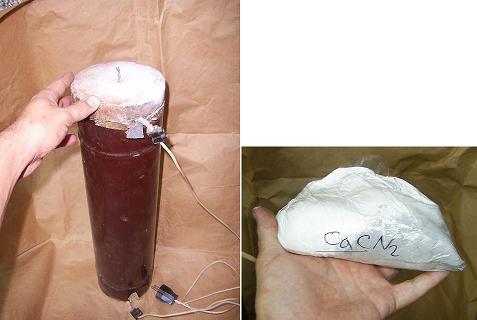
[Edited on 19-8-2010 by rrroket]
|
|
Rosco Bodine
Banned
Posts: 6370
Registered: 29-9-2004
Member Is Offline
Mood: analytical
|
|
The reported fusion reaction of a cyanate with caustic hydroxide is described in the middle of the page linked below. It is page 496
http://books.google.com/books?id=cQoSAAAAIAAJ&pg=PA496&a...
See the footnote 33a at the bottom of that page 496 as it appears that my speculation about the reaction equation posted earlier is correct. hehehe
.....sometimes I get 'em right guessing and I sure feel better about having guessed when it works out that way I am going to try to get the information about the required temperature for that fusion reaction. Reference
requests are pending which should provide further information. I suspect that sodium or potassium or other alkali cyanurate would decompose directly
on pyrolysis via an intermediate cyanate to eventually form the alkali cyanamide, similarly as occurs for calcium acid cyanurate. This may provide a
shortcut if cyanuric acid is available.
Another interesting reaction which I have found mentioned in the literature involves the reaction of thiourea with metal oxides which precipitate an
insoluble metal sulfide byproduct
and leave cyanamide as the other product. This reaction of thiourea is reported for mercuric oxide and lead oxide, but probably works for other metal
oxides or possibly other metal salts as well. If thiourea is easily available this method may be useful as an alternative route to cyanamide.
It is not clear what are the reaction conditions, but this reaction possibly may occur in solution in H2O, and if so this may be a very easy source
for cyanamide via thiourea.
The reaction using the oxide of mercury is:
(NH2)2CS + HgO ----> H2NCN + HgS + H2O
Perhaps Zinc Oxide would also work the same way.
Also I am wondering is if thiourea would react with sodium zincate to result in zinc sulfide precipitating from a residual solution of Disodium
Cyanamide
(NH2)2CS + Na2Zn(OH)4 -----> Na2CN2 + ZnS + 4 H2O
[Edited on 19-8-2010 by Rosco Bodine]
|
|
Engager
Hazard to Others
 
Posts: 295
Registered: 8-1-2006
Location: Moscow, Russia
Member Is Offline
Mood: Lagrangian
|
|
Preparation of aminoguanidine bicarbonate from calcium cyanamide and hydrazine sulphate.
This alternative route to aminoguanidine is known to me for a long time, however it took time to find enough free
time to do extensive experimentation like that, since it required not only extensive chemistry work but also construction of electric furnace suitable
for production of cyanamide. Finally all this work arouse in success and pure cyanamide based aminoguanidine was obtained, leading alternative way to
home made tetrazole compounds.
