Pages:
1
2
3
4 |
metalresearcher
National Hazard
  
Posts: 758
Registered: 7-9-2010
Member Is Offline
Mood: Reactive
|
|
Steel retort design for making Na metal for review
I want to make Na metal chemically, because it seesm a lot easier than with the usal electrolysis of NaOH (which dissolves the Na metal) or NaCl/CaCl2
mixture which requires separation of the anode and cathode sections .
The reaction is :
Na2CO3 + 2C --> 2Na + 3CO
This reaction is favorable @ 1100oC and was still used commercially in the late 19th century.
Now I want to make a steel tube retort to run this reaction. Small samples in a test tube (the latter did not survive, melted like plastic) did
release Na vapor due to the bright yellow sparks escaping from the reactants.
I already made a steel pot (made from a steel tube which bottom is squeezedin a vise and then welded together) with a 3/4 steel tube screwing cap but
I'll make a steel tube to capture the vapor and collect it under mineral oil. I pot the end of the tube not too far under the oil level to prevent the
oil coming in the retort when pressure lowers due to e.g. the flame moves a bit away.
I'll put the retort in a propane furnace heated to 1200oC
Of course I'll take safety precautions: do it outdoors , wear a face mask and gloves.
Does anyone have suggestions ?
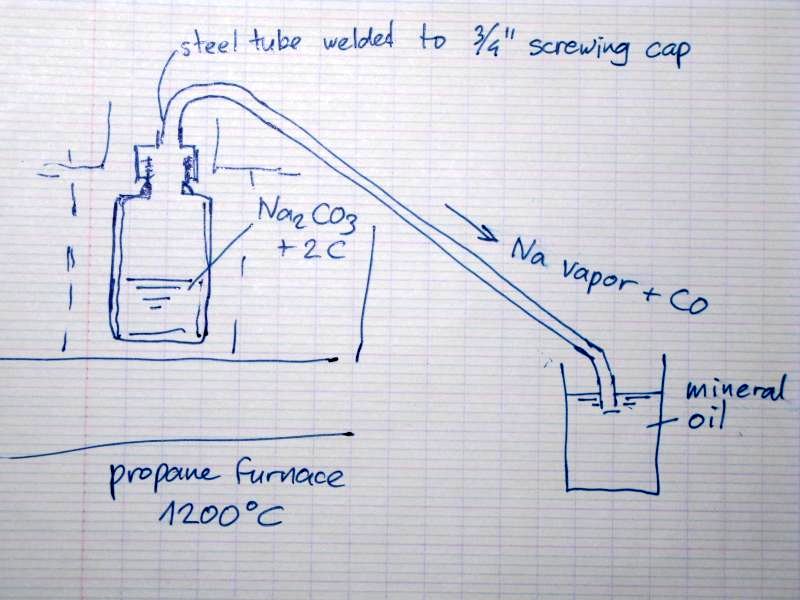
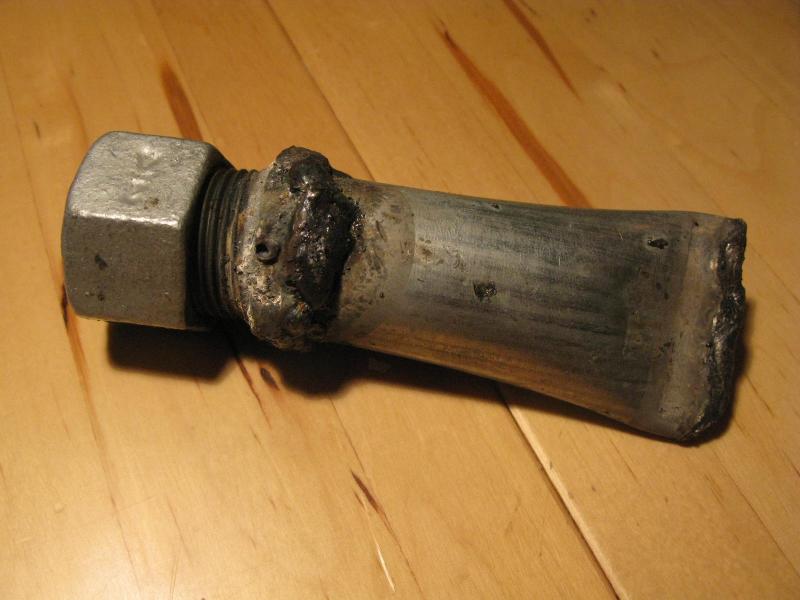
[Edited on 2010-9-15 by metalresearcher]
|
|
Globey
Hazard to Others
 
