Sauron - 27-3-2008 at 08:08
I have a couple of practical questions.
1. Is it necessary to use a cylindrical vessel, or will a flanged spherical vessel do as well? Spherical is cheaper.
2. I recall reading that the resins used in peptide synthesis stick to the walls of glass vessels unless the vessels have been silylized. Is this a
general problem with many resins? I am planning to polymerize 4-vinylpyridine with divinylbenzene as crosslinker. The reaction is done in dilute
aqueous solution of polyvinyl alcohol with AIBN in toluene as initiator.
3. The literature prep used PVA with average MW 180,000-250,000. I have not been able to find PVA with MW that high. Is this important, or can I
substitute PVA with MW 145,000?
4. The lit.procedure was done on a scale of 25 g PVP resin produced. I want to scale up 4X or more. In scaling up, is the amount of radical initiator
also directly scaled? Or will a smaller multiple work?
DrP - 27-3-2008 at 10:04
"Anyone have Practical Experience with Polymer Synthesis?"
- yes a fare bit. Not with your exact system but with AIBN and toluene with various other monomers and comonomers. Will you have to degass with
Nitrogen or Argon? Probably a good idea if you haven't thought of it. Bubble it through the system for a few mins to get rid of any unwanted oxygen.
Here is what I know from experience rather than text book knowledge - hope it helps:
1 - I don't think it should matter. As long as your consistant using the same shape and size vessel for each of your reactions. (i.e. If you have
been getting consistent yeilds, molecular weights and polydispersities with a certain shape/size flask - thats good, but if you try and scale up using
different glassware you may find discrepencies). In other words as long as you are consistant from run to run you'll be fine.
2 - we used to soak for ages in a base bath (usually IPA/NaOH mixture) - wash well then transfer to an acid bath to soak for more time. Then rinse
rinse rinse and rinse again - then rinse some more. Then rinse a few more times for luck. Apparently this removes surface hydroxyl groups from
the glass. (so we were told - so we done this and did not have any trouble)
3- Sory I don't know - I would guess at not. What is the PVA for? Will it latch on to the polymer you are making and be included in the cross
linking? or is it just part of the solvent system? I don't think the MW will matter either way.
4 - if you use a smaller multiple you will end up with a higher molecular weight in theory ( less free radicals to monomer ratio) - however - I
never found scaling up to be exact (see answer no. 1) . Can you run a couple of tests first to plot, say MW vs Initiator conc. IN THE GLASSWARE YOU
INTEND to do the main run in, then choose your initiator conc. accordingly? As I said - scalling up doesn't always act as predictingly as you would
expect in theory.
vulture - 27-3-2008 at 10:55
Be careful for the gel effect or Trommsdorf effect when scaling up polymerization reactions, especially radical ones. The reaction mixture can become
very viscous, which hampers heat transfer, sometimes causing violent runaway.
This is usually prevented by using a water/hydrophobic mixture where the polymerization takes place in small droplets of solvent, with persulfate as
the initiator in the aqueous phase. This also leads to narrower polydispersity.
Ozone - 27-3-2008 at 20:20
Your PVA should work just fine.
It looks like a suspension (there is no surfactant for an emulsion system) polymerization wherby PVA is used to suspend the developing polymer bits.
This mode negates Trommsdorf effects by keeping the polymerization small (inside the droplet "microreactors") and in the presence, intimately, of a
material with a very large latent heat (water).
Systems like this should scale fine b/c the initator is soluble only in monomer, which is dispersed.
PVA is made via hydrolysis of p-vinylacetate. Vinyl alcohol does not exist as acetaldehyde is much more stable. NaOH in MeOH works quite nicely (large
volume of MeOH dissolves the pVAC then a small amount of NaOH dissolved in MeOH is added with stirring). It turns pink before the PVA falls out of
solution. Wash it with acetone whilst filtering to get a nice powdered product.
The PVA is not involved with the chain polymerization. Just remember that the half-life of AIBN is ~10 her at 80°C. I do not know the initiation
efficiency for vinyl pyridine. Make sure you degas the water before you start--O2 will greatly inhibit polymerizations of this type.