Preparation of aminoguanidine was carried out on base of procedure described in US Patent 3673253, and is based on
condensation of cyano-group in free cyanamide with hydrazine. Reaction of hydrazine sulphate with calcium cyanamide in aqueous media results in
formation of insoluble calcium sulphate and liberation of free cyanamide and hydrazine, witch react with each other in basic media forming
aminoguanidine. Since cyanamide is quite reactive and can readily form dimeric form – dicyandiamide witch doesn’t produce aminoguanidine on
reaction with hydrazine, this side reaction leads to decreased yield of final product. Reaction conditions, mixture pH and temperature are controlled
in such manner witch allows to overcome this side process. This is achieved by keeping minimal concentration of cyanamide and decreasing pH by
addition of sulpuric acid to level keeping conversion to dicyandiamide at minimum while still allowing fast condensation process for cyanamide and
hydrazine. Reaction scheme is shown on picture below:

Procedure:
55.8g of monohydrazine sulphate (0.429 mol) and 40g of finely ground calcium cyanamide containing 30% N (~0.5 mol)
were simultaneously and uniformly added with vigorous stirring to 200 ml of water at pH value of 9.5 (Note №1). The pH value was regulated by
the addition of 50 percent sulfuric acid in an appropriate quantity (Note №2). The reaction temperature was kept at 40C. After reaction mixture
had been stirred for 30 minutes at pH 9, the pH value was adjusted to 7 and the mixture was heated for about 1 hour at 80C at that pH value. After
reaction mixture had been cooled to 60C, it was filtered and the filtration residue, consisting essentially of calcium sulfate, was washed with 200 ml
of warm water (Note №3). Both the filtrate and water used for washing were collected in a precipitation vessel and were adjusted to a pH value
of 6.5 with 50 percent sulfuric acid. 36.9g of sodium bicarbonate were then slowly and uniformly added at 30C as a result of which the aminoguanidine
bicarbonate was separated as fine white precipitate. Precipitate is filtered, washed with small amount of cold water and dried. Product is white
microcrystalline powder, yield is 49.1g (85% based on hydrazine, Note №4).
Notes:
1. This pH range can be achieved without adding sulfuric acid – by adding components in
corresponding rate, however it can also be justified by addition of acid. Addition can be carried out in portions, adding new portion, stirring for
1-2 minutes then adding new one e.t.c. Addition should not produce any gas or significant odor, if such are present – your cyanamide is impure and
yield be lowered. Use of cyanamide contaminated with alkali metals on this step will lead to formation of hydrogen cyanide witch will be noticeable by
odor, while cyanamide significantly oxidized by air during production (e.g containing carbonate) will form a lot of bubbles of carbon dioxide gas.
2. Total amount of sulfuric acid, consumed during whole reaction process is equivalent to 12-15 ml
of concentrated 96% H2SO4. It should be noted that not uniform addition of sulfuric acid will cause high local concentrations of H2SO4 and formation
of solid/gases, so if H2SO4 is added by portions for example from syringe, addition must be accompanied by vigorous stirring to prevent loss of
reactants.
3. Precipitated calcium sulfate consist from particles of relatively large size and filtration
proceeds with ease. Total amount of water used for washing is not critical however 200 ml is reasonable amount. One can notice that filtrate obtained
has distinctive yellow coloration common for solutions of aminoguanidine salts.
4. Product yield can vary depending on quality of starting cyanamide and from care with witch
correct pH ranges are controlled.
Photos:
1. Left photo shows reagents – calcium cyanamide and hydrazine sulfate used for reaction, second photo is reaction
mixture in the middle of reagent addition, third one is heating stage, last photo shows reaction mixture with calcium sulfate precipitate, obtained
after heating period.
2. Left photo shows filtration from calcium sulfate, second is filtrate produced –note that this yellow color is
common for solutions of aminoguanidine salts, third photo is precipitate of aminoguanidine bicarbonate formed after addition of sodium bicarbonate,
fourth photo shows final filtering, last photo is white pure aminoguanidine bicarbonate produced by the process.
[Edited on 20-8-2010 by Engager]
Attachment: US3673253 - Aminoguanidine from calcium cyanamide and hydrazine sulfate.pdf (385kB) This file has been downloaded 3531 times
|
|
Engager
Hazard to Others
 
Posts: 295
Registered: 8-1-2006
Location: Moscow, Russia
Member Is Offline
Mood: Lagrangian
|
|
Quote: Originally posted by Rosco Bodine  | This reaction of thiourea is reported for mercuric oxide and lead oxide, but probably works for other metal oxides or possibly other metal salts as
well. If thiourea is easily available this method may be useful as an alternative route to cyanamide. It is not clear what are the reaction
conditions, but this reaction possibly may occur in solution in H2O, and if so this may be a very easy source for cyanamide via thiourea.