Posts: 183
Registered: 9-2-2009
Member Is Offline
Mood: No Mood
|
|
I bet if someone comes up with miniaturized versions of Down's Cell/Castner Cell, ammonia plant, liquid air plant,, P plant, etc. all very small, and
producing gram quantities (instead of tons), and simply plug into 110 or 220. That person will make a killing off sales. These are toys the rich
would LOVE to have, and would EASILY spend thousands of dollars on. The Germans spend thousands on vocoders, why not this?
|
|
Magpie
lab constructor
   
Posts: 5939
Registered: 1-11-2003
Location: USA
Member Is Offline
Mood: Chemistry: the subtle science.
|
|
I have no comments on the concept, and am eargerly awaiting your results.
My only comments are only on the possibility of making the fabrication a little easier for you in the future:
1. Use a pipe nipple (short pipe piece, threaded both ends) as body.
2. Seal one end of the body with a threaded cap; backweld.
3. Use a threaded reducer at the top; backweld to the body.
4. Thread the bent vapor/condenser pipe into the reducer at the top; Backweld to the reducer.
These plumbing fittings should be available in black iron (steel), normally used for natural gas piping I think.
Edit: The backwelding may be optional. If so, omitting it would make the retort reuseable.
[Edited on 15-9-2010 by Magpie]
[Edited on 15-9-2010 by Magpie]
[Edited on 15-9-2010 by Magpie]
The single most important condition for a successful synthesis is good mixing - Nicodem
|
|
spong
Hazard to Others
 
Posts: 128
Registered: 28-5-2009
Location: Chatham
Member Is Offline
Mood: No Mood
|
|
Are you going to heat the thin tube or will the CO being released keep it hot enough?
Also, if you're having trouble finding thin steel tube, steel brake lines should work well and come in a few different diameters, you might also be
able to get a fitting that would go straight from the brake line to something like 1/4" threads, I suppose that wouldn't be all that useful to you
though as you can just weld it.
|
|
metalresearcher
National Hazard
  
Posts: 758
Registered: 7-9-2010
Member Is Offline
Mood: Reactive
|
|
I'll use 1/2" central heating pipe which is made of galvanized steel. I'll weld a steel 1/2" threaded cap (which I will open by drill a holein it) and
then screw it onto a 3/4" -> 1/2" reducer.
The pipe will be bended to point it 45 deg downward.
|
|
bbartlog
International Hazard
   
Posts: 1139
Registered: 27-8-2009
Location: Unmoored in time
Member Is Offline
Mood: No Mood
|
|
In my opinion your proposed operating temperature is (still) too close to the melting point of your vessel. Even if you start with an iron alloy
(something low carbon) that will in principle not melt at 1200C, and you have good enough temperature control and even heating so that no part melts,
the extra carbon (CO) in your system will gradually carburize the steel and lower its melting point as more carbon enters the mix. I don't know what a
good vessel material would be (nickel? graphite?) but I don't know that ordinary steel will cut it. On the plus side, your design allows for easy
replacement of the reaction vessel if it turns out that steel will work for a small number of runs...
(addendum)
I also see that part of your design involves a galvanized pipe. I don't know what sort of thermal gradient there will be here but if you are lucky the
zinc coating will only melt; if you are unlucky it will vaporize (which is hazardous to your health). Don't use galvanized parts near the hot part of
your setup. More generally, if you're going to construct apparatus that runs at white heat you really need to familiarize yourself with the thermal
limits of different materials.
[Edited on 16-9-2010 by bbartlog]
|
|
Wizzard
Hazard to Others
 