Cheers,
O3
[Edited on 27-3-2008 by Ozone]
[Edited on 27-3-2008 by Ozone]
Sauron - 28-3-2008 at 10:00
An Auspicious Beginning
I need a 4 liter cylindrical Morton (baffled) reaction vessel for this and later polymer preps. Chemglass makes this, price is not so bad.
Also need a matching lid with at least 3 standard taper joints, 150 mm Schott O-ring grooved flange. I found this one on SurplusLab for under $100
(after a 25% discount). So I bought it. This one has 5 24/20 necks, the new ones are over $300 (costing more than the vessel.) Still need a clamp and
an o-ring (PTFE).
Off and running...
[Edited on 29-3-2008 by Sauron]
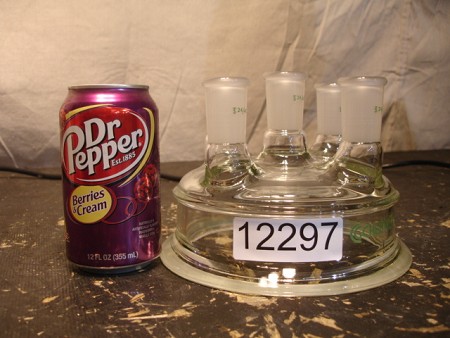
Maya - 28-3-2008 at 17:14
good luck with those o-rings, I keep ordering them to the correct size from leading manfgrs and they are always "wanting in size"
Swany - 29-3-2008 at 13:00
I don't have any experience in polymer prep, but I work in a lab that works with polymerized thiophene derivs. The IPA/NaOH base bath is always full
and re-emptied. I am under the impression that it dissolves a thin layer of glass-- don't put anything with a frit in one, they tend to dissolve. If a
flask sits in it half-immersed, when it is wetted after it has been removed and washed, the surface tension of the water behaves differently on either
side. I think a base bath would help clean everything up nicely.
Sauron - 29-3-2008 at 20:01
There's nothing magical about IPA/NaOH. It is just a caustic cleaning bath. In the lab at my university we had a vat of methanol/KOH or ethanol/KOH
for same reason, and no one was doing polymers.
The downside is that it is about impossible to completely remove traces of the caustic from ground glass joints and this has been known to cause
problems with reactions subsequently run, where some reagents/reactions are very sensitive to alkali.
cbfull - 11-5-2009 at 03:30
I spent 8 years synthesizing various resins. Phenolics, acrylates, polyesters, and occasionally there was the odd caseinate, and many others I can't
even think of.
We rarely ever performed "solventless" reactions because the potential for gelling was just too great. One gelled reaction will likely ruin your
entire apparatus, and might even generate enough heat to result in an explosion.
The amount of catalyst must be tested and profiled before scaling up. For one thing, more catalyst tends to create shorter chains, but a runaway
reaction also becomes much more likely. Too little catalyst and you might never get anything going, ie. the reaction will completely poop out.
I remember one reaction where we used a peroxide as the catalyst, and some type of dithiol was added as a chain length inhibitor. The dithiol also
helped to create a buffer in the event of a runaway. I think the chain limiting dithiol might have been temperature dependent so that if the temp
tried to runaway, the dithiol became more reactive and stopped chain growth.
I was a tech so I just set up and ran the experiments, I didn't get too deep in the chemistry of most of the reactions. I was usually too stressed
out by the assigning engineer to care. Some of the engineers were just delightful to work with, and that's when I would actually learn what was going
on.
I didn't mean to make this thread about me but once I saw the word "practical" I couldn't resist!
I hope this is of some use to you. I'll try to answer any questions you might want to throw at me.