|
Actually this is dead end, a read a lot of references on such reactions, you may find some of them in my requests in references section. It is known
that thiourea is significantly desulfurized only by fresh mercury oxide, with lead process goes much harder and yields are low. This is crazy stuff,
considering quantities, expense and toxicity of this oxides. And by the way have you actually counted how much HgO will be needed to produce 1 mole -
40g of cyanamide? 216g of mercury oxide and corresponding amount of waste.... still think this is a good idea? Try it yourself - i grantee you, that
you will never want to repeat this insanity again! Silver salts work as well but they are even more expensive, also it was found that cyanamide can be
produced by oxidation of thiourea by KMnO4 (sulfur is oxidized all way to sulfate), however in this case product separation is real pain, especialy
considering that cyanide is also produced. Disodium cyanamide can also be produced by fusing urea with metallic sodium, but reaction is vigorous -
resulting hydrogen even sets on fire, so this is also nasty.
[Edited on 20-8-2010 by Engager]
|
|
Rosco Bodine
Banned
Posts: 6370
Registered: 29-9-2004
Member Is Offline
Mood: analytical
|
|
Congratulations on getting the calcium cyanamide to cooperate. I knew pH was going to be an issue 
On the alternative methods, I did not know you had already looked at the thiourea approach, and really I was not thinking about it as potentially
useful unless perhaps the zinc oxide or sodium zincate approach may be workable, as a variation.
However, some of your countrymen have also studied the alternative using cyanurate, and confirm what I have proposed as a more direct route, at least
for calcium, strontium, barium, and lead. There may possibly be others which also work under modified conditions of pH , for example if there is a
caustic hydroxide present it may work for the sodium and potassium cyanurate via a cyanate intermediate. The study was not extended to experiments
with such possibilities. However it is a very informative article
and I attach here the English translation for others.
Congratulations again on getting the precipitate to cooperate. Calcium sludges of carbonate, sulfate, ect, can be very troublesome if the conditions
are not perfect for a filterable granulation to form. This can be difficult for anyone to perform that tricky manipulation with good results.
Also attached is the Drechsel article but it only has a brief mention of the reaction of a fusion of cyanate with alkali.
See page 1 lines 97-101 of US1630769 for a similar use of Sodium Zincate. In the absence of ammonia instead of a guandine end product, wouldn't
thiourea possibly lead to the cyanamide as I was suggesting ?
Attachment: Cyanuric Acid and Cyanurates .pdf (332kB) This file has been downloaded 13835 times
Attachment: php019VGM.pdf (1.9MB) This file has been downloaded 1745 times
Attachment: US1630769 Sodium Zincate for Desulfurization of Thioureas.pdf (271kB) This file has been downloaded 1769 times
[Edited on 20-8-2010 by Rosco Bodine]
|
|
Rosco Bodine
Banned
Posts: 6370
Registered: 29-9-2004
Member Is Offline
Mood: analytical
|
|
Calcium Oxide alternative
The problems which were reported for use of Calcium Carbonate and Urea may have not only been due to the use of fertilizer grade materials of
insufficient purity. The need for ordering chemical grade Calcium Oxide and Urea would change the process to not using strictly OTC materials. So
there are alternatives which should be kept in mind. Urea is available pure and cheaply as a feed additive for livestock.