Posts: 337
Registered: 22-3-2010
Member Is Offline
Mood: No Mood
|
|
It would be far easier to have the output end in a cooled copper vessel, cooled well below freezing, so that all gaseous sodium would collect and
solidify, and positive pressure from the carbon monoxide would flow out slowly, through say, a pinhole or regulated valve of some sort.
Also, this would allow you to heat the vessel and collect the sodium in a puddle, with the vessel sealed (of course).
Line your steel melting vessel with a high-temp ceramic crucible.
|
|
Magpie
lab constructor
   
Posts: 5939
Registered: 1-11-2003
Location: USA
Member Is Offline
Mood: Chemistry: the subtle science.
|
|
I am thinking that the body-to-reducer connection should be threaded and not backwelded so that the assembly is cleanable after use and hence
reuseable.
Keep the bent pipe at a small enough diameter and length to accomplish the following:
1. Large enough diameter that there is no risk of plugging.
2. Small enough to prevent excessive heat loss via the pipe.
3. Stays warm enough that the sodium remains a liquid and flows nicely into the receiving oil bath (Na mp = 98C; bp=883C).
I agree that galvanized steel should not be used. Especially when it is so easy to get black iron (at least for me it is).
The single most important condition for a successful synthesis is good mixing - Nicodem
|
|
Eclectic
National Hazard
  
Posts: 899
Registered: 14-11-2004
Member Is Offline
Mood: Obsessive
|
|
2 inch black iron pipe fittings should be cheap enough, and of a scale that the effort might be worthwhile?
There is some stuff on thermocarbic production of potassium in Mussprat (see the SM Library)
|
|
NERV
Hazard to Others
 
Posts: 152
Registered: 22-9-2002
Location: USA
Member Is Offline
Mood: Fluorinated
|
|
Awesome its nice to see another person who is on the side of non-electrochemical alkali metal production . After a long hiatus from home experimentation I have started a new project similar to yours. My aim though is the
production of potassium utilizing the KOH & Mg termite. The method was derived from the discussion's in unconventional sodium. Since KOH & Mg turnings are readily available to me this method is unmatched.
The reaction proceeds as follows:
KOH+Mg--->MgO+K+.5H
The reaction is very fast (almost explosive for NaOH) and it is initiated at a relatively low temperature. The nice thing about it is it can be
applied to a variety of alkali metals including Cesium. In the system I have designed I will purge the inner chamber through a ball valve with argon
before igniting the mixture. After the mix has reacted fully I will continue to heat the retort until its about 759°C when the potassium will
volatilize into the copper pipe and condense. The condenser will be kept at a temp of about 65-70°C via a recirculating heater keeping the K liquid
and allowing it to collect in the mineral oil catch pan.
Conveniently this reaction is well bellow the melting point of my reaction vessel. I do however intend to plate the inside of my steel pipe with
nickel to help reduce the corrosive effects of the hydroxide on the iron.
And now for the best part photos :
Vir sapit qui pauca loquitur.
|
|
Eclectic
National Hazard
  
Posts: 899
Registered: 14-11-2004
Member Is Offline
Mood: Obsessive
|
|
I was curious about stability of copper to K or Na, but it looks like it may be OK....you can get stainless tubing at plumbing supply in 20 foot
lengths, reasonable price. Or steel brake line.
http://resources.metapress.com/pdf-preview.axd?code=p27u1k11...
K2CO3 and Mg might be more manageable?
[Edited on 9-16-2010 by Eclectic]
|
|
NERV
Hazard to Others
 
Posts: 152
Registered: 22-9-2002
Location: USA
Member Is Offline
Mood: Fluorinated
|
|
It probably would be, but K2CO3 is not nearly as available to me as KOH. And the reaction isn't that bad with potassium its fast but not really
explosively according to the thread i mention above so I'm not to worried. I'd only be concerned if I needed Na, but lucky for me I have enough of
that to last me for a long time .
Vir sapit qui pauca loquitur.
|
|
Panache
International Hazard
   
Posts: 1290
Registered: 18-10-2007
Member Is Offline
Mood: Instead of being my deliverance, she had a resemblance to a Kat named Frankenstein
|
|
so why not make the reaction vessel from stainless? Am i missing something?, in fact the entire thing could be stainless.
|
|
NERV
Hazard to Others
 
