Pages:
1
..
22
23
24
25
26
..
47 |
dann2
International Hazard
   
Posts: 1523
Registered: 31-1-2007
Member Is Offline
Mood: No Mood
|
|
Hello,
The puzzle has been solved. The 'solution' was posted here many moons ago. I /we are trying to do the same thing with more OTC materials. It ain't
working for me I guess.
See here for working homemade Ti substrate, DTO + Lead Dioxide anode.
http://www.sciencemadness.org/talk/viewthread.php?tid=1425&a...
from a guy who actually made lots of anodes.
More discussion of anode here:
http://www.sciencemadness.org/talk/viewthread.php?tid=2465&a...
He use Butter of Tin and Butter of Antimony + water + Buthanol.
Dann2
|
|
Rosco Bodine
Banned
Posts: 6370
Registered: 29-9-2004
Member Is Offline
Mood: analytical
|
|
If the SnCl4 plus SbCl3 was so straightforward as to be the simple solution , then you wouldn't be having huge problems with it , would you ?
Alembic wasn't very forthcoming with the particulars concerning the intermediate layer ...was he ?
The problem of volatility has been mentioned with regards to the chlorides precursor mixture .
There is a gap in the temperature range where there is an indeterminate variable loss of the chlorides precursor mixture
due to volatility .....before the decomposition to the non-volatile oxides takes place ....at a higher temperature .
This alone is a problem I have pointed out before , which
makes the rate of heating affect the composition of the
residue of oxides , as well as how much of that residue is
even there .
Attached is a patent which uses a vapor deposition method
for metal oxide applied to a ceramic substrate to produce
resistors as an electronic component . The mixed chlorides
precursor is used , not as a liquid applied to a substrate and baked .....but as an aerosol vapor contacted with the substrate already raised to the
much higher pyrolysis temperature where the vapors of the mixed chlorides on contacting the much hotter surface , then deposit the desired
oxides as a decomposition product . What makes this vapor deposition process work is precisely what presents a problem
when the mixed chlorides precursor is applied to a cool surface and then gradually heated ....most of it simply evaporates and leaves on the wind ,
literally gone with the wind .....get it ?
[Edited on 31-7-2007 by Rosco Bodine]
Attachment: US3632429 Sb2O3 SnO2 METAL_OXIDE_FILM_Resistors.pdf (196kB) This file has been downloaded 860 times
|
|
Twospoons
International Hazard
   
