Intergalactic_Captain - 11-8-2008 at 17:34
This isn't quite technochemistry, but it's close enough I suppose - I'm building an apple scratter for cider making and the only motor I've got
floating around uses split-phase AC at 115v. It will be powered from a single-phase AC 110v line, but I have no idea how to hook it up. The
definitions and diagrams I've seen on split-phase AC make it out to be one half of a center-tapped 3-wire single phase 220v transformer output, which
seems to me to be essentially the same as a single phase 110 volt mains line. However, I don't quite trust this understanding - Any of you electronic
gurus care to offer a better explanation of split-phase AC and help me wire this thing?
12AX7 - 11-8-2008 at 18:43
The split phase (I seem to recall that's what it is) motor I have has two wires and a common. One goes to a motor-run capacitor to a winding, the
other goes to a winding. Power is applied to both live wires. Once spinning, power can be removed from one or the other and the motor will continue
to spin, but torque drops to zero when the motor is loaded. If power is applied to just one winding from a dead stop, the motor will just hum (not a
good idea unless the motor specifically states "impedance protected" on its placard); it can be "hand propped" and will spin in either direction,
since there's no direction information from just two wires.
The phase shift provided by the capacitor is what makes it spin, and unlike induction motors, which use a rather beefy start winding (with a low
quality start, rather than run, capacitor), these motors are apparently designed to run both windings continuously. I guess it's less efficient,
which is why these are usually medium to small sized motors.
Tim
ShadowWarrior4444 - 11-8-2008 at 19:03
Indeed, the term "Split-Phase Motor" refers to the method the motor uses to start moving, and bears no relation to electricity distribution system. It
should run nicely off the standard 110v North American system.
http://www.allaboutcircuits.com/vol_2/chpt_13/9.html
Rosco Bodine - 11-8-2008 at 20:24
It is a simple ~110 AC two conductor line powered motor.
There is no capacitor on it if it is what I think it probably is.
What you have is probably basically this, with some added switching that is application related, which you won't need or will bypass.


It is probably the type motor most commonly used ( and salvaged still good from old clothes dryers ). If it is one of those, it will have a
centrifugal switch on the back of the shaft inside the cover which energizes the start winding below a certain RPM and opens when the motor gains
enough speed to be pulled into synchronous speed by the run winding, and IIRC it will also have an additional set of centrifugally switched contacts
which normallly go to the start button on a clothes dryer which is a momentary button switch, but "latches" the motor in running mode after it reaches
cutout speed. That is a safety feature which only allows the heating elements to energize when the motor is running, which also drives the blower,
to prevent burning out the elements from lost airflow, or creating a fire. The centrifugal switch will make an audible snap during startup as the
motor nears full speed, and will snap again at a much lower speed as it resets after the motor is turned off and coasts to a stop.
[Edited on 11-8-2008 by Rosco Bodine]
12AX7 - 11-8-2008 at 22:28
What is the point of that diagram? There is no stated mechanism for producing the different phase shifts (at stall, the windings look like quite
excellent inductors, so they'll both be nearly 90°). If there were a resistor in series with one, there would be a small lagging shift on one, and
it's my understanding that some motors do use this method. Obviously this doesn't generate much torque (the phase difference is small) and wastes a
lot of power (hence the switch).
As stated, my example motor has a run capacitor and no centrifugal switch that I know of.
Tim
Rosco Bodine - 11-8-2008 at 22:44
But the thread started with asking about a split phase motor , not a permanent split capacitor (capacitor run motor) nor a capacitor start / capacitor
run motor , and those are different configuration motors.
The start winding IIRC is physically oriented rotated some degrees so it forms leading poles to the run windings, and the start windings are finer
wire which adds resistance and increases the phase between those windings. It works something like a shaded pole for starting, but develops a higher
starting torque, probably intermediate between the torque of a PSC and a capacitor start motor. They are pretty common for medium duty appliance
applications like clothes dryers and some clothes washers.
http://books.google.com/books?id=99xxCjXFbnEC&pg=PA75&am...
[Edited on 12-8-2008 by Rosco Bodine]
12AX7 - 12-8-2008 at 10:49
Oh yeah, PSC! I thought it wasn't quite right!
Tim
Mr. Wizard - 13-8-2008 at 07:59
Intergalactic_Captain, is there a specification plate somewhere on the motor? Assuming it doesn't have a capacitor mounted on it's case, it most
likely has a centrifugal switch in it. If you can see inside the motor, it will be a disk with some moveable weights that will allow contacts to open
to the starting coils once it comes up to speed. You usually can't hear the opening noise, but when you shut the motor off, the slowing armature
allows the weights to close the switch and you can hear a distinctive 'click'. You can even put a small pulley and wrap some strong string around it
and spin up the shaft by pulling quickly. When the motor slows you may hear the click. A dirty or gummed up switch will result in the starter
windings staying on while the motor is running. This will result in a thermal shut-off switch shutting down the over heated motor, if it has a thermal
safety switch. If it doesn't you'll soon smell the burned varnish and insulation.
You will need to regulate the load on the motor. If you draw more than it's regulated amperage the motor will overheat, with the same results as if
the starting switch didn't work. You can measure the amperage while it runs with a clamp on AC ammeter. You put the clamp probe around ONE of the AC
wires feeding the motor. If the amperage is less than the rating, the motor will run at full speed and not overheat. If you run the motor with too
much load it will slow it down, and the amperage will go over it's rating and get hot. The way to vary the load is with gears or pulleys. You can
fine tune the load with a variable pulley that effectively changes the size of the pulley as you adjust it. I've found you can go right up to the load
stamped on the case and the motor won't get too hot. If you can keep your hand on the motor for 30 seconds without saying ouch, the motor isn't too
hot.
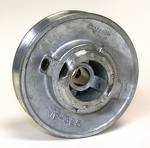
benzylchloride1 - 13-8-2008 at 13:49
This does not pertain to this practicular motor, but pertains to an AC motor for a laboratory mechanical stirrer. I bought a Sargent mechanical
stirrer off of Ebay and the electrical cord was frayed. The stirrer worked extremely well until I went to replace the power cord. I opened up the
motor and replaced the cord by unscrewing the connectors and attaching the new cord. I went to turn the motor on, but nothing happened. Does anyone on
the forum have any experience with a Bodine motor?
Mr. Wizard - 13-8-2008 at 16:23
Benzylchloride. I suspect you have an open connection somewhere. Check for continuity through the motor. You may have broken a wire somewhere. Just a
thought.
Rosco Bodine - 13-8-2008 at 16:46
If it has brushes , you may want to check them too.
Sometimes a brush type motor will lose contact due to a stuck brush or a piece of debris or oxidation, and even a light tap on the housing may jar it
loose and get it going.