Such "food grade urea" or possibly the less pure fertilizer grade urea may be both usable as a precursor for cyanuric acid, which is gotten in 85%
yield by heating 2 parts urea with 1 part ammonium chloride for 15 minutes at 250C, according to US2527316. The same Cyanuric Acid Dihydrate is also
sold in pure form as "chlorine stabilizer" for swimming pools water treatment. The usefulness of Calcium Cyanurate as an alternative precursor not
requiring Calcium Oxide becomes apparent. The low solubility of Calcium Cyanurate allows for its precipitation in pure form from reaction of Disodium
Cyanurate and a soluble calcium salt like Calcium Chloride, which is available as a dehumidifier and is also sold as a deicer, or can be made from
hydrated lime and muriatic acid. Calcium Cyanurate depolymerizes on heating to Calcium Cyanate which on heating to higher temperature decomposes to
Calcium Cyanamide. This parallels the reactions gotten from heating Calcium Oxide and Urea, which leads to a mixture of Calcium Cyanurate and Calcium
Cyanate, both (or either) of which ultimately decompose via pyrolysis to Calcium Cyanamide. See US3173755. Actually, the process using the
precipitated Calcium Cyanurate precursor may have some advantage
because it eliminates the liquid and gas / solid reaction which
operates with the Calcium Oxide and Urea reaction, and provides a completely formed and pure precursor gotten as a solid product precipitated from
reacting solutions. Therefore the Calcium Cyanurate alternative should be kept in mind with regards to strict use of over the counter common
materials.
[Edited on 23-8-2010 by Rosco Bodine]
|
|
Engager
Hazard to Others
 
Posts: 295
Registered: 8-1-2006
Location: Moscow, Russia
Member Is Offline
Mood: Lagrangian
|
|
Last week i got more experience on urea/CaO process, and gathered some new facts:
1. I managed to determine actual cyanate presence in Urea/CaO melting product, by means of flushing
small sample with large amount of water, filtering and precipitation of cyanate by means of lead acetate. Insoluble lead cyanate is filtered, washed
and dried. This resulted in 1.38g of lead cyanate from 5g crude cyanate/cyanurate sample. Product of first stage found to contain a lot of water
insoluble product thought to be calcium cyanurate. This is in agreement with theoretical view of the article Roscoe posted, "Cyanuric Acid and
Cyanurates" Table 4, witch shows that conversion to cyanate require better heating, and solidified product must be mostly cyanurate. Observation on
loss of mass during the first stage, shown that reaction product obtained then reaction mixture solidifies has greater mass than assumed by
theoretical view:
3CO(NH2)2 => 3HOCN + 3NH3
CaO + 2HOCN => [Ca(OCN)2]
HOCN + H2O => CO2 + NH3
For example fusion of 56g (1 mol) of CaO and 180g of urea (3 mol) should give 1 mol - 124g of cyanate/cyanurate,
while experiment gives 132g of solidified product. However if product is finely grounded and reheated for more time on saucepan it found to loose mass
further and theoretical mass of 124g may be obtained in such manner.
2. Previous runs of second stage - pyrolysis of cyanate shown that portion of product was colored
due to presence of carbon, derived from organic impurities in source cyanate/cyanurate. I was able to completely evade carbonization of final product.
I found that carbonization did not occur if final stage is carried out at 700C for 30 minutes. At first i was wondering if pyrolysis will be complete
in such short period - however experimental data on weigh loss shown that conversion is essentially complete. Reaction equation:
Ca(OCN)2 (124g, 1 moll) => CaNCN (80g, 1 mol) + CO2
Shows that weight loss in such process must be 35.5% of mass of initial cyanate, experiment for 26g sample of
cyanate/cyanurate shown weight loss to 14.2g (11.8g vs 9.24 theoretical). This indicates that conversion is essentially complete and that some
cyanate/cyanurate impurities are also decomposed.
3. I've managed to preform quantitative analysis of product produced as described above. 1g of
product was added to 150 ml of cold water and stirred for several minute, 2-3 ml of 70% HNO3 is added and mixture is stirred until all solid is
dissolved and transparent solution is obtained. After this solution is complemented with 4 ml of 25% ammonia, and solution of 4.5g of silver nitrate
in 50 ml of water with stirring. On addition of ~40 ml more of 25% ammonia silver cyanamide is precipitated as pale yellow mircrocrystalline solid.