Posts: 152
Registered: 22-9-2002
Location: USA
Member Is Offline
Mood: Fluorinated
|
|
Well for one thing black steel is a lot cheaper than stainless, and plating it with Ni took me only about an hour.
Vir sapit qui pauca loquitur.
|
|
metalresearcher
National Hazard
  
Posts: 758
Registered: 7-9-2010
Member Is Offline
Mood: Reactive
|
|
FIRST TRY ... FAILED :-(
I just did my first attempt but despite heating the (small)vesselto 1100oC I saw no sodium in the oil.
In the meantime I bought steel tubing + caps like @NREV did. I think the vessel as I used it now was not completely sealed as Isaw bright yello flames
(see in the video) in the furnace and a little white smoke (Na2O ?) appeared.
I think that the threaded parts are hard to seal .
Other ideas like stainless steel retort do not make much sense as SS is as weak as 'ordinary' steel and oxidizes as easily. The only real solution is
using Ir, Re or W as vessel material but these metals cost thousands of $$$ per kilo. And graphite crucibles (which I have) can be a solution too but
... how to seal ???
I bet the facilities producing Na metal commercially by this process at the end of the 19th century used black steel as well.
Here a video of which I did this evening:
http://www.youtube.com/watch?v=fNJgH52Ff1s
UPDATE:
I was unable to unscrew the bend + tube from th vessel. So the only option was the .... angle grinder .
And here a closeup of the open cut vessel:
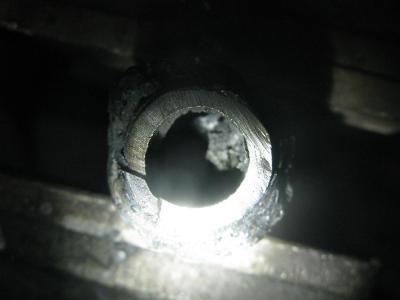
[Edited on 2010-9-17 by metalresearcher]
|
|
peach
Bon Vivant
   
Posts: 1428
Registered: 14-11-2008
Member Is Offline
Mood: No Mood
|
|
Awwww shit.... and my 70amp 12vdc adjustable power supply turned up this morning as well. 
A young guy into HAM radio donated it to the cause (science), on my birthday too! 
There is a lot of stainless used for kitchenware / household items that is simply stamped, where precise wall tolerances, stress lines, welds and all
the rest aren't an issue.
Maybe you could find something suitable digging around the local cheapo stores (e.g. I have a stainless steel toothbrush holder, a cup like thing,
that cost next to nothing). Then nickel plate it for super duper corrosion resistance.
I'm not sure how you're going to oxidize the stainless with a reducing atmosphere inside it (unless you mean the outside).
Also, check the temperature on that spout coming out of the heating pot, you'll want the entire thing above the melting point of sodium. You'll
probably also want to purge the pots with an inert gas prior to starting.
Bartlog is also correct about the temperature. People go on about "but jet fuel doesn't burn hot enough to melt steel". It doesn't need to melt it
when there's thousands of tons of building sat on top of it. Anyone who's held a long, long rod of steel knows it's like spaghetti even when it's
cold. The steel will loose a gigantic amount of strength once it goes over something like 700 - 800C, from memory. If the 'jet fuel not hot enough'
stuff was worth a single grain of salt, boeing would be making engines out of wrought iron. They actually make them out of monocrystalline titanium
and other super alloys, and stainless. There's probably some reasoning behind that.
You should check out the videos for how they do the turbine and fan blades. Unbelievable stuff. The fan blades are actually hollow, and cost about
£20 -30k or something, EACH.
As for vocoders, any tune that involves a vocoder is going to be a guaranteed hit with me.
"Just on the border of your waking mind
There lies... Another time
Where darkness & light are one
And as you tread the halls of sanity
You feel so glad to be
Unable to go beyond"
John <----- WHERE ARE THE REST OF MY PRESENT GUYS!?
Left to right, a coffee filter, cocktail shaker (stirred will do), kitchen storage thingy (spices / sugar / flour), cups, 100% stainless thermos

I particularly like the drinks shaker and the storage thing. Both have friction fit lids and the walls are ready for heating (the shaker LOOKS like a
crucible). They can all be found for very little money (the thermos was about £5 or something).

