Carbon monoxide can also enter the body entirely undetected and the only warning sign is of imminent death is feeling a bit sleepy, but the point in
bold above is important:
"There are 2 mechanisms of injury, hydrolysis and acylation. In hydrolysis, damage
caused by phosgene is due to the presence of a highly reactive carbonyl group attached to 2 chloride atoms. The gas dissolves slowly in water, but
when this occurs, it hydrolyses to form carbon dioxide and hydrochloric acid. This slow dissolution allows phosgene to enter the pulmonary system
without significant damage to the upper airways. However, in the lower airways and alveoli, the tissue undergoes necrosis and inflammation. After the
first few hours of exposure, the carbonyl group attacks the surface of the alveolar capillaries, causing leakage of serum into the alveolar septa. The
tissue fills with fluid, causing hypoxia and apnea. Massive amounts of fluid (up to 1 L/h) leak out of the circulation, leading to a noncardiogenic
pulmonary edema, with associated hypoxemia and volume depletion.
Acylation involves the reaction of phosgene with nucleophilic moieties causing denaturation of proteins, changes in cell membranes, and
disruption of enzymes. The permeability of the blood-air barrier is altered,
leading to interstitial edema, and the inflammatory cascade is activated. This primarily occurs in the bronchioli and alveoli since they are not
protected by a mucous layer."
A member of our own forum died not too long ago as the result of an experiment involving phosgene.
Witness how even DuPont can get it wrong:
<iframe sandbox width="640" height="360" src="http://www.youtube.com/embed/ISNGimMXL7M" frameborder="0" allowfullscreen></iframe>
Rather than building an entirely enclosed and computer controlled storage room, another option they could have looked at would have been enclosing the
cylinders in liners. Such that, if the cylinder began to leak, it would do so through the scrubber. That may have cost significantly less than $2.2M
to implement. It would have also been easier to control the atmosphere around the cylinder it's self (keeping it dry), to prevent hydrolysis and
subsequent corrosion caused by cylinder leaks. Temperature control would have been easier, allowing for better process control.
Any leak occurring would produce a more rapid build up of concentration within the liner due to the small volume for dilution, allowing a detector to
pick up the early signs of failure.
Many of the cylinder companies supply cabinets for storing dangerous cylinders. A lot of these are vented at the top. If the cylinder begins to leak,
it is exhausted through the vent.
A simple vented cabinet (a liner):
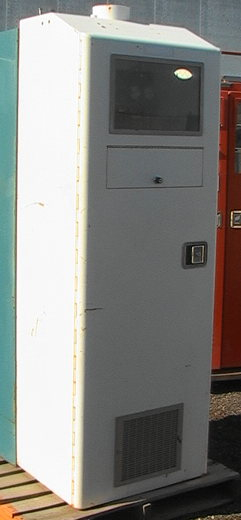
Note the vents attached at the top:

Here's the high tech GasGuard from Air Products (designed to not only store the cylinder and provide a safe venting, but also control the delivery via
an in built computer). I would guess this one is from some form of semiconductor place given it has silane written on the front. An environment where
precise control is required:

These liners are designed for one to three cylinders sat in a lab. For bulk work, as DuPont were doing, they could have built the liners themselves
from large diameter HDPE pipe (or something similar), to save capital on the fancy paint job and pretty aesthetics.
The description of the burst hose doesn't make total sense. Unless they were cooling the cylinders, the phosgene in the hose would be at approximately
the same temperature it was at under normal transfer conditions, and so a similar pressure. There is also an issue with the idea that the guy was
looking at swapping them over knowing that the hose hadn't been correctly purged.
The only way that could be achieved without detaching the still full hose would have possibly been to stand it up (or otherwise get the dip tube out
of the phosgene) and purge it.
Given the weight of them and length of the hoses, a more likely approach would have been to simply disconnect it.
Assuming they don't have flow stops on the ends of the hoses, that would entail exposure to the contents. He would have been partially exposed even if
they did feature stops.
In other words, he should have had a suit on given the problem at hand. Lack of communication perhaps meant he didn't realise precisely what was going
on.
I can offer two other possible causes for the accident (which could involve charges against DuPont if they were true):
- The video mentions the hoses being over exposed. PTFE may be slightly permeable with regards to phosgene, but how readily does phosgene actually
alter PTFE? If hose age is the issue, it seems more likely the phosgene would permeate the liner and then attack the braid. But an alternative
explanation is the hose being damaged by kinking and abuse, due to it dangling in mid air as heavy cylinders are being moved around. Note in the video
at 9.25 that it appears someone has stuck something directly over the point where the hose ruptured, which is either pure coincidence or a previously
damaged spot being covered.
- He was actually sprayed when he was told to unscrew the hose, not realising it was still full and under pressure, without a suit on.
[Edited on 3-1-2012 by peach]