Mixture is stirred for 10 minutes, precipitate is filtered off, washed with water and alcohol and dried. Silver cyanamide is weighted and checked
against theoretical of 3,197g for 100% calcium cyanamide. Analysis for my sample shown that is gives 2.85g of silver precipitate, indicating that
sample contained 89.15% of pure calcium cyanamide, corresponding to nitrogen content of 31.2% (vs 34% calculated for formula CaNCN)
[Edited on 31-8-2010 by Engager]
|
|
Rosco Bodine
Banned
Posts: 6370
Registered: 29-9-2004
Member Is Offline
Mood: analytical
|
|
What you are reporting is consistent with what I was expecting after reading the published methods. The 90% purity Calcium Cyanamide product is
sufficent for use in synthesis so it is a useful method. However, a modified procedure seeking pure Calcium Cyanurate as the precursor for pyrolysis
should produce a quantitative yield of chemically pure Calcium Cyanamide.
The Calcium Cyanamide product should be 100% pure if derived from a pure Calcium Cyanurate intermediate. Side reactions occuring in a melt are
eliminated by use of a pure Calcium Cyanurate precursor precipitated from solution.
Precipitated Calcium Cyanurate is possibly a trihydrate which has been identified in the Russian article, CaH(OCN)3 - 3 H2O. The hydration level is
possibly dependant upon the temperature at which the precipitation is conducted, and it could be anhydrous or a lower hydrate for the precipitate
gotten from near boiling hot solution / stirred suspension method as I used. Upon heating a hydrate would lose water decomposing to the anhydrous
salt first, with evolution of steam. At a higher temperature the Calcium Cyanurate would depolymerize to Calcium Cyanate, evolving a mole of gaseous
cyanic acid. And at a still higher temperature the Calcium Cyanate would decompose via pyrolysis, evolving CO2 and leaving pure Calcium Cyanamide.
I would have to review the literature to be certain, but if I recall correctly there was some reference which was made in an old British patent to a
parallel reaction possible for Zinc which occured at a slightly lower temperature requirement for the pyrolysis. I am not sure if this is correct, it
was my own liberal interpretation of the reference, and there may be a discrepancy with the Russian study which provides more detailed information
from actual experiments. Sometimes my theory is good and sometimes..... not so good Experiments are always better.
There were some threads where we were discussing this general reaction several years ago that have overlapped and been thread split, so as not to
interfere with your compilation. It is good to see your recent experiments which illustrate some of the reactions that are possible. Here are links
to two of the older threads and there are several more.
http://www.sciencemadness.org/talk/viewthread.php?tid=8594&a...
http://www.sciencemadness.org/talk/viewthread.php?tid=2762&a...
Edit 09-02-2010: I found two old references which may be helpful with regards to possibly useful modifications or variations / alternatives. In the
post above where I mentioned the Thorpe reference, I also said something about the possible usefulness of precipitation of the Calcium of the Calcium
Cyanamide as phosphate or borate. I found an old British patent GB109825 (attached) which describes an increased yield of aminoguanidine bicarbonate
from a reaction mixture where Boric Acid is used as a buffer for pH. The reaction described by the patent is for free cyanamide and hydrazine
sulfate. It occurred to me further that the free cyanamide solution described could likely be produced in the first place by hydrolysis of the
Calcium Cyanamide with a Boric Acid solution, or alternately perhaps by a solution of Borax titrated with HCl, achieving precipitation of the Calcium
species as borate, which may (or may not) be more easily filtered. Depending upon the capability and compatability of such buffering, this may be
advantageous with regards to processes which do not isolate the aminoguanidine, but proceed to nitrosation and / or other reactions leading to
isolation of a different eventual product for which the aminoguanidine was an intermediate not necessarily having need of being isolated as
bicarbonate or other salt.