[Edited on 17-9-2010 by peach]
|
|
metalresearcher
National Hazard
  
Posts: 758
Registered: 7-9-2010
Member Is Offline
Mood: Reactive
|
|
Nise stainless stuff, but these are so thin (< 0.5mm) when heated to 1200oC they will be damaged easily, particularly when molten alkali (yes:
Na2CO3 is an alkali !) is in it.
But of course SS is better when it has the same thickness as the iron tubing parts.
Up to the next Na making attempt !
|
|
peach
Bon Vivant
   
Posts: 1428
Registered: 14-11-2008
Member Is Offline
Mood: No Mood
|
|
I bet one of these Chinese guys can get lids for graphite crucibles
Or someone on Alibaba
Riogrande also sell bottom gaskets for their investment casting crucibles that would work as a lid if you bought one bigger than the crucible and
either pressed it on with weight somehow or had someone cut a groove into it with a lathe. You could probably cut the groove with a hand drill if you
stuck a disc sanding disc backing pad in it and then the gasket to that.
|
|
Eclectic
National Hazard
  
Posts: 899
Registered: 14-11-2004
Member Is Offline
Mood: Obsessive
|
|
http://shop.ebay.com/?_from=R40&_trksid=p3907.m570.l1313...
|
|
peach
Bon Vivant
   
Posts: 1428
Registered: 14-11-2008
Member Is Offline
Mood: No Mood
|
|
I was sure I saw one of the crucible companies in the UK doing lids at some point, Morgan (Salamander), but I can't see them on there now. If you're
Europe / UK side, you could give them a ring.
The guys who do investment casting of jewellery and dental fixings are likely candidates I suspect, they usually have nice crucibles, but not the "How
much did you say again?" end of nice.
{Edit}Are you in the UK? I thought DeWalt had made Bosch illegal in the US My
last Bosch grinder actually died, early. And when I opened it up, I discovered it was 100% unserviceable, an odd thing for a German brand. I switched
to a mondo 3hp DeWalt, that gets things moving alright. But the trigger switch also jams in the ON position when grit blows into it. 3HP, a few
thousand RPM, mit blade and jammed ON. Hmm....
[Edited on 18-9-2010 by peach]
|
|
Formatik
National Hazard
  
