WFChem
Harmless
Posts: 15
Registered: 1-11-2023
Member Is Offline
Mood: No Mood
|
|
Questions in electroplating
Hi,
I am Chris and recently started off in electroplating. I have some questions because my first plating attempt failed. I dont know if this is the right
sub forum. If so I am sorry.
I want to plate a aluminium inner cylinder wall with a hard coating. For hardness SiC particles are "dissolved" in nickel sulfate. My pretreatment is
cleaning, desmutting, etching with sulfuric acid and a little sodium fluoride. Then zincating, etch again, zincating again, rinse off. I am using only
distilled water.
Current density is 0.02A/cm², pH about 4, operating temperature 40°C. The solution contains also nickel chloride and boric acid according to watts
solution. The solution is agitated continously with a pump and temperature is also controlled with a digital timer. The cathode surface area is about
140 cm². Anode is pure nickel, 8 mm in diameter and 100 mm long.
The coating is adhering quite good so far. I tested it with a hard file and tried to peel off. But the problem is that my anode got extrem roughly as
the cathode did. The anode looks like a file, some pittings and bubbles on it. At the cathode the coating is uneven, build up on edges, build up of
bubbles.
What went wrong here? Is my anode area to small? Honestly I didnt find anything about the anode area. Always its talked about cathode area. I dont use
a anode bag, if this is the cause at all. I assume the sic particles arent distributed enough, agglomerating. I have much settlement on the ground
despite agitating.
Thanks
[Edited on 1-11-2023 by WFChem]
[Edited on 1-11-2023 by WFChem]
|
|
Rainwater
National Hazard
  
Posts: 989
Registered: 22-12-2021
Member Is Offline
Mood: Break'n glass & kick'n a's
|
|
Quote: | But the problem is that my anode got extrem roughly as the cathode did. |
Can you clarify that.
Did your plated piece get pitted, or other wise damaged?
Quote: | recently started off in electroplating |
Not from what you described, sounds like you know what your doing.
Quote: | I want to plate a aluminium inner cylinder wall | difficulty level >>> max
Ok start simple
Double check your current density measurment.
More than once i have had my meter set to the incorrect scale and pumped amps instead of milliamps.
Check and verify the polarity of your electrodes.
Verify your power supply is supplying only DC.
Its common for big rectifier diodes to fail shorted producing a mixed waveform
Those things can cause cathode erosion, and that is supper easy to check.
Now that the easy stuffs covered, thats about all I got.
"You can't do that" - challenge accepted
|
|
violet sin
International Hazard
   