Posts: 1327
Registered: 26-7-2004
Location: Middle Earth
Member Is Offline
Mood: A trace of hope...
|
|
@Hashashan
Here's the controller I built for a hotplate:
http://www.sciencemadness.org/talk/viewthread.php?tid=4896&page=1#pid55520
Works well, holds within a degree or so, and is very simple.
Helicopter: "helico" -> spiral, "pter" -> with wings
|
|
Rosco Bodine
Banned
Posts: 6370
Registered: 29-9-2004
Member Is Offline
Mood: analytical
|
|
Why mixed valence oxide precursors may be useful
Stable colloidal dispersions of mixed antimony and tin oxides
are known , where a colloidal dispersion of antimony oxide is *intimately* mixed by *coprecipitation* with a colloidal dispersion of tin oxide , so
that doping is already accomplished at a relatively low temperature for
a dispersion that is a transparent emulsion ....a sol .
Antimony doped tin oxide nano *crystals*of X-ray diffraction
identified character showing only the tin oxide crystal structure , fully enclosing and masking the antimony within the tin oxide crystal structure
are formed from such mixed colloidal dispersions , even at temperatures as low as 200C
in water dispersions heated for 6 hours in an autoclave .....
where the reaction goes entirely to completion . The nature
of the material is a solid solution of antimony entirely caged within the tin oxide crystal matrix . See US4775412 . Compare the coprecipitation of
the Sn and Sb which is performed and *required* in the process with the similar process and material produced by US6777477 . These materials are
probably identical as precursors .....or close enough , and the method of the later patent is simpler .
As a side note of possible interest .....
For colloidal sols of antimony oxide alone see US5008036 .
This patent also references other patent methods for
antimony ethyl glycolate .
For our purposes of producing an amorphous film structure
as opposed to a layer of solid solution nano crystals ...it appears that a variation on the mixed colloidal precursors could be useful , involving the
mixed valency precursors which have a long chain polymeric form and dehydrate intact in that form , rather than precipitating as solid solution nano
crystals . A desirable physical property of such a dispersed polymer is that it has profound effect as a wetting agent and
also has a strong electrostatic attraction to a surface to which it is applied , attaching itself as a persistent coating .
This is reported specifically for SiO2 , but the similar property
likely also applies to TiO2 . The effect is so pronounced that
even teflon is readily wetted by the inorganic polymer and the effect of wetability is persistent , for this material which
remains as a permanent surface layer adhering to the teflon .
Since the dispersion distribution of particles would be so complete already in the "doped colloid" , which would dehydrate as the polymer rather than
a solid solution crystalline form .....during drying and baking , and the electrostatic property is so favorable for adhesion to a substrate , this
would seem to be an ideal candidate for an initial coating .
BTW , this polymer is very possibly involved in the oxidative soak method for deposition of SnO2 . In that deposition method a +II valency Sn(OH)O?
is being gradually oxidized to
a less soluble +IV SnO2 which is precipitated ....but it would seem that the mixed valency polymer would necessarily be present in that reaction
system . And this may be what accounts for the reported strong adhesion of the deposited
films of SnO2 gotten by the oxidative soak method .
[Edited on 1-8-2007 by Rosco Bodine]
Attachment: US3890429 STANNIC_OXIDE_POLYMER_Film Wetting Agent.pdf (399kB) This file has been downloaded 1132 times
|
|
Rosco Bodine
Banned
Posts: 6370
Registered: 29-9-2004
Member Is Offline
Mood: analytical
|
|
more specifics concerning oxidation of titanium
From a couple of pages earlier in this thread ....
Quote: | Originally posted by dann2
From www.azom.com
____________________________________________
Oxide Film Growth
The oxide film formed on titanium at room temperature immediately after a clean surface is exposed to air is 12-16 Angstroms thick. After 70 days it
is about 50 Angstroms. It continues to grow slowly reaching a thickness of 80-90 Angstroms in 545 days and 250 Angstroms in four years.
The film growth is accelerated under strongly oxidizing conditions, such as heating in air, anodic polarization in an electrolyte or exposure to
oxidizing agents such as HNO3, CrO3 etc. The composition of this film varies from TiO2 at the surface to Ti2O3, to TiO at the metal interface.
Oxidizing conditions promote the formation of TiO2 so that in such environments the film is primarily TiO2. This film is transparent in its normal
thin configuration and not detectable by visual means.
A study of the corrosion resistance of titanium is basically a study of the properties of the oxide film. The oxide film on titanium is very stable
and is only attacked by a few substances, most notably, hydrofluoric acid. Titanium is capable of healing this film almost instantly in any
environment where a trace of moisture or oxygen is present because of its strong affinity for oxygen. Anhydrous conditions in the absence of a source
of oxygen should be avoided since the protective film may not be regenerated if damaged.
__________________________________________
Dann2 |
To provide a more detailed look at the pH and electrical parameters which define the reactivity of titanium , these Pourbaix Diagrams are helpful .
This data is useful in predicting what conditions may be helpful not only in plating schemes for titanium , but also in preparation of and coating
and doping schemes for titanium .
The first diagram is generalized and does not account for higher concentrations of dissolved hydrogen , for which titanium exhibits a very strong
adsorption . The second diagram accounts for and shows the effects of the hydrogen .
These diagrams are important so I have saved them locally on the forum server .
Pourbaix diagrams for titanium below were found here
http://www.engr.sjsu.edu/WofMatE/projects/srproject/srproj5....