The second reference is US1842018 which briefly mentions Zinc Cyanamide from Zinc Cyanurate or Zinc Cyanate as an intermediate for pyrolysis. The
process described is an inefficient gas / solid reaction not done upon an isolated pure Zinc Cyanurate as I contemplated would be better. However, it
was interesting to me that the pyrolysis did appear to occur at a somewhat lower temperature requirement than for the Calcium compound, showing that
the Zinc Cyanamide is perhaps more easily won. How well or difficult the Zinc Cyanamide may fare as a precursor in later reactions is unknown, so
this may be of value or may not be of any use. The Zinc Cyanamide intrigued me somewhat for the lower temperature requirement and the possibility
that the Zinc may possibly be recycled.
Attachment: GB1089825 Aminoguanidine Bicarbonate using Boric Acid as buffer.pdf (190kB) This file has been downloaded 1793 times
Attachment: US1842018 Zinc Cyanamide.pdf (139kB) This file has been downloaded 1807 times
[Edited on 3-9-2010 by Rosco Bodine]
|
|
Rosco Bodine
Banned
Posts: 6370
Registered: 29-9-2004
Member Is Offline
Mood: analytical
|
|
a followup note
There is an additional observation which I would make concerning the potential usefulness of the fusion reaction of Sodium Cyanate and Sodium
Hydroxide to produce Disodium Cyanamide probably at lower temperatures than required for
producing Calcium Cyanamide. The Drechsel reaction referenced by Thorpe is
3 NaOCN + 3 NaOH ------> Na2CN2 + 2 Na2CO3 + NH3
If this reaction does proceed as reported, the disodium cyanamide produced would provide a precursor for aminoguanidine via reaction with hydrazine.
Disodium Cyanamide would also provide a precursor for guanidine salts, via a higher yield method and at a lower temperature, while not requiring the
use of a silica catalyst as when urea is used directly as precursor. The method is described by GB507498 attached.
This scheme could possibly provide a route to guanidine nitrate or other guanidine salts under milder conditions
from starting materials of Urea and Sodium Hydroxide
to form the Sodium Cyanate intermediate, fused with additional Sodium Hydroxide to form the Disodium Cyanamide
precursor, then reacted with an ammonium salt of the acid desired for the guanidine product of the reaction sequence. In a commercial scheme, the
byproduct ammonia
could be used for neutralization of an acid to provide the
ammonium salt for process economy.
With regards to a somewhat related matter, involving the exothermic and hazardous fusion reaction of dicyandiamide and NH4NO3 to produce guanidine
nitrate, it has been a matter of some curiosity for me if DMSO might be useful for moderating the reaction, via the 189C boiling point for DMSO,
and if the reaction may proceed for the DMSO solvated reactants. This curiosity about possible usefulness of DMSO extends also to the fusion reaction
of the cyanate and caustic alkali to produce Disodium Cyanamide. DMSO has been reported useful in the synthesis of the Cyanate, which
leads to the suspicion that DMSO may have usefulness also
in the other reactions. If true, then DMSO could be very
useful through the entire process, which may even be
reducible to a stepwise one pot process for urea conversion to guanidine salt, conducted under relatively mild conditions
in DMSO solution. This is hypothetical, but it could be basis for interesting experiments, as the inferences this may be possible appears to be there
in the existing literature.
Attachment: GB507498 Guanidine Nitrate from Cyanamide H2O and NH4NO3.pdf (413kB) This file has been downloaded 1768 times
[Edited on 12-6-2011 by Rosco Bodine]
|
|
Rosco Bodine
Banned
Posts: 6370
Registered: 29-9-2004
Member Is Offline
Mood: analytical
|
|
Related followups are also posted in replies in other threads
http://www.sciencemadness.org/talk/viewthread.php?tid=23&...
http://www.sciencemadness.org/talk/viewthread.php?tid=9128&a...
[Edited on 22-8-2011 by Rosco Bodine]
|
|
Hawkguy
Hazard to Others
 
Posts: 326
Registered: 10-10-2014
Location: British Columbia (Canada eh!)