Posts: 927
Registered: 25-3-2008
Member Is Offline
Mood: equilibrium
|
|
Well according to Gmelin, the thing about using Na2CO3 together with C is that it reduces only at white glow (which is something like 1500 C), though
NaOH and C can be reacted at red glow, the reaction being: 4 NaOH + 2 C = Na2CO3 + 2 Na + 2 H2 + CO. I know molten NaOH at low red heat very strongly
attacked a stainless steel bottle, in fact it ruined it. Maybe having a small bed of carbon or charcoal below and surrounding the reaction mixture
could buffer some of this corrosive nature, by causing the NaOH to absorb.
Concerning some other mixtures: one reference notes reduction of Mg with Na2CO3 causes such a vigorous deflagration, so that this mixture is not even
useful for the preparation of sodium (Cl. Winkler, Ber. 23 [1890] 46). But, heating Na2CO3 with aluminium powder also forms sodium, except here the
reaction is said to occur very peacefully (L. Franck, Bl. Soc. Chim. [3] 11 [1894] 439). Some salts can cause a very dangerous reductions, like Na2SO4
as noted here.
Also, in the thermal preparation of potassium involving carbon and carbon compounds, hot potassium vapor can react with the CO gas to form a highly
explosive compound (potassium hexahydroxybenzene, a.k.a. potassium benzenehexoxide or potassium carbonyl, milder conditions gets dipotassium
ethynediolate). This explosion risk is also noted in the literature. I'm not sure of a similar hazard for sodium, that might be something to look
into. Maybe not, since I haven't seen this mentioned anywhere. And the Encyclopaedia Britannica states: "Potassium reacts with carbon
monoxide at temperatures as low as 60°C to form an explosive carbonyl (K6C6O6), a derivative of hexahydroxybenzene. Sodium is essentially nonreactive
with carbon monoxide." Then Handwörten der Chemie by A. Ladenburg mentions that indeed no explosive compound is formed with sodium as
opposed to potassium, so it does not unite with carbon monoxide.
I also noticed your apparatus does nothing to address suckback. Heating a mixture this high and reacting, could cause quite a suckback (NERV's
schematic above does address suckback, flushing with inert gas).
Alternative to inert gas flush, maybe one could use the same kind of shut-off valve seen in NERV's picture, if you fix this as being part of the
apparatus tubing that leads the metal away. Then closely monitoring the mineral oil level and as soon as a slight amount is sucked up (if it happens
so graciously) the shut off valve is turned to close. Care would probably need to be taken so that oil is not sucked in and then it is closed, but
that it is closed quickly before any can even enter the reaction vessel.
Quote: Originally posted by NERV  | Since KOH & Mg turnings are readily available to me this method is unmatched.
The reaction proceeds as follows:
KOH+Mg--->MgO+K+.5H |
This interaction between KOH and Mg is also described in Z. physik. chem. Unterricht 5 [1892], 146-152. This reference states the liberated hydrogen
completely promotes the distillation of the potassium out of the mixture. They also say the reaction goes most peacefully by heating a mixture of the
following until the beginning of glowing heat: 7 parts KOH, 3 parts Mg and 7 parts MgO in a glass or iron tube with a gas tube having a diameter of
15mm. I wouldn't use glass though for obvious reasons.
K2CO3 and Mg was less energetic than either Li2CO3 or Na2CO3, in a H2 stream all of the potassium can be completely distilled off, they noted some of
that naughty compound formed in small amounts, especially the less Mg in the mixture there was, and in colder parts of the tubes CO and K unified to
the same hazardous compound.
Attachment: Z.physik.chem.Unterricht 5 [1892],147.pdf (72kB) This file has been downloaded 678 times
[Edited on 19-9-2010 by Formatik]
|
|
Eclectic
National Hazard
  
Posts: 899
Registered: 14-11-2004
Member Is Offline
Mood: Obsessive
|
|
http://www.youtube.com/watch?v=908rjHQ5mmc&feature=relat...
I'd go with Magnalum if it works, as it's easy to pulverise.
|
|
metalresearcher
National Hazard
  
Posts: 758
Registered: 7-9-2010
Member Is Offline
Mood: Reactive
|
|
@Formatik
The reaction *is* favorble @1100oC according to this site : fill in 1 mol Na2CO3 and 2 moles C and this was used commercially in the 19th century before that electrolysis of liquid NaOH or NaCl
was more feasible.
I did address the suckback issue as I keep the level of the ducking tube less than 1cm below the oil level so when the retort sucks back it drags only
the oil above this level and that is not enough to fill the entire tube to get into the hot vessel.
I just did my second attempt by using a sealed steel container (see the photo in my first post on top of in this topic) now I heated it more by using
forces draft propane and within five minutes it got yellow hot which required dark goggles to see anything rather than yellow void which means as much
the temperature is 1200-1300oC way enough to start the reaction. But what also happened is that I saw again bright yellow flames from the bottom of
the vessel and then fumes escaping which required to wear a mouth mask as these fumes are probably Na2O.
When it did not react, no fumes can escape because Na2CO3 vaporizes at white heat @ 1600oC according to http://en.wikipedia.org/wiki/Na2CO3 .
The bubbling in the oil bath stopped as well which means that venting took place from the vessel itself
Then I stopped the furnace and opened the furnace lid and took out the retort and saw this:
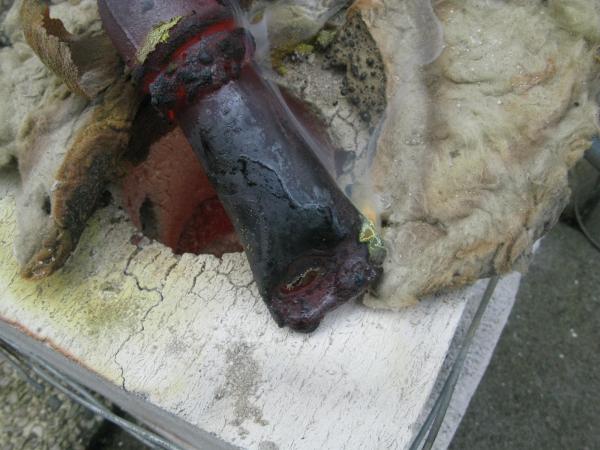
and a more detailed view:
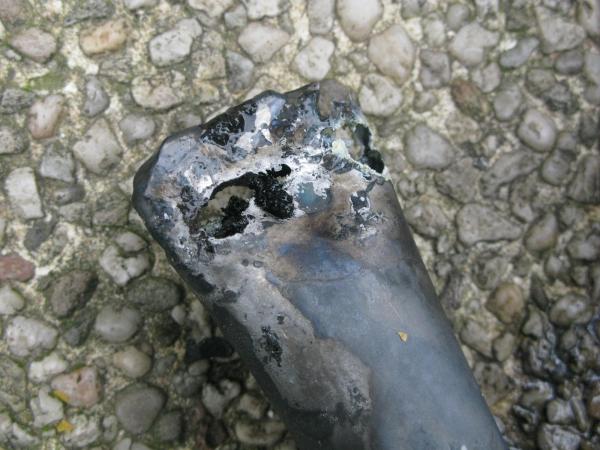
which tells that the steel is probably chemically attacked by the liquid Na2CO3.
It was not hot enough to melt (which occurs @ 1500oC).
Next time: graphite crucibles glued together with stove kit ???
Or iridium / rhenium ???
[Edited on 2010-9-19 by metalresearcher]
|
|
Formatik
National Hazard
  