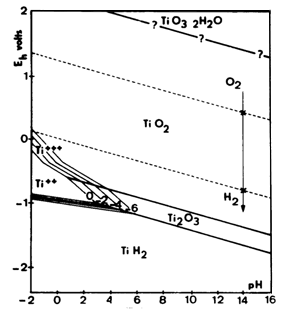
There are cathodic etching / hydriding schemes which are applicable to plating and also preparation for other coatings for titanium and other metals .
It is possible to do this in a plating bath by first applying a low cathodic voltage to etch and hydride the metal , and then increasing the voltage
to quickly deposit the metal plating so that a good metal to metal interface is produced .
Patents of possible interest concerning this technique are
US5368719 , US5456819 , US2801213 , US4153742 .
I posted this in response to electroplating of iron on titanium
in another thread , but this is also highly relevant here .
[Edited on 9-8-2007 by Rosco Bodine]
|
|
Rosco Bodine
Banned
Posts: 6370
Registered: 29-9-2004
Member Is Offline
Mood: analytical
|
|
Oxalic acid related
There is a patent US3650861 which directly relates to the usefulness of oxalic acid for etching titanium in a controlled way which improves the
adhesion of coatings or platings as compared with other methods .
Also it reportedly is possible to use the mixed oxalates of tin and antimony as non-volatile precursors for baked ATO coatings of high quality on a
titanium substrate , by a simple
dip , dry , and bake method . See US5431798 attached .
Eclectic has mentioned the possible usefulness of an initial
plating of metallic tin directly on the etched metallic titanium substrate , and this is described in the attached patent .
However ...there may be easier or better ways of obtaining
such an initial plating , as the oxalate of tin will itself plate
out tin at an appropriate pH , if the substrate is made cathodic . There are patents which relate specifically to plating of tin from tin oxalate
electrolytes .....and I will have to dig them up to see if there is an example for the conditions for titanium . It may be possible to perform the
titanium etching , tin strike plating , and dip coating for baking ATO , all in one pot using an oxalate / oxalic acid system . Anyway , for an example of the plating of tin
from an oxalate bath .....there is a brief description of this
tin plating in a rectifier patent US2368749 , see last page .
Also a variant of these mixed oxalates reportedly produces transparent optical quality coatings . No examples are given for titanium substrates in
these further patents , but the chemistry is described in some detail and the conductivity
of various levels of antimony doping in the finished oxides is charted .....the ~5% figure for antimony oxide agrees nicely with most other sources
which report an antimony percentage range from a minimum of 2% to a maximum of 8% , IIRC . See US4873352 and US4924017 .
Edit :
I just found a later version of the same patent attached below , apparently a parallel application , same inventors , same company , same subject
material ... US5683567 .
[Edited on 17-8-2007 by Rosco Bodine]
Attachment: US5431798 Oxalate Precursors for ATO coated Ti substrate anodes.pdf (130kB) This file has been downloaded 931 times
|
|
hashashan
Hazard to Others
 
Posts: 255
Registered: 10-10-2006
Member Is Offline
Mood: No Mood
|
|
Say guys, I think i will be able to lay my hands on a nice pice of Ta + Nb foil (surprizingly it will be easier to get then Ti ) Do you think that a
protective DTO layer should be applied on this substrate also? or the Ta wont get oxidized form the PbO2 layer?
|
|
Eclectic
National Hazard
  
Posts: 899
Registered: 14-11-2004
Member Is Offline
Mood: Obsessive
|
|
Absolutely, if you can get it to work. Ta oxide is even better at insulating than TiO2. I don't think it's going to work without some fluoride in
the mix.
|
|
hashashan
Hazard to Others
 
Posts: 255
Registered: 10-10-2006
Member Is Offline
Mood: No Mood
|
|
Oh never mind, somone outbidded me on ebay. I guess ill find some Ti there.
maybe somone here care to sell some Ti?
|
|
dann2
International Hazard
   