Posts: 1483
Registered: 2-9-2012
Location: Daydreaming of uraninite...
Member Is Offline
Mood: Good
|
|
WFChem, honestly, I'm not sure what your issue could be, deff not an expert. My attempts at electroplating were quite a while ago now. But I found a
lot of time was spent looking for brighteners and levelers or crude approximations from common stuff. Mainly because it took forever or came out
lumpy or not at all. Rainwater probably has much better advice
If your adding SiC powder to plate on at the same time as Ni by capture, you might need a dedicated mechanical stirring? Homogenized
Maybe mask your cylinder in just a bit from the edge to avoid the sharp corner. IIRC the polarized region has a hard time with corners and it's
easier for metal ions to approach so thicker deposits.
I really like finishing. Com for metal finish reading. Plenty of information on plating Al, as well as diff grades reacting differently. Quick
search showed comments about silicon and copper contents affecting baths or precautions to be aware of when pickling etc. You seem like you're quite
knowledgeable, maybe you know better sites.
There's another option for aluminum and hard surfacing. High voltage hard anodizing. I came across it while looking up other hard anodized
processes. Said to be able to incorporate adulterants fairly well.
https://www.sciencedirect.com/science/article/abs/pii/B97801...
Seems like I read something about zirconia doped baths... Let me check. No nothing pops up. But this looks like a decent read.
https://www.sciencedirect.com/science/article/abs/pii/S02578...
Best of luck
|
|
WFChem
Harmless
Posts: 15
Registered: 1-11-2023
Member Is Offline
Mood: No Mood
|
|
Hello,
thanks for fast response.
Quote: |
Can you clarify that. Did your plated piece get pitted, or other wise damaged? |
It was like sticking bubbles which were "frozen" inside the nickel matrix. I can rub off the bubbles and it looks cratered then. Isnt blistering the
right term for this? The anode was pitted also, but also had little uneven spots. Its definetely pure nickel, bought it in a plating shop.
Quote: |
Not from what you described, sounds like you know what your doing. |
More or less. Plating attempts before were made with pure nickel. It was just dull because I didnt use brighteners, but had no issues with adhering or
blistering.
Quote: |
difficulty level >>> max |
Indeed. But someone on youtube got this done well, but cant reach this guy. Maybe too busy.
Quote: |
Double check your current density measurement. More than once i have had my meter set to the incorrect scale and pumped amps instead of milliamps.
|
How do you mean? My power supply has an ampere scale and I have checked this with my amperemeter, its just off a few milliamps. For 140 cm² cathode
area I had about 2.8 A. The cathode area was determined with an 1 inch grid. If I reverse measurement the amperemeter shows minus. So I assume it
should be direct current.
Quote: |
If your adding SiC powder to plate on at the same time as Ni by capture, you might need a dedicated mechanical stirring? Homogenized
|
Its stirred by a strong pump. But not really homogenized. As I said despite pumping I got huge settlement on the ground. So the sic density goes down,
generating sludge. Maybe I need a surfactant. Recently read about this to avoid agglomerating. SiC concentration is 25 g/l. If you using more its
getting to thick. I have researched several google patents how to go. This project is quite special and just a few companies still do this. But they
dont help, confidential.
[Edited on 2-11-2023 by WFChem]
[Edited on 2-11-2023 by WFChem]
|
|
semiconductive
Hazard to Others
 
Posts: 326
Registered: 12-2-2017
Location: Scappoose Oregon, USA.
Member Is Offline
Mood: Explorative
|
|
I'm less knowledgeable than others here; I've been experimenting with waterless plating of iron for about two years, now. I've only been able to
plate thin coats of aluminum or titanium on anything; they're very stubborn materials.
But, aluminum anodizing seems like it might be another route you could try, if your present route continues to fail; Sulfuric acid, boric acid, or
other oxidizers, when using aluminum as a (+) anode, will cause a thick layer of aluminum oxide to form that is smooth and uniform. It is also very
porous microscopically, which I figured out the hard way. But that is normal, apparently, and can be an asset; for it is how chemically inert colors
such as Prussian blue can be wiped as a paste into the pores after the aluminum surface is formed. Prussian blue, or other pigments / possibly the
silicon carbide your wanting, can be dropped into vigorously boiling water. The water has the effect of causing the pores to close on the pigment
and seals whatever has gotten into the pores in place. The finish is very smooth and even with excellent wear resistance.
The other thought that occurs to me is that blistering might be caused by contaminants in the cleaning solution. For example, I've occasionally
bought acetone locally where it didn't clean copper surfaces evenly but left tiny dots of 'something' that ruined PCB etching photo-resists. I
imagine the same would happen if I used it in an anodization process.
|
|
vanBassum
Hazard to Self

Posts: 66
Registered: 16-4-2019
Member Is Offline
|
|
Are you trying to plate the inside of a cylinder from an internal combustion engine?
|
|
WFChem
Harmless
Posts: 15
Registered: 1-11-2023
Member Is Offline
Mood: No Mood
|
|
Sorry for late answer.
Yes.
Now it looks I am on the right way. Will let you know when its finish, if any..
[Edited on 8-2-2024 by WFChem]
|
|
Morgan
International Hazard
   
Posts: 1731
Registered: 28-12-2010
Member Is Offline
Mood: No Mood
|
|
A photo would be interesting if you wanted to show what you are trying for. Chromium is the hardest metal, if it would suffice as a coating for your
project.
Study of fabrication and wear properties of Ni–SiC composite coatings on A356 aluminum alloy
https://www.sciencedirect.com/science/article/abs/pii/S00431...
|
|
mysteriusbhoice
Hazard to Others
 