Member Is Offline
Mood: Body is Ready
|
|
Hmm I've tried this twice, and I must be making some mistake I don't know about, because the procedure hasn't worked either time. The problem is in
the step when I roast the Calcium Cyanate. I have managed to get good Cyanate, but it won't decompose to Cyanamide. The furnace/ thing I'm using is
hot enough to melt borosilicate glass, as well as turn steel bright hot, my best guess at 850 degrees C. The crucible is a steel crucible (well no
shit) with about 1 - 2 mm thickness. I roast it for an hour at the high heat, but it always tests negative for cyanamide. What can I improve? This is
like a bit frustrating.
|
|
Tdep
National Hazard
  
Posts: 519
Registered: 31-1-2013
Location: Laser broken since Feb 2020 lol
Member Is Offline
Mood: PhD is done! It isn't good but it's over lol
|
|
Can you test how much carbonate is in it? You could be letting too much air in and it just oxidises, especially if you roast it for a really long
time, eventually the air is going to destroy it
|
|
Great
Harmless
Posts: 34
Registered: 8-2-2016
Member Is Offline
Mood: No Mood
|
|
Hmm Okay so I tried to make Calcium Cyanate through the method with Alkali Cyanate. Here is what I got. I suck shit at descriptions so hopefully it
makes sense.
20g of Urea was weight out and added to my ol' shitty crucible, a very thick steel can of sorts that turned up somewhere. The Urea is $2/100g at the
grocery store as cold packs, and usually they're fine with me buying them all because I'm their friendliest customer.
7g of Sodium Hydroxide, somewhat dry, was also prepared and added to the can. I'm using slightly more Hydroxide than required because water formed
during the reaction (which destroys HCNO) evaporated on a greater scale than expected during the last attempt, and I think I can get away with a bit
extra Hydroxide. (I know it evaporated because I collected the vapors from the crucible and got water.) The Sodium Hydroxide was $15 for 5lb from the
hardware store, and very pure. I only got the deal because of some weird product mix up or whatever that left them with a large but not really well
labeled jug of Sodium Hydroxide.
The mixture was heated on a propane camping stove, and despite lack of real insulation/ containment, crucibles heated over the flame can easily reach
~700 degrees C. In this case however, It was only heated to 600 or do degrees on a lower flame because huge heat isn't required for the reaction.
Everything melted quickly, and became a white foamy mix. The can was not immediately corroded, and a lot of white vapour was produced, as well as
ammonia. The vapour was collected, and idfk what it is. It condenses and becomes a white solid at room temperature (5 degrees in Canada right now
lol).
After a while, the mix solidified, and was allowed to cool. I dissolved it in water after grinding into a powder, and added a few drops of weak acid
to destroy any remaining Hydroxide, or Carbonate, which had somehow formed. I did this because I want the precipitate to be all Calcium Cyanate later
in the experiment, and Calcium Hydroxides or Carbonates formed would have precipitated.
I went to the beach and picked up some shells. The shells here are almost pure (almost lol) Calcium Carbonate, and they are everywhere. Sometimes
birds drop them in the yard too, so thats nifty. I crushed up the shells and dissolved them in 34.45% HCl from the store, which is quite pure except
for a slight Ferrous Chloride contamination that makes the stuff SLIGHTY yellowygreen. The Calcium Chloride produced should be an excess, I didn't
bother measuring it.
The Calcium Chloride solution was filtered to remove residual Silicon Dioxide n stuff, and so was the Sodium Cyanate. I mixed them together and looked
at them without safety glasses for awhile because I'm a bad boy. A white precipitate immediately formed, redissolved, and precipitated again after an
hour in the freezer. The stuff reminds me of Calcium Hydroxide snot I made from shells, because of the fine, paste-like properties. It seems to be
quite pure, and if it actually is Calcium Cyanate, I will be a happy guy for days to come.
I've had extended problems making Calcium Cyanamide recently, so I assumed the problem was from Calcium Hydroxide in the Cyanate decomposing the
Cyanamide whilst being fired in the crucible when the Hydroxide releases water. (Previously I prepared all my Cyanate from Calcium Hydroxide.)