Posts: 1523
Registered: 31-1-2007
Member Is Offline
Mood: No Mood
|
|
Tin Oxalate, where/how to obtain?????
Hello Folks,
Been doing some Patent digging Rosco eh?
The Pat. using the Tin Oxalate is good since it uses a new Tin compound for me/us in the examples, ie. Tin Oxalate.
The obvious question that I am going to ask is, where/how can one get Tin Oxalate?
Tin metal + Oxalic acid is my wild assed guess but quite frankly I don't have a clue.
I am looking at a piece of Ti, on the bench, that I coated with DTO about 4/5 weeks ago. The coating seems to be getting more and more shiney as the
days go by. (The part of the coating at anode top end not etched away when I 'tested' it some weeks ago). I will try putting it into a Chloride
solution as an anode and see what happens. This piece of DTO coated Ti has been tested before in a Chloride electrolyte and it lasted some minutes
when it had sat on the bence for about 2 weeks after it was coated. (Simiarly coated Ti had only lasted about one minute when tested just after
coating).
Perhaps the coating gets better when aged for a few weeks?? ...................Like Whiskey.
We shall see.
Dann2
|
|
Rosco Bodine
Banned
Posts: 6370
Registered: 29-9-2004
Member Is Offline
Mood: analytical
|
|
Quote: | Originally posted by dann2
Hello Folks,
Been doing some Patent digging Rosco eh? |
Yeah you know me ...I occasionally look at a patent or two
trying to find anything interesting 
Quote: |
The Pat. using the Tin Oxalate is good since it uses a new Tin compound for me/us in the examples, ie. Tin Oxalate.
The obvious question that I am going to ask is, where/how can one get Tin Oxalate?
Tin metal + Oxalic acid is my wild assed guess but quite frankly I don't have a clue. |
I looked briefly for a preparation but didn't find anything other than the oxalates have a low solubility in plain water .
I thought probably either direct reaction with the metal
and a hot oxalic acid solution perhaps with added hydrogen peroxide . Boiling a solution of the chlorides with oxalic acid
may also possibly do it , with the HCl byproduct boiling away .
Or perhaps make ammonium stannate and then make the oxalate from that , although the ammonium stannate itself is probably a better precursor to use
directly .
I still think that mixed valency polymer of the approximate oxychlorides composition has the most promise , or an oxidative soak method for getting
the first layer ....but anyway there sure are a few promising alternatives to
the mixed chlorides which are presenting complications .
I have an idea for shortcutting the process if the anode substrate could be a solid titanium rod . Get a rectangular form cast iron burner from an
old radiant space heater , and
chuck the solid rod in a slow speed rotisserie drive like a
zeromax stirmotor or light duty conveyor motor , and do
the baking over an open flame with the part rotating .
You could spray coat your precursor liquids directly onto
the hot part , in several passes as a more or less continuous
process until you get the desired thickness ......instead of doing several separate manipulations . One of those Preval
sprayers like hobbyists use could do the job , or an airbrush
if you have one .
[Edited on 20-8-2007 by Rosco Bodine]
|
|
dann2
International Hazard
   
Posts: 1523
Registered: 31-1-2007
Member Is Offline
Mood: No Mood
|
|
Hello,
Done some Googling [tin oxalate] and came up with this
http://64.233.183.104/search?q=cache:2v4fAkdugnwJ:www.ias.ac.in/matersci/bmsdec2004/491.pdf+tin+oxalate&hl=en&ct=clnk&cd=5&gl=ie
You may need to cut and paste this link.
In document it describes synthesis of Tin Oxalate:
_______________________________________
2.2 Preparation of tin oxalate precursor
This precursor was prepared by dissolving equimolar quan-tities of tin chloride and oxalic acid and stirred well. The precipitate of tin oxalate
obtained was filtered through sintered glass crucible and was washed with oxygen-free distilled water till free from chloride ions and oxalic acid,
finally with dry acetone and was then dried under vacuum.
_______________________________________
Which Tin Chloride do you think it is?
Looks dead easy to me if it is Tin(II) Chloride (SnCl2)!
This link states that SnCl4 forms when Tin metal is added to Aqua Reiga:
http://www.neymetals.com/tin.htm
Oxidizing acid,,,, same as HCl then H2O2?????? I guess.
US 5116468 uses Sn/Sb metal + Oxalic acid to obtain DTO in electrolythic set up. May be applicable to us.
Cheers,
Dann2
[Edited on 24-8-2007 by dann2]
|
|
Rosco Bodine
Banned
Posts: 6370
Registered: 29-9-2004
Member Is Offline
Mood: analytical
|
|
The SnCl2 is probably what they were using and it would be the stannous oxalate precipitated . The patent however is
producing the higher oxidized stannic oxalate by anodic oxidation of the tin metal . You can get the same thing
I think , without the lengthy electrolysis .
Probably the easiest route would be to just make your clear solution of mixed chlorides with HCl + H2O2 ,
or HCl + NH4NO3 (toxic fumes!) and then neutralize with ammonia to a pH of 7 to 8 to precipitate the mixed basic hydroxides , that is the stannic and
antimonic "acids" . The precipitate will probably settle out by gravity and the waste liquid can simply be decanted , and oxalic acid solution added
and the mixture stirred and heated to form a solution of the mixed oxalates . IIRC you will need some small excess acidity of oxalic acid and
possibly also some small amount of ammonium oxalate present for increasing the solubilities of the mixed oxalates well beyond what is their usual low
solubility in plain water .
[Edited on 24-8-2007 by Rosco Bodine]
|
|
Eclectic
National Hazard
  