Posts: 477
Registered: 27-1-2016
Member Is Offline
Mood: Became chemistry catboy Vtuber Nyaa
|
|
to plate on aluminum you need to first do zincate bath then finally a layer of whatever metal you want but if its the inside of a cylinder you would
need to fit the anode in the center of the cylinder and have it as an inert electrode and just have excess plating solution salts in the bath.
|
|
WFChem
Harmless
Posts: 15
Registered: 1-11-2023
Member Is Offline
Mood: No Mood
|
|
I will show a photo when its success. Hope it will not fail.
|
|
clearly_not_atara
International Hazard
   
Posts: 2828
Registered: 3-11-2013
Member Is Offline
Mood: Big
|
|
I'm confused? Isn't the anode supposed to corrode? It's pitting because it's not noble enough to evolve O2 or Cl2. Maybe you could get no corrosion
using a formate bath?
|
|
semiconductive
Hazard to Others
 
Posts: 326
Registered: 12-2-2017
Location: Scappoose Oregon, USA.
Member Is Offline
Mood: Explorative
|
|
Quote: Originally posted by clearly_not_atara  | I'm confused? Isn't the anode supposed to corrode? It's pitting because it's not noble enough to evolve O2 or Cl2. Maybe you could get no corrosion
using a formate bath? |
That's a curious suggesion. I've tried formate quite a bit, and it works so-so with iron; but I've not had any success with aluminum. Aluminum tends
to make colloidal particles with formic acid in my limited experience.
On the other hand, it might be the formate itself. I've bought it from multiple companies, duda energy, G?? Labs, and I notice that after exposure
to air it slowly darkens in color over a period of months. I wonder what reaction is going on, and if oxygen or nitrogen is being absorbed by formic
acid causing some kind of side reaction.
Do you know why formate (and formate baths) darken over time after exposure to air?
|
|
WFChem
Harmless
Posts: 15
Registered: 1-11-2023
Member Is Offline
Mood: No Mood
|
|
Sure the anode will corrode slowly. But the pitting was extreme. It looked like a rough diamant file Maybe too less anode area. The anode area was just a fifth of cathode area. Maybe I will switch to a basket and fill
with nickel.
The composition of the bath should be right. My second attempt will be with better aggitation.
The adhesion of the first attempt was not bad but not really even. Also the hardness was not as expected. Too less particles trapped.
[Edited on 10-2-2024 by WFChem]
[Edited on 10-2-2024 by WFChem]
|
|
WFChem
Harmless
Posts: 15
Registered: 1-11-2023
Member Is Offline
Mood: No Mood
|
|
Hello,
a little update: In fact it seems the anode area was too small. The anode diameter with 8 mm has a too small surface for a cylinder bore with 58 mm.
Now I have used a round basket, 30 mm in diameter, filled with nickel pieces. The result looks pretty good and the achieved hardness is so high, you
cant almost hone it with silicon honing stones. When you scratch with a file it sounds like you do it on tiles.
But I am not satisfied because the plating is uneven. Not in its roundness, but from the bottom to the top. The basket was just filled half with
nickel pieces. May this lead to that uneven plating? I assume on the bottom you have a nickel enrichment comparing to the top.
The plating was done while agitating the solution.
Is it needed to fill the basket with pieces? Otherwise the solution gets not replenished.
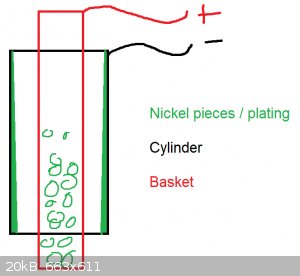
[Edited on 9-4-2024 by WFChem]
[Edited on 9-4-2024 by WFChem]
|
|
semiconductive
Hazard to Others
 