Posts: 927
Registered: 25-3-2008
Member Is Offline
Mood: equilibrium
|
|
Quote: Originally posted by metalresearcher  | @Formatik
The reaction *is* favorble @1100oC according to this site : fill in 1 mol Na2CO3 and 2 moles C and this was used commercially in the 19th century before that electrolysis of liquid NaOH or NaCl
was more feasible. |
I take the literature's description over that site. They have been there and done the reaction. There are several other references also saying white
heat. Enter "sodium carbonate white heat sodium metal" into google books to see some. It will not work.
Wiki does also mention the same temperature. I don't trust wiki, but do trust the cited Kirk Othmer. Though this is in conflict with quite a few
references. Kirk Othmer is said to cite Deville. The Ausfuehrliches Lehrbuch der pharmazeutischen Chemie by E.A. Schmidt mentions St. Claire
Deville distilled an intimate mixture of Na2CO3 (30 parts), CaCO3 (5 parts) added to facilitate reaction, and 13 parts charcoal distilled in wrought
iron retorts at white glowing heat. The lowest temperature ranges I've seen for white glow is 1300 C to 1400 C. Though the original Deville references
(could all be in French) would provide clearer details.
Though my point at mentioning it was it would be easier to use aluminium mixture with Na2CO3 (which also won't need as much heat) or the NaOH. NaOH
will be a bit harder though, since Na2CO3 forms which needs the white heat to reduce. In the process itself, Na2CO3 was drawn off to avoid the higher
temperatures.
Another mixture which needs higher heat than those (but not white heat): sodium borate (Na2B4O7.10 H2O) heated together with coke powder dehydrated at
600 C in a retort, this then gets heated to 1150 C where Na distills over; if the temperature rises to 1300 C, B2O3 also distills over. Heating the
residue to 1600 C yields elemental B (Peacock, Waldo, AP1493126 [1921]).
[Edited on 19-9-2010 by Formatik]
|
|
Rogeryermaw
National Hazard
  
Posts: 656
Registered: 18-8-2010
Member Is Offline
Mood: No Mood
|
|
check out the last few pages of the phosphorus thread. i built a reactor and furnace much like these that may suit your needs. worked great for
producing P4! the furnace is run on wood but that's variable. just change the water in the catch pan to mineral oil and away you go. if your having
trouble sealing threads, use teflon tape. yes it will melt but it won't run out of the threads and it will maintain it's seal. if your reactor
survives the process, you can just scrape it of and reapply.
[Edited on 21-9-2010 by Rogeryermaw]
|
|
Pages:
1
2
3
4 |