Posts: 899
Registered: 14-11-2004
Member Is Offline
Mood: Obsessive
|
|
Sn(II) oxalate is poorly soluble, Sn(IV) soluble. H2S bubbled through a solution of Sn(IV) and some Sn(IV) oxalate precipitates antimony sulfide, but
not tin.
(I'm still experimenting with 95/5 solder as a source of tin) 
[Edited on 8-24-2007 by Eclectic]
|
|
Rosco Bodine
Banned
Posts: 6370
Registered: 29-9-2004
Member Is Offline
Mood: analytical
|
|
IIRC there is a window concentration of diluted HNO3 ....maybe 5-35% concentration range where
the metals are dissolved by the boiling acid and the
nitrates formed are then immediately hydrolyzed with
precipitation of the oxides , or basic oxides . There is an evolution of deadly toxic oxides of nitrogen as a byproduct during the process similarly
as when lead or silver or mercury are dissolved in nitric acid .
After producing the oxides , then they could be converted to other materials by further reaction to produce the desired salt ......like the oxalate .
The implications for the electrolysis are also interesting in another way .
The use of electrolysis in regards to the oxalate
could perhaps be used in an exactly opposite arrangement from that patent , to partially reduce
the higher valency materials to a system of the mixed
valency "polymer" , or sol type of liquid system as has been described for the chlorides . The chlorides could probably be treated the same way as
an alternative electrolytic method of production of that mixed valency polymer , instead of stirring the solutions of the higher
valency salts with the powdered metals , or addition of the
lower valency salts , to form the polymer . A gentle , partial reduction in a divided cell where the higher valency
salts are the catholyte should accomplish the same thing
and the polymer of mixed valency materials should result ,
as an intermediate in reduction before the free metals are plated out .
[Edited on 24-8-2007 by Rosco Bodine]
|
|
not_important
International Hazard
   
Posts: 3873
Registered: 21-7-2006
Member Is Offline
Mood: No Mood
|
|
Quote: | Originally posted by dann2
...
In document it describes synthesis of Tin Oxalate:
_______________________________________
2.2 Preparation of tin oxalate precursor
This precursor was prepared by dissolving equimolar quan-tities of tin chloride and oxalic acid and stirred well. The precipitate of tin oxalate
obtained was filtered through sintered glass crucible and was washed with oxygen-free distilled water till free from chloride ions and oxalic acid,
finally with dry acetone and was then dried under vacuum.
_______________________________________
Which Tin Chloride do you think it is?
|
It's Sn(II), note the use of oxygen-free water for washing.
Quote: |
...
Oxidizing acid,,,, same as HCl then H2O2?????? I guess.
|
Note that H2O2 contains stablisers, which might affect the product and the end use, given that you are working towards semiconductive materials that
often are sensitive to small amounts of other ions.
|
|
Eclectic
National Hazard
  
Posts: 899
Registered: 14-11-2004
Member Is Offline
Mood: Obsessive
|
|
H2O2 stabilizers are usually in PPM and are generally either tin compounds or phosphoric acid. From my experiments with various lead free solders,
I'd say dissolving 1 lb (500g) lead free solder with about 1 quart (liter) 10-12N HCl in a ceramic crock pot @ 90C for 12-24 hours is cheap and easy
route to obtain fairly high purity SnCl2. The intermetallics from the alloying elements don't seem to want to dissolve unless the oxidation state is
raised with H2O2 and additional HCl. Dropwize addition of 1 part 30% H2O2 to 2-3 parts 10-12N HCl (foaming hazard if acid contains Fe) with vigorous
stirring to the COLD (much heat produced) SnCl2 solution will convert it to SnCl4. Excess H2O2 produces a white precipitate.
Concentrated SnCl4 solution WILL dissolve tin and tin intermetallics.
|
|
hashashan
Hazard to Others
 
Posts: 255
Registered: 10-10-2006
Member Is Offline
Mood: No Mood
|
|
Sorry for reviving a dying thread,
Anyone knows any way to make an alpha lead dioxide coating? I don't want to electrolyze lead in H2SO4 because i need this alpha layer to be plated
directly on silver. Also i would prefer not to use lead tartarate because i just don't have tartaric acid and for some reason it is quite expensive.
|
|
Antwain
Hazard to Others
 
Posts: 252
Registered: 21-7-2007
Location: Australia
Member Is Offline
Mood: Supersaturated
|
|
Have you tried looking in the supermarket for tartaric acid? In Australia, we can get food grade tartaric acid for ~$2/100g and I can't see why it
wouldn't be available everywhere. Its usually near the baking supplies or herbs and spices. If your only shortage is tartaric acid then this may help.
|
|
hashashan
Hazard to Others
 
Posts: 255
Registered: 10-10-2006
Member Is Offline
Mood: No Mood
|
|
Never seen it here.
|
|
dann2
International Hazard
   