Posts: 326
Registered: 12-2-2017
Location: Scappoose Oregon, USA.
Member Is Offline
Mood: Explorative
|
|
From your drawing, yes, filling the basket with nickel is likely to help even out the plating.
The nickel needs to be nearly equal-distance from all the parts being plated.
Other ways that help plating, are by pulsing D.C. voltage, and rapid circulation of the fluid by a pump.
It's diffusion which is your enemy.
Ultrasound, stirring, etc. anything which speeds up chemical dispersion will help.
But at the end of the day, the closer a surface is to the nickel ... the more nickel should be expected to be plated, there.
|
|
WFChem
Harmless
Posts: 15
Registered: 1-11-2023
Member Is Offline
Mood: No Mood
|
|
Hello,
thanks for your answer. I will test it again with a full basket and try to pump through the cylinder.
Indeed, homogenity is quite difficult on this job.
[Edited on 9-4-2024 by WFChem]
|
|
Rainwater
National Hazard
  
Posts: 989
Registered: 22-12-2021
Member Is Offline
Mood: Break'n glass & kick'n a's
|
|
Plate thick, machine later. Even with a perfect platting distribution to the eye, those tolerances wont be meet. Throwing power needs to be increased.
polyethylene glycol works miracles plating copper sulfate.
Google "The Assaf Cell". It demonstrates an easy way to test the throwing power of your mix.
Attachment: 01may127.pdf (65kB) This file has been downloaded 229 times
[Edited on 10-4-2024 by Rainwater]
"You can't do that" - challenge accepted
|
|
WFChem
Harmless
Posts: 15
Registered: 1-11-2023
Member Is Offline
Mood: No Mood
|
|
Quote: Originally posted by Rainwater  | Plate thick, machine later. Even with a perfect platting distribution to the eye, those tolerances wont be meet. Throwing power needs to be increased.
polyethylene glycol works miracles plating copper sulfate.
Google "The Assaf Cell". It demonstrates an easy way to test the throwing power of your mix.
[Edited on 10-4-2024 by Rainwater] |
Hello,
this is interesting. Pulsed DC current. My power supply cannot not do this, unfortunately.
But dont you think that a full basket will avoid plating just from the bottom to the middle?
I am aware that you cannot plate a finished cylinder bore. Honing is always needed.
[Edited on 10-4-2024 by WFChem]
|
|
Rainwater
National Hazard
  
Posts: 989
Registered: 22-12-2021
Member Is Offline
Mood: Break'n glass & kick'n a's
|
|
Even distribution of the anode and cathode surface area(filling the basket) will likely help alot, but is not the only solution available.
Quote: | My power supply cannot not do this, unfortunately. |
Unfortunate for you? Naa this is science madness
2 10amp channels, or wire in parallel to make 1 20amp channel. Control up to 36 volts.
Highly recommend a current controlled power supply. Under high current youll need additional cooling(fan)
https://www.amazon.com/Sabertooth-Regenerative-Driver-Bridge...
Logic level voltage can be 3.3~20V controlled through any number of ways, rc discharge circuit, 555 timer, plc, light switch, or a arduino.
https://www.amazon.com/HiLetgo-ESP-WROOM-32-Development-Micr...
This little bugger will give you wifi and can do data logging for you. Built in adc, you can add a shunt resistor and accurately measure current.
How far do you want to go, 30 bucks goes a long way?
[Edited on 10-4-2024 by Rainwater]
"You can't do that" - challenge accepted
|
|
WFChem
Harmless
Posts: 15
Registered: 1-11-2023
Member Is Offline
Mood: No Mood
|
|
Okay. I will try this also. Maybe there is another device on the market with housing and not the platine alone. 30 bucks is nothing. This is a hobby
and when it helps?
The question here is the expecting plating thickness depending on frequency, current density and time. My plating handbook shows only expected
thickness without pulsed DC at difference current densities and time.
[Edited on 11-4-2024 by WFChem]
[Edited on 11-4-2024 by WFChem]
|
|
Rainwater
National Hazard
  
