metalresearcher - 8-8-2023 at 12:14
Finding a better method to isolate potassium (I did it successfully with KCl + Lithium), I did a a proof of concept by heating a few grams of K2CO3
and powdered charcoal (140:24 stiociometric ratio) in a 10mm I.D. mild steel tube closed at one end to 1200 C which resulted in bright lilac flames
and white (probably K2O) fumes after a few minutes.
That reaction works at 1200 C and does not need Lithium.
So now I repeated it and tried to capture the K metal. I now used a larger stainless (316) retort of 30mm I.D. and a cap screwed on it with a tube
leading into mineral oil to capture the potassium metal, the same retort I used more times successfully with the KCl+ Li method.
I put it into a propane furnace and it started bubbling and after a few minutes. The inside of the propane+air fired furnace got bright yellow hot.
But then the bubbling stopped. So I thought is was ready and removed the retort which was yellow hot, but missing the bottom which was attacked or
molten. There was a few K in the pipe as it reacted with the water leaving a few lilac flames when I dumped the retort in the water.
After the furnace had cooled, I found a frozen blob in the furnace which was clearly metal. I cut it with an angle grinder which indeed showed solid
metal.
Picture:
Top left: the (remains of) the overheated retort
Top right: A new verstion (not used yet, only welded) of the retort, same as the old was, screwed on the distillation pipe, the latter used earlier
successfully.
Center: The blob of frozen SS 316 (was the bottom of the retort) cut by angle grinder.
For comparison a ruler (metric).
My questions are:
Did the charcoal attack the stainless steel and possibly lower the melting point of SS (which is normally over 1500 C) ? But when I removed the retort
it appeared white hot, about 1400+ C.
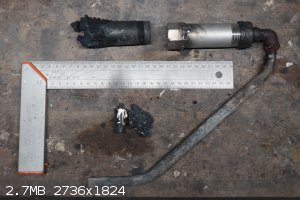
Rainwater - 8-8-2023 at 14:57
As these temperatures, your reactor should be considered a consumable resource. Plan on building a bunch. But you can make them last longer.
Exterior effects
the extreme temperature in an oxidizing atmosphere has corroded the steel from the outside in.
316 is not rated for more than 700c if i remimber correctly.
For example, using a propane burner
By reducing the air intake of your burner until you start seeing yellow/redish flame, exiting your furnace exhaust, you starve the flame of oxygen,
generating carbon monoxide. This will protect the metal from your flame allowing you to exceed the standard operating temperature for that alloy
because your using a reducing flame.
Using electric heat, you need a more reactive, sacrificial compound that will react with the oxygen
Charcoal is a cheap choice. The coal will use up the oxygen before the steal does.
CO2 gas is another cheap option. But argon works best if you can heat inside a controlled atmosphere
These methods should protect the outside.
the inside is a completely different environment. In industrial practice at these temperatures catholic protection is the standard. Running a small
electrical current through your reactor will provide some protection.
Selection of the anode material is difficult as it will produce contamination of the reaction. By selecting easy to remove materials like carbon, this
could be acceptable.
sceptic - 8-8-2023 at 18:46
I think you're correct about the charcoal lowering the melting point. At those temperatures, in a reducing atmosphere, the steel will be absorbing
carbon from the charcoal. As steel absorbs carbon, the melting point decreases. At the eutectic point, with a little more than 4% carbon by weight, the melting point of steel is 1147 degrees Celsius.
unionised - 8-8-2023 at 23:49
I think you are on course to generate this stuff as the potassium salt, rather than potassium metal.
https://en.wikipedia.org/wiki/Benzenehexol