Sauron - 11-5-2009 at 05:54
Thanks!
benzylchloride1 - 11-5-2009 at 18:20
I am also interested in polymer synthesis. I want to prepare some solid phase resins for organic synthesis. I have read that polystyrene can be
chloromethylated and then subsequent reactions can be preformed on the solid to produce the resin with the proper functional group needed for the
synthesis of interested. What would be the best approach? Polymerize styrene and then chloromethylate or obtain a commercial product; styrofoam? The
chloromethylation reaction that I would use would be similar to that used in Vogel for the chloromethylation of naphthalene. I currently own a 2 liter
reaction kettle with clamp, O-ring, and lid with a 24/40 joint and inert gas inlet.
Ozone - 11-5-2009 at 18:40
Wish to make Merrifield's resin do you? Then, with chloromethylstyrene, and DVB (~5%), emulsion (or maybe suspension) polymerize the beads you will.
Unless...
Chloromethyl ether is your thing, then a nice paper is attached, FYI.
Cheers,
O3
Attachment: chloromethylation of styrene.pdf (867kB)
This file has been downloaded 3496 times
Nicodem - 12-5-2009 at 00:07
I'm afraid that styrofoam is not good for preparing the Merrifield polymer resin. It really needs to be a crosslinked polymer to work as solid support
in organic and peptide synthesis, otherwise the granules simply dissolve or swell too much (depending on the solvent used). So unless you want to be
limited to work with a few compatible polar solvents like MeOH or MeCN or aqueous mixtures, you can not use non-crosslinked polystyrene.
Copolymerisation of chloromethylstyrene with divinylbenzene like Ozone suggests would be ideal, but also quite expensive. On the other hand, maybe
crosslinked polystyrene can be bought cheaply or maybe it is used in some products? I have no idea, but chloromethylating crosslinked polystyrene is
described in the paper posted by Ozone. The only problem is that the reagent used is a "no way I'm gonna use that!" type of a reagent, since extremely
carcinogenic and no chemical company is shipping it any more (for example, it is not available in Europe, because it is being produced in the USA and
it is not allowed to be transported - which is a stupidity since BrCH2OMe is still available and its transport is not restricted). I know of a couple
of polymer chemists who died from cancer just because of doing this exact reaction on pilot scale.
Paddywhacker - 12-5-2009 at 12:12
Good luck Sauron, and please report any interesting findings. Making lab-sized batches of custom solid-supported reagents is something I would like
to gain experience in.
matei - 12-5-2009 at 13:36
There is a safer method for chloromethylation of crosslinked polystyrene resins:
J. Am. Chem. Soc., 1990, 112 (22), pp 8187–8188
It uses trioxane, tin tetrachloride and chlorotrimethylsilane, which may not be so easy to obtain, but so is chloromethyl-methyl-ether.
This method can also be applied to chloromethylate soluble polystyrene, whithout promoting crosslinking.
[Edited on 12-5-2009 by matei]
Ozone - 12-5-2009 at 16:23
Thanks,
Stannic chloride is nasty too, but I'd use it any day over chloromethyl ether. Neat route, too. ClTMS is not so bad to handle. For either, a
hood is required. No problem there.
The paper is attached for handiness.
The best thing about buying the resin is the very small, very uniform perfect spheres with homogenous and complete substitution. This allows for
reproducibility and reasonable estimation of loading capacity (so you don't waste expensive precursors).
This would be difficult for any statistically substituted polymer, and substitution will be low (vs. every monomer, every time). The direct
polymerization works well, though, so long as your system is set up correctly (which the manufacturers have spent much time to do) and the stirring is
vigorous. If it works, you will get very fine beads. If it works only so-so, you get an intractable blob.
The resin (sigma) I have is very fine, like a powder. Under a microscope, however, perfect spheres are revealed. Spill a tiny bit and you have it for
life! You can't see the stuff, but your beaker slides across the bench quite miraculously.
The good news is that it can be reused (for peptide work) several times. A one-time investment in some quality material might be (reviewing cost of
precursors/recovery, etc.), perhaps, more cost effective in the long run.
Cheers,
O3
Attachment: merrifield preparation_Itsuno_1990.pdf (286kB)
This file has been downloaded 1479 times
[Edited on 13-5-2009 by Ozone]