Posts: 989
Registered: 22-12-2021
Member Is Offline
Mood: Break'n glass & kick'n a's
|
|
Ive got 4 factories that use these type of setups, each a home brew, +100amp system. But all basicly consists of a dual rail high current low voltage
dc source, waveform generator, and high power dc current amplifier. This is such a notch market that most folks want something they can just add to
their solution to increase the throwing power. The only benefit i know of with a/c electroplating is you can plate where you cant get with traditional
dc electrolysis. Like inside an enclosed cylinder, through really tiny holes, or pipes.
The method / topology,..... cell design is what I wanted to point out. They can accurately measure the throwing power of a mix.
From my experience using a/c electroplating, limited to plating cu, pgm, and about 10 others and repairing lead acid batteries, plating time/
thickness is very equivalent to Foward AmpHours - ReverseAmpHours under sub hertz conditions with the Foward time is greater
than 1.5-2x the reverse amp hours.
My "go to" is about 10 seconds at 100% current, then 2 seconds 300% reverse current, then about a second off time under mixing.
This will eroded dendrites and help stop them form forming, keeping plating more uniform.
TLTR Warning
Dont bother reading this little bit here, skip to the end...
There are strong factors that affect this... affect, effect... eye wood like too think pub-lick school and all my teaches for they're years of wasted
effort.
Sorry,
the factors include
Average Current Density - like AmpHours divided by surface area
Peak Current Density - this is a good one. Its what causes the grow of dendrites. As the little bugger gets closer to the anode, it is the path of
less impedance, so it absorbs more current, throwing off the calculated average current density.
Please note, least impedance, not least resistance, we have removed ourselfs from the relm of dc and entered into ac and a/c with a dc offset, most
difference will be negotiable at these frequencies, but in a minute will become a major issue
Solution saturation - so having a high reverse current for a short burst, will help to saturate the solution around the areas of peak current density,
removing material, forcing it else where, while areas further away, will have less material removed and a more saturated solution available for
plating
Efficiency, or more like the lack there of, from a power prospective. I wouldn't want to know or even bother running the numbers. It should be looked
at as a quality not quantity measurment.
frequency -
Now ive reguartated enough about basics that any textbook will give, the beautiful thing about a/c with dc offset, Is the path of least impedance and
anode placement. Let me set the scene, your an electron on a big hunk of metal plate, and low frequency a/c with dc offset is pushing you around. So
you take the path of least impedance to the source of the voltage, the positive anode, which happens to be the shortest path. Simple enough, but then
someone turns up the frequency to around 2KHz, your path of least impedance is no longer a stright line back to the voltage source, but instead, you
want to couple tighter to where you just where, wore,.... where you just came from. This results in a wider trace/trail/path back to the source.
Instead of a nice tight line, you now have a big open road. Bad analogy but i can not think of another one that does not involve electron field
probability diagrams.
Now lets say the frequency just hit 100KHz we have past the point of benefits for your purpose, but I want to try to explain what would happen. The
electrons, are so tightly tied to the positive path that reaches an area, the positive path begins acting like an anode, even tho its the cathode
material. And the anode is way over there across an ocean of solution. This is how one manufacturer etches their circuit boards for a 0.01 pitch. It
doesnt really etch the material, it kind pushes it to the side and builds up a mound. They dont like the laser cutters and i know their is more to
their process than the few pieces of equipment ive worked on.
TLTR:
Somewhere in there is a sweet spot frequency that will increase the throwing power of your cell without having to increase the throwing power of your
solution. Its cheaper than reagents after the capital cost of equipment, and fine tuneable in ways that chemical mixtures can not be.
A cheaper method, that doesnt have as much control as described ramblings above would be a high current PWM current source.
If you want to spend some $ $ I can try to walk you through building one. If your machineing motors, you have the skill set and tools required.
If you just want to spend some $ $ $ $ you're going to have to hire an engineer because i dont think any company sells these like toasters.
"You can't do that" - challenge accepted
|
|
WFChem
Harmless
Posts: 15
Registered: 1-11-2023
Member Is Offline
Mood: No Mood
|
|
Here is the first attempt. Seems quite good. Tried to scratch, nothing happens. Hard as it should.

Here I have tried to overplate after my fixture collapsed while plating. Seems not working even after reactivate.

[Edited on 13-5-2024 by WFChem]
|
|