Posts: 1523
Registered: 31-1-2007
Member Is Offline
Mood: No Mood
|
|
Quote: | Originally posted by hashashan
Sorry for reviving a dying thread,
Anyone knows any way to make an alpha lead dioxide coating? I don't want to electrolyze lead in H2SO4 because i need this alpha layer to be plated
directly on silver. Also i would prefer not to use lead tartarate because i just don't have tartaric acid and for some reason it is quite expensive.
|
Hello,
It would be a pity to let the thread die!
This may help.
http://www.geocities.com/CapeCanaveral/Campus/5361/chlorate/...
Dann2
|
|
chloric1
International Hazard
   
Posts: 1147
Registered: 8-10-2003
Location: GroupVII of the periodic table
Member Is Offline
Mood: Stoichiometrically Balanced
|
|
Suppliers of wine making materials carry tartaric acid. If you are adventurous, and I am still considering this, by cream of tartar and neutralize
with the appropiate amount of sodium or potassium carbonate. Then when everything is in a clear solution add a soluble calcium salt to precipitate
calcium tartarate. When this is thoroughly washed and dried, prepar a dilute (10%) sulfuric acid solution with the exact stochiometric amount of
sulfuric acid and heating with constant stirring for about 2 hours. I would heat to boiling or just under. The resulting calcium sulfate should
consist of large enough crystals to be easily filtered. Concenrate said filtrate until crystals start to form then chill. Tartaric acid is VERY
soluble in water so I do not know how hard this is. Also, adding alcohol to the concentrated solution may help.
Fellow molecular manipulator
|
|
hashashan
Hazard to Others
 
Posts: 255
Registered: 10-10-2006
Member Is Offline
Mood: No Mood
|
|
Hi, did some alpha lead plating, weired thing... i only got a thin brown plating, couldnt get the thick black deposition. Anyone tried to plate alpha?
|
|
dann2
International Hazard
   
Posts: 1523
Registered: 31-1-2007
Member Is Offline
Mood: No Mood
|
|
Quote: | Originally posted by hashashan
Hi, did some alpha lead plating, weired thing... i only got a thin brown plating, couldnt get the thick black deposition. Anyone tried to plate alpha?
|
Hello Hashashan,
Never plated Alpha myself. I used to communicate with a guy who did lots of plating from a Lead Acetate bath, (made from vinegar and Lead metal). It
plated OK but anodes were falling apart. The substate was ceramic.
You cannot plate Alpha onto Graphite for some reason or other.
What is your substrate and bath type.
Dann2
|
|
quest
Hazard to Self

Posts: 75
Registered: 15-9-2003
Member Is Offline
Mood: No Mood
|
|
I've been searching and found patent 4,064,035, and got an idea of making PbO2 with no substrate.
I thought of using iron as base
Quote: |
Examples of substances which satisfy these requirements and which are inexpensive include graphite, titanium, iron and stainless
steel.
|
Quote: |
Where the electrode is desired to be manufactured in a sheet-like form containing no substrate, it can be obtained by first electrodepositing on one
surface of the substrate an .alpha.-PbO.sub.2 layer and then electrodepositing thereon a .beta.-PbO.sub.2 layer by following the procedure described
above, subsequently repeating this cycles of operation to have additional .alpha.-PbO.sub.2 layers and .beta.-PbO.sub.2 layers electrodeposited
alternately until the combined thickness of layer reaches a required value (about 10 mm), and thereafter separating the substrate mechanically by use
of a cutter or, if the substrate happens to be made of iron, chemically dissolving out the substrate from the substrate by use of an
acid
|
I made all the bathes for alpha and beta PbO2 plating and a iron anode\cathode.
And then I found this link:
Quote: |
Ions that are bad news in a plating tank, according to the literature, are:
Chloride, Cobalt, selenium, arsenic and iron. The only ion that is likely to effect you is iron. If you are using
'crocodile' clamps made of steel to make connections to an anode that is being plated, you must be careful that no corrosion (it is very likely to
form on the damp clamp) falls or gets into tank. Better not to use Iron at all. Not too sure about SS but it has been in a plating
tank and had no corrosion or ill effects reported. Keep Gouging rods out of the tank as them may contain Iron particles.
|
long post for small punch line:
So it is OK to use iron in a PbO2 electrolysis bath?
[Edited on by quest]
|
|
Pages:
1
..
22
23
24
25
26
..
47 |