Hmm. I can't tell if theres anything wrong with what I did, but posting crap here usually helps someone.
EDIT: Now that the Calcium Cyanate is drying out, I can see that it is a grey solid in its pure form. Previously I thought that it had acquired the
color due to residual contamination, but now I see otherwise. Not really a big deal, but I still found it interesting.
[Edited on 13-2-2016 by Great]
|
|
PHILOU Zrealone
International Hazard
   
Posts: 2893
Registered: 20-5-2002
Location: Brussel
Member Is Offline
Mood: Bis-diazo-dinitro-hydroquinonic
|
|
Quote: Originally posted by Great  |
Everything melted quickly, and became a white foamy mix. The can was not immediately corroded, and a lot of white vapour was produced, as well as
ammonia. The vapour was collected, and idfk what it is. It condenses and becomes a white solid at room temperature (5 degrees in Canada right now
lol). |
Probably ammonium carbonate...
2 NH3 (g) + CO2 (g) + H2O (g/l) <----> (NH4)2CO3 (s)
[Edited on 14-2-2016 by PHILOU Zrealone]
PH Z (PHILOU Zrealone)
"Physic is all what never works; Chemistry is all what stinks and explodes!"-"Life that deadly disease, sexually transmitted."(W.Allen)
|
|
S.C. Wack
bibliomaster
   
Posts: 2419
Registered: 7-5-2004
Location: Cornworld, Central USA
Member Is Offline
Mood: Enhanced
|
|
Quote: Originally posted by Great  | The Calcium Chloride solution was filtered to remove residual Silicon Dioxide n stuff, and so was the Sodium Cyanate. I mixed them together and looked
at them without safety glasses for awhile because I'm a bad boy. A white precipitate immediately formed, redissolved, and precipitated again after an
hour in the freezer. The stuff reminds me of Calcium Hydroxide snot I made from shells, because of the fine, paste-like properties. It seems to be
quite pure, and if it actually is Calcium Cyanate, I will be a happy guy for days to come. |
It would not be a surprise if your precipitate is calcium hydroxide and carbonate. Making alkali cyanate with the Inorganic Syntheses directions, or
calcium cyanate with patent specifications (e.g. US2801154 and 3222126, good luck) might be more rewarding.
Here is what "performed according to US patent 5753199" means:
Example 1
500 g urea and the amount corresponding to the respective molar ratio (186 or 155 g) of calcium oxide (particle size <500 μm) were melted in a
tubular reactor at 150° C. (residence time 7 minutes) and subsequently applied to a rotating roller dryer which had been heated to various
temperatures as stated in Table 1. The solid reaction product that formed was scratched off with the aid of scrapers after a residence time of 10
minutes and then calcined for 1 hour in a rotating tube under a nitrogen atmosphere at a temperature of 750° C
Example 2
500 g urea and the amount corresponding to the respective molar ratio (233 or 186 g) of precipitated lime (particle size <200 μm) are melted down
in a tubular reactor at 150° C. (residence time 12 minutes) and subsequently reacted for 1 hour at 350° C. in a rotating tube in the presence of
porcelain balls (diameter 20 mm).
After the first reaction step is completed, the reaction product is calcined for 1 hour at 750° C. in a settling furnace under a nitrogen atmosphere.
Example 3
73 kg/h urea and 27 kg/h CaO are melted down in a stirred tank at ca. 160° C. (residence time ca. 10 minutes) and the melt is continuously rolled and
compressed in a subsequent heated kneader. The temperature at the entrance of the kneader is ca. 235° C., and ca. 275° C. at the product discharge
point. After a throughput of 1400 kg reaction mixture, 884 kg of product are obtained which is converted into a lime nitrogen with a nitrogen content
of 30.0% by weight by calcination at 750° C. (20 minutes) in a rotating tube in the absence of air
[Edited on 14-2-2016 by S.C. Wack]
|
|
Pages:
